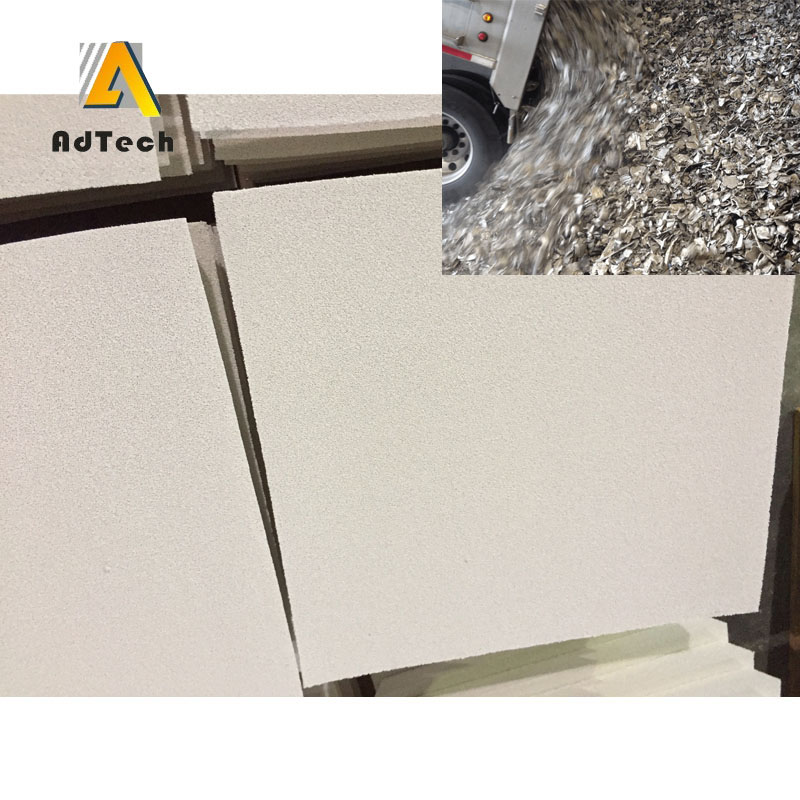
25 6月 Aluminium Continuous Casting Foam Furnace Filter
Aluminium Continuous Casting Foam Furnace Filter
The aluminum liquid sucked from the electrolytic cell contains various impurities, and therefore needs to be purified before casting. In the industry, purification methods such as clarification, flux, and gas are mainly used, and some methods are used for purification by directional solidification and filtration methods.
Foam Furnace Filter adopts adsorption principle for filter, can effectively remove big piece inclusions in molten aluminum, and effectively adsorb tiny inclusions.
No broken bits drop out, effectively reduce the pollution of molten aluminum.
Superior thermal shock resistance, improve erosion resistance ability of molten metal.
Automatic flow production,3 calibration procedures,precision size,fit the filter bowl tightly.
Improve the surface appearance and performance, purify molten aluminum.
Foam Furnace Filter uses a three-dimensional mesh structure and an organic foam body that communicates with air holes as a carrier, infiltrating it into a thixotropic aluminum oxide slurry, and using a square-corrected center distance automatic extrusion The process is such that the slurry is evenly deposited on the foam body skeleton of the carrier, and baked and cured at a high temperature of 1180°C. Installed in the filter box for aluminum alloy liquid impurity filtration, to meet the production of high value-added, high-tech performance aviation, transportation and other aluminum alloy precision casting. Such as: computer hard drives, printing PS base, can making materials, jet turbine engine fan blades and other products.
Foam Furnace Filter Product Advantages
1. Using the principle of adsorption, it can effectively remove large inclusions in the aluminum liquid and effectively adsorb fine inclusions of small size;
2. Do not drop slag, effectively reduce the pollution of aluminum liquid;
3. Good thermal shock resistance and improved resistance to molten metal corrosion;
4. Automated assembly line production, three calibration procedures, accurate dimensions, and more in line with the filter box;
5. Improve surface quality, improve product performance, and improve microstructure.
Aluminium Continuous Casting Foam Furnace Filter Installation
The filtration efficiency of Ceramic foam Filter of the aluminum plant is closely related to its proper installation and use. At the same time, it is not possible to ignore the conventional and necessary measures taken to reduce the occurrence of inclusions in the process operations such as smelting, furnace treatment, and casting, because the filtration process is employed. It is also necessary to prevent re-contamination of the cleaned aluminum liquid after filtration.
Ceramic Filters Features
Effectively remove the inclusions and reduce the scrap rate.
Improve surface quality and product performance.
Improve microstructure.
Aluminium Foundry Ceramic Filters selection and using
In general, choose alumina ceramic foam filter should take into account the requirements of finished product quality, the flow capacity of the molten aluminum tank, the amount of the total filtration of molten aluminum and aluminum liquid cleanliness and other factors.
1. Clean the filter box.
2. Gently put the filter into the filter box, and press the gasket around the filter to prevent the molten aluminum to flow from the side.
3. Even preheat filter box and filter plates, closer to the temperature of molten aluminum casting.
4. Observe aluminum liquid hydraulic head change, the normal initial pressure head is 75-150 mm. When the Alumina liquid began to pass, the pressure head will be reduced to 25 mm below, then the pressure head will gradually increase.
5. After filtration, timely remove the filter plate, clean the filter box.
Sorry, the comment form is closed at this time.