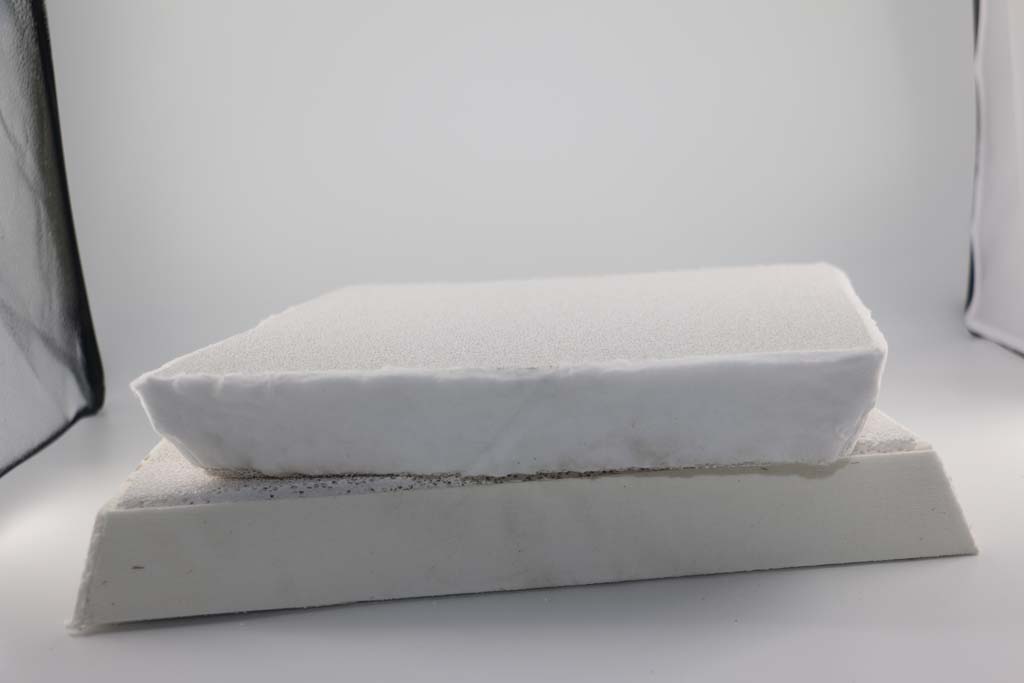
26 2月 Alumina Ceramic Foam Filter Casting Filtration
Alumina Ceramic Foam Filter Casting Filtration can filter out the source of pollution generated in the aluminum casting process.
On the one hand, during the smelting process, aluminum is exposed to the atmosphere in the furnace in a molten or semi-molten state, which is prone to oxidation, reacts with water vapor to absorb hydrogen, and easily forms various forms of non-metallic slag (such as furnace lining fragments, fluxes The chlorides, carbides, etc.) and coarse intermetallic particles and so on.
These impurities often cause bubbles and inclusions in the casting billet, which seriously affect the purity of the molten metal, thereby further affecting the processing performance, mechanical properties, corrosion resistance and the appearance quality of the product.
Alumina Ceramic Foam Filter Casting Filtration has a network hole-like structure, which has a certain strength, can withstand the pressure difference of the metal liquid level and the impact of the metal flow, but is brittle and fragile. Because this material has a precise structure, uniform quality, and Large surface area, so excellent filtering effect.
The production of aluminum ingots consists of bauxite mining, alumina production, and aluminum electrolysis.
The bauxite ore is first mined, and aluminum ore powder is produced through water washing and grinding processes, and then four complex processes such as roasting are used to obtain alumina. There are three main types of bauxite for the production of alumina: gibbsite and monohydrate. Water diaspore, boehmite.
Of the proven global reserves of bauxite, 92% are weathered laterite-type bauxite, which belongs to the gibbsite type. These bauxites are characterized by low silicon, high iron, and high aluminum-silicon ratio, and are concentrated in Africa. West, Oceania and Central and South America. The remaining 8% is sedimentary bauxite, belonging to boehmite and diaspore type, of medium and low grade, mainly distributed in Greece, the former Yugoslavia and Hungary.
Due to the different characteristics of the three types of bauxite, each alumina production enterprise adopts different production processes, mainly including Bayer method, soda lime sintering method and Bayer-sintering combined method. Generally, high-grade bauxite is produced by the Bayer method, and medium and low-grade bauxite is produced by the combined method or the sintering method. Due to its simple process and low energy consumption, the Bayer process has become the most important method used in alumina production at present, and its output accounts for about 95% of the total global alumina production.
Alumina is electrolyzed to produce aluminum metal under the action of a strong current. This process is called electrolytic aluminum.
No Comments