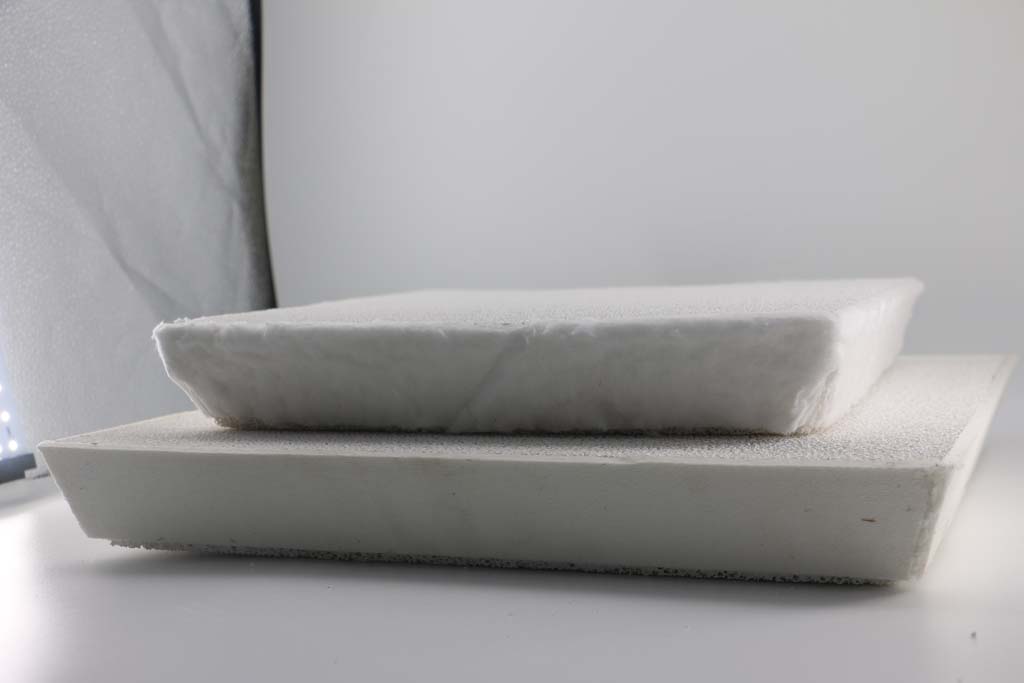
10 5月 Aluminium 7075 Foam Filter Manufacturers
Aluminium 7075 Foam Filter Manufacturers provides ceramic filter plates for aluminum plants, which have a unique three-dimensional interconnected network skeleton structure, with a through-hole rate of up to 80% ~ 90%, strong adsorption capacity, low filtration resistance and high filtration efficiency.
The effect can be achieved by filter cake effect, deep bed effect and distillation scum effect. Filter out large slag particles and micron (10 ~ 40m) fine inclusions in the molten aluminum.
By reducing the number of effective crystal nuclei in the molten aluminum, the molten aluminum can be nucleated and grown under larger supercooling conditions. The grain structure is refined and the sensitivity to internal defects of the alloy is reduced.
7075 aluminum plate is a cold-treated forging alloy with high strength and hardness, far better than mild steel. 7075 aluminum plate is one of the most powerful commercial alloys, with ordinary corrosion resistance, good mechanical properties and anode reaction.
The fine grains make deep drilling performance better, tool wear resistance enhanced, thread rolling more distinctive, and the first choice for metal materials with lower density requirements and higher hardness requirements.
7075 typical use
It is used to manufacture aircraft structures and other high-stress structural parts that require high strength and strong corrosion resistance.
Such as aircraft upper and lower wing surface panels, stringers, bulkheads, etc.
After solution treatment, the plasticity is good, and the heat treatment strengthening effect is particularly good. It has high strength below 150°C.
It has particularly good low temperature strength, poor welding performance, and stress corrosion cracking tendency. Two-stage aging can improve SCC resistance. Provided by Wuxi Hanshin Metallurgy.
Description of Aluminium 7075 Foam Filter Manufacturers
Filtering through alumina ceramic foam filter can remove the harmful alkali metal and alkaline earth metal inclusions that are harmful to the casting structure. At the same time, by filtering solid inclusions, the content of parasitic gas is reduced and the level of tissue pinholes is improved.
Standardize the flow of molten aluminum, adjust the flow rate, and reduce turbulence during filling.
Reduce the high-temperature viscosity of the melt by filtering inclusions, improve fluidity, increase filling and replenishment capabilities, and reduce casting defects.
Reduce the scrap rate, significantly improve the fatigue strength, compression and sealing performance of castings.
Increasing elongation and tensile strength improves the surface finish.
No Comments