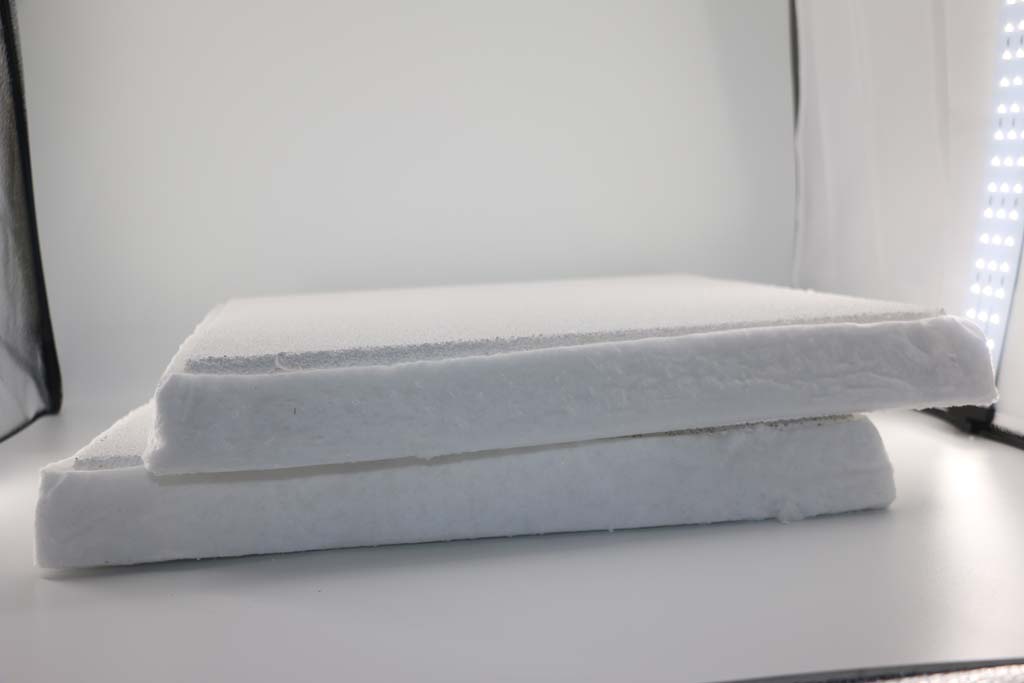
22 12月 Alumina Ceramic Foam Filter
Alumina Ceramic Foam Filter China uses polyurethane foam as a carrier, immerses it in a coating made of ceramic powder, binders, sintering aids, suspending agents, etc., and then extrudes the excess coating to coat the ceramic Coat evenly on the carrier. The skeleton becomes a green body, and the green body is dried and fired at a high temperature.
Ceramic Foam Filter manufacturing process-porosity index
In this standard, the porosity index is determined to be greater than 84%.
The uniformity of holes is used to describe the difference between the actual number of holes per 25.4 mm length in the filter plate product and the theoretically required number of holes.
The smaller the gap, the better the product quality. If the gap is too large, it will cause the Ceramic Foam Filter to reduce the ability of impurity retention or slow melt filtration rate, which cannot meet the production requirements of individual users.
The uniformity of the pores mainly depends on the foam used to produce the filter plate.
The uniformity of the pores of the foam is good, and the uniformity of the pores of the filter plate is good, so the choice of foam is extremely important.
How to choose Alumina Ceramic Foam Filter China
1. There are many impurities and the casting quality is average. You can use a Ceramic Foam Filter with a larger mesh, and add a glass cloth coarse filter in front of the filter plate. At this time, semi-continuous casting is important for coarse filtration using glass cloth. It can cut off the slag from the opening of the furnace eye and wash the slag from the car wash pool to prevent the filter plate from clogging.
2. For castings with high quality requirements, a new type of large-hole Ceramic Foam Filter is used.
3. The specifications of the Ceramic Foam Filter depend on the flow rate and total output of the melt.
4. The color is pure and free of impurities, indicating that the material is uniform. The hands are not sticky, indicating that the surface is not sprayed with adhesive, which will not cause secondary pollution.
5. When buying a Ceramic Foam Filter, you should carefully evaluate the effective specific surface area or porosity calculation of the foam.
You can observe the homogenization state of the mesh surface of the filter plate, and then observe the homogenization state of the cross-section mesh.
If possible, the porosity can be calculated by the drainage method.
The three-dimensional grid is uniform and the porosity is relatively large, which is an excellent ceramic filter plate.
How to use Ceramic Foam Filter? AdTech, the manufacturer of Ceramic Foam Filter, will tell you.
1. Clean the Filtering Housing.
2. Gently put the Ceramic Foam Filter into the housing, and then press the gasket on the Ceramic Foam Filter by hand to prevent the flow of aluminum liquid.
3. Preheat the Filtering Housing and Ceramic Foam Filter evenly to make it close to the temperature of the molten aluminum.
Preheat to remove moisture and facilitate initial transient filtration.
Electric heating or gas heating can be used for preheating. Normally, it takes about 15-30 minutes.
4. Pay attention to the replacement of aluminum hydraulic head during casting. The normal starting pressure head is 100-150mm. When the molten aluminum begins to pass, the indenter will drop below 75-100mm, and then the indenter will slowly increase.
5. In the normal filtering process, avoid knocking and vibrating the Ceramic Foam Filter.
6. After the filtering is completed, take out the Ceramic Foam Filter and clean the Filtering Housing in time.
Sorry, the comment form is closed at this time.