Posted at 01:46h
in
Ceramic Foam Filter
by admin
Metallurgical and foundry filters for aluminum refining
PURPOSE: Filter elements for aluminum PEA are designed for fine filtering of all grades of aluminum and its alloys (wrought and cast alloys based on aluminum - silicon (silumins), aluminum - copper (duralumin), aluminum - magnesium (magnalium), special silumin) zinc , magnesium and other non-ferrous metals and alloys, as well as providing additional positive effects on aluminum melts at the request of the Customer.
DESCRIPTION: Filter elements for aluminum FEA are made on the basis of a glass mesh of the brand KS-11-LA or SSF by dipping fiberglass in a special solution, subsequent drying and calcination at temperatures above 600 ºС. This treatment gives the glass mesh rigidity, modifying ability and chemical resistance under the influence of liquid non-ferrous metals alloys with temperatures up to 800 ºС and working time up to 200 s. The filter base is a mesh structure with a surface density of 500 ... 600 g / m2 and filter mesh sizes: 1.0x1.0mm; 1.5x1.5mm; 2.0x2.0mm (1.5mm recommended), filter thickness - 0.8 ... 1.2 mm. Filters for alloys based on aluminum FEA are supplied in the form of rolls or cut into rectangles of the required sizes (special shape - circle, volume funnel, etc. - as agreed with the manufacturer).
APPLICATION TECHNOLOGY: Filter elements for FEA aluminum are used in the production of color castings in single sand molds and chill molds. To obtain the maximum filtering effect, the filter should be installed as close as possible to the body of the casting. Filters can also be used in the production of investment castings (precision casting), injection molding, and can also be installed in filtration boxes as a high-yield metallurgical filter when pouring metal from the furnace into the intermediate transport bucket (or from the intermediate ladle to the mixer). The shape and dimensions of the filter must correspond to its purpose and are calculated according to the methods based on the specific technological conditions for the production of castings. If in doubt when choosing a size, contact the manufacturer’s technology department.
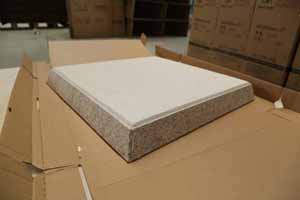
SCIENTIFIC BASES OF EFFICIENCY: The introduction of special components into the filter impregnation composition gives the silica mesh a modifying effect (at the request of the customer), enhanced refining and
degassing ability, increased resistance to high temperatures and other useful properties.
The use of FEA casting filters with a special coating makes it possible to ensure high-quality metal purity with high mechanical characteristics as a result of the following effects on the melt:
fine cleaning of non-ferrous alloys of solid non-metallic impurities and gases due to the implementation of effective filtering mechanisms: mechanical retention of slag inclusions and oxide films with sizes exceeding the cell size, delay of inclusions by the slag layer from the supply side of the filter, including particles of significantly smaller sizes, adsorption of undissolved particles and evolution of dissolved gases as a result of contact of a liquid metal with a filter base and a refractory coating;
modification in silumin of eutectic silicon (eutectic) and alpha solid solution of silicon in aluminum (Al grains), grinding, leveling the structure of color castings as a result of saturation of the melt with effective crystallization, modification centers and alloying elements from the impregnating composition;
the release of inert gases during heating and the use of finely dispersed refractories in the impregnating composition guarantees high thermal and chemical resistance of the filter structure during the entire pouring time, which greatly expands the scope of application of filters based on glass fiber for filtering aluminum-based alloys;
the formation of a laminar metal flow behind the filter contributes to the smooth filling of the mold, while reducing the likelihood of destruction of the mold cavity, as well as the likelihood of the formation of new impurities as a result of reoxidation of the molten metal
EFFECT OF APPLICATION:
a sharp decrease in the number of castings defective due to the presence of non-metallic inclusions, oxide films, slag and gases;
simplification and a significant reduction in the metal consumption of gating systems, as the gating system does not need elements that inhibit the movement of metal and slag traps;
optimization of casting speed, prevention of mold erosion, improvement of surface and quality of castings;
increasing the mechanical properties of the cast structure and achieving better density of castings
ADVANTAGES OF USE:
the variety of execution forms (rectangle, circle, funnel, etc.) allows the use of filter elements instead of expensive ceramic foam, mesh ceramic, chamotte and other filters;
low cost and high quality filtration;
simplicity in technology of use (there are no changes in foundry equipment);
the possibility of using direct technology
[embed]https://www.youtube.com/watch?v=SKW0iofyGko[/embed]