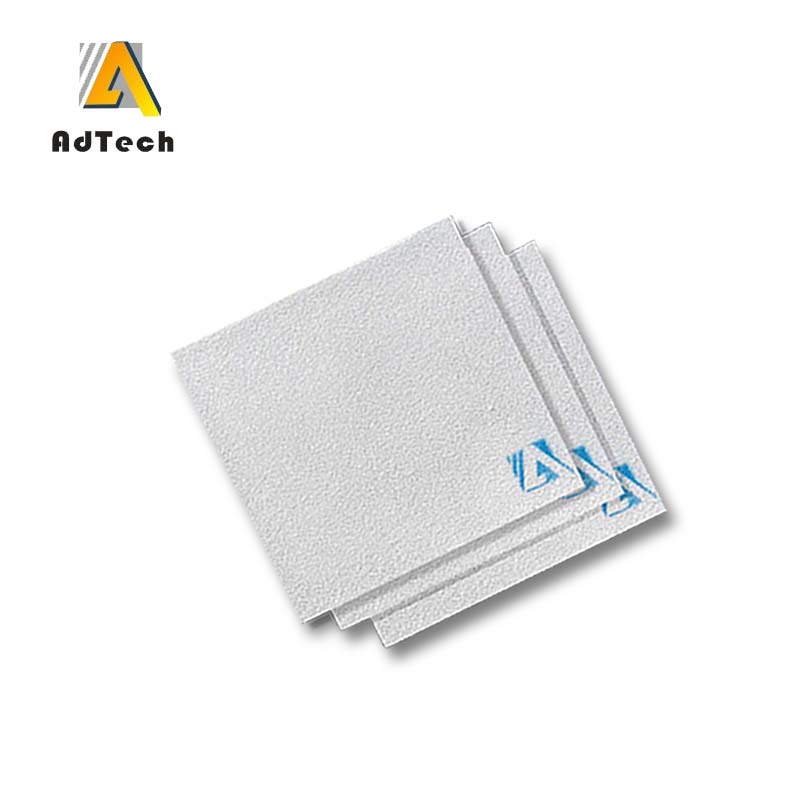
13 8月 Alumina Molten Metal Filter
Alumina Molten Metal Filter
Alumina Molten Metal Filter can effectively remove a large amount of inclusions in the aluminum liquid, adsorb micron-sized fine inclusion particles, improve surface quality, improve product performance, improve microstructure and increase yield.
It is widely used in the production of aluminum profiles, aluminum foil and aluminum alloys.
Alumina Molten Metal Filter production process
The High Quality Foam Filter is connected to the pores as a carrier by a three-dimensional network structure and an organic foam sponge, infiltrated into a special ceramic slurry having thixotropic properties, and uniformly coated with a ceramic slurry by a special roll extrusion process. Covered on the ceramic slurry. Carrier’s skeleton.
Then, it is dried and solidified, and then fired at a high temperature.
Porous Ceramic Foam Filter Foam Ceramic Filter for Aluminum Alloys Since the first study in 1978, foam ceramic filtration technology has developed rapidly.
The porous ceramic foam filter uses a polyurethane foam as a carrier, is immersed in a coating made of a ceramic powder, a binder, a sintering aid, a suspending agent, etc., and then extrudes the excess coating to uniformly coat the ceramic coating. Apply to the carrier.
The skeleton turns into a green body, and the green body is dried and fired at a high temperature.
How to use Alumina Molten Metal Filter
1. Clean the filter box.
2. Gently place the filter plate into the filter cartridge and press the sealing gasket around the filter plate to prevent the aluminum liquid from flowing.
3. Evenly preheat the filter box and filter plate to bring it close to the temperature of the aluminum liquid. Preheat to remove moisture and promote initial transient filtration. Preheating can be carried out using electric heating or gas heating. Under normal circumstances, it takes about 15-30 minutes.
4. Pay attention to the change of the aluminum hydraulic head during the casting process. The normal starting head is 100-150 mm. When the aluminum liquid begins to pass, the indenter will drop below 75-100 mm and the indenter will slowly increase.
5. Avoid knocking and vibrating the filter plate during normal filtration. At the same time, aluminum water should be injected into the water tank to avoid too much interference from the aluminum water.
6. After filtering, remove the filter plate and clean the filter cartridge in time.
Alumina Molten Metal Filter Transmittance
Transmittance refers to the effective filtration area of a foamed ceramic filter plate product.
The higher the light transmittance, the fewer blind holes, the more effective the filter holes (potholes), the better the filtration effect.
Place the ceramic filter plate to be inspected on a light box with a built-in 200W incandescent bulb.
The area of the large surface of the filter plate was measured using a square transparent plastic plate having a uniform 5.0 x 5.0 mm square to calculate the test.
The light transmittance of the filter plate is used to determine the light transmittance of the filter plate.
In this standard, the transmittance (through-hole ratio) of the filter plate is specified to be 95% or more.
Alumina Molten Metal Filter Porosity
Porosity is the percentage of the total volume of the cavity in the filter plate product to the total volume of the filter plate product.
Porosity determines the filtration capacity per unit volume of ceramic foam filter plates.
The larger the porosity, the larger the filtration flow rate of the filter plate and the stronger the filtration capacity.
There are currently two main methods for determining porosity.
One is to calculate the volume of the filter plate hole according to Archimedes’ law, that is, to inject water into the glass beaker with an overflow pipe until the water flows out from the overflow pipe.
When the water no longer flows out, the water will be tested.
All samples were gently placed in water, then water was drained from the overflow tube and the amount of water in that portion was measured.
The volume of overflow water is subtracted from the physical volume of the filter plate, which is the total volume of the holes in the filter plate.
Another method is to determine the true density and bulk density of the sample to be tested, respectively, and then calculate the porosity of the sample according to the following formula.
Both methods have their pros and cons.
The operation method is simple and convenient, and the detection speed is fast, but its fatal disadvantage is that the drainage capacity is smaller than the actual displacement due to the water absorption property of the filter plate material itself. This causes the measurement data to be too small.
Although the testing process of the second method is complicated, the influence of the water absorption rate of the filter plate material is excluded during the test, and the obtained data is relatively accurate.
In this standard, the porosity index is determined to be greater than 84%.
Sorry, the comment form is closed at this time.