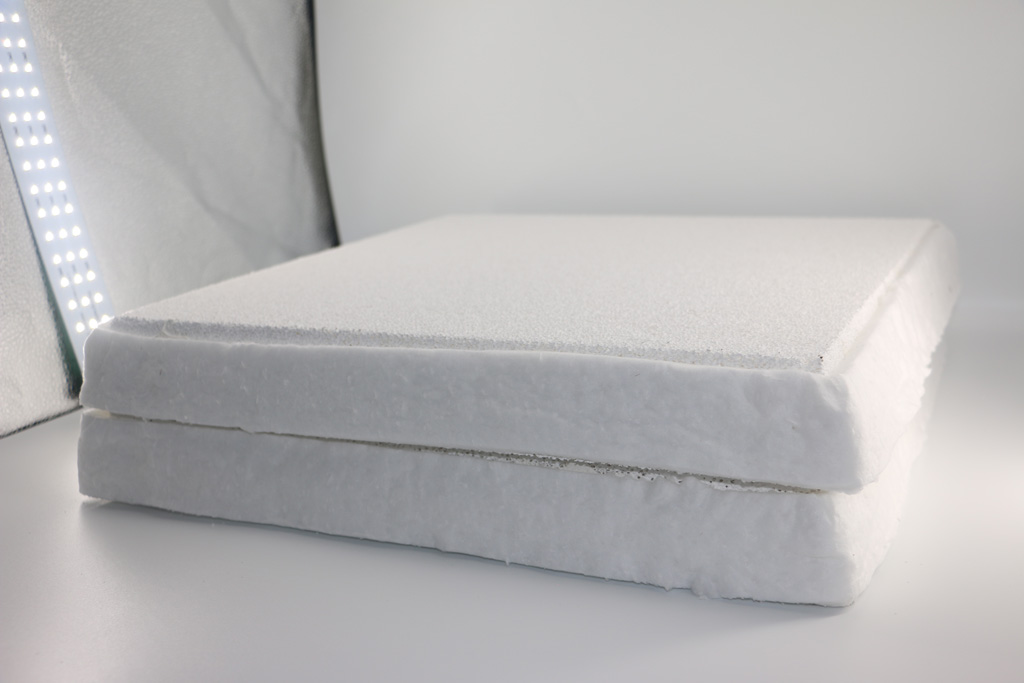
21 2月 Alumina Ceramic Foam Filter Plate
Alumina Ceramic Foam Filter Plate is the most widely used filter in the field of aluminum melt filtration.
Aluminum is a lively metal and is easily oxidized.
In the air, aluminum is easily combined with oxidation to form a dense aluminum oxide film (thickness of about 0.1-0.2μm), with a high melting point (about 2050°C), far exceeding the melting point of aluminum and aluminum alloys (about 600°C) about).
The density of alumina is 3.95-4.10g/cm3, which is about 1.4 times that of aluminum. The surface of the alumina film is easy to absorb moisture.
When welding, it hinders the fusion of basic metals, and easily forms defects such as pores, slag inclusion, and lack of fusion, which cause the performance of the weld to decrease.
The dense oxide film formed immediately on the surface of aluminum in dry air prevents the aluminum from further oxidation and is resistant to water.
But aluminum powder mixed with air is extremely flammable.
Molten aluminum can react violently with water.
Many metal oxides can be reduced to corresponding metals at high temperatures.
Aluminum is amphoteric, that is, it is easily soluble in strong alkalis and also soluble in dilute acids.
Alumina Ceramic Foam Filter Plate can remove oxides on the surface of aluminum, thereby improving casting quality. Today, more and more aluminum plate and aluminum foil manufacturers are using these ceramic filters.
The advantages of Alumina Ceramic Foam Filter Plate are high porosity, high filtration efficiency, easy replacement, low cost and strong adaptability. It can also be separated by filtering solid inclusions in liquid inclusions; the disadvantages are low high temperature strength and short life ( Mostly for single use) The filtering volume is small.
Adtech is one of the largest foundries and a supplier of ceramic foam filter products to the Indian and global industrial markets. The company provides these high-quality filters to customers involved in the production of aluminum plates and foils.
The treated aluminum alloy is light and tough.
Aluminum has excellent corrosion resistance (especially oxidation, because its oxide aluminum oxide increases the corrosion and heat resistance of aluminum).
The main cause of pores in aluminum and aluminum alloy welding is hydrogen. Because liquid aluminum can dissolve a large amount of hydrogen, while solid aluminum hardly dissolves hydrogen, when the temperature of the molten pool is rapidly cooled and solidified, hydrogen is too late to escape and is easy to be welded. Gather in the slit to form pores.
At present, it is difficult to completely avoid hydrogen holes. There are many sources of hydrogen, such as hydrogen in the arc welding atmosphere, and the surface of aluminum plates and welding wires adsorb moisture in the air.
When the moisture content reaches 20ppm, a large number of dense pores will also appear. When the relative humidity of the air exceeds 80%, the weld will have obvious pores.
The weld has a large tendency to deform and form cracks.
The linear expansion coefficient and crystal shrinkage rate of aluminum are about twice as large as steel, which is prone to large internal stress of welding deformation, and will promote the generation of thermal cracks on rigid structures.
No Comments