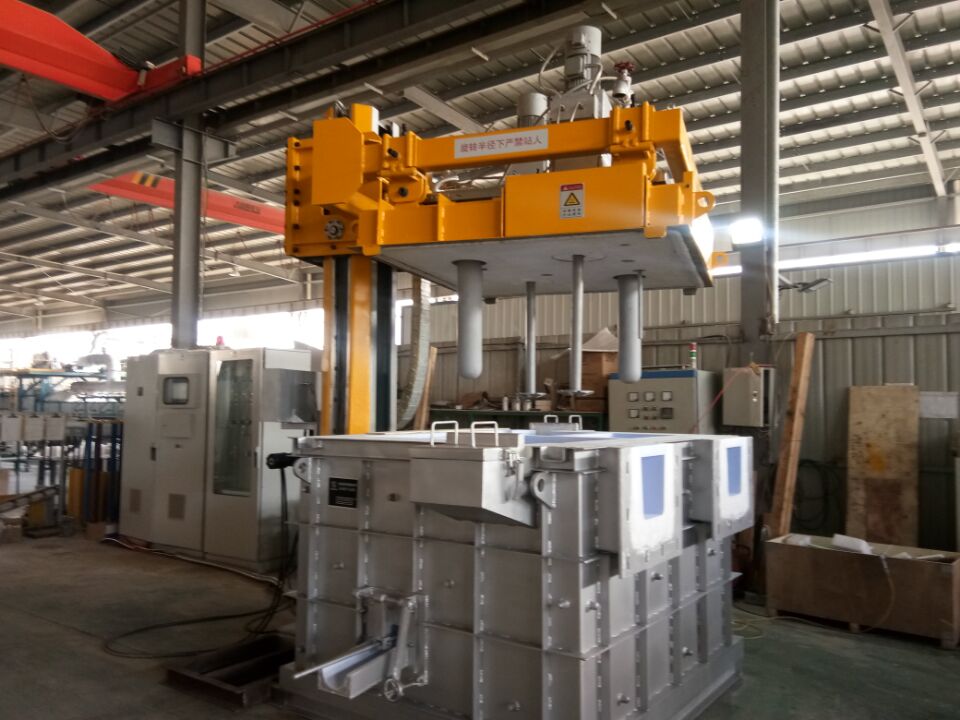
08 4月 Aluminium Degassing Machine
Aluminium Degassing Machine
Aluminium Degassing Machine is used in a fixed position to treat the metal contained in transfer ladles.
The machine is equipped with a rotating graphite tool (Iance), composed by a shaft and a rotor, through which the inert gas (nitrogen or argon) is blown into the melt, in the form of small bubbles. In this way it is possible to eliminate the hydrogen dissolved in the alloy.
In addition, the same treatment allows the removal of the non-metallic inclusions present in the alloy, which are dragged by the gas bubbles toward the surface by effect of flotation.
Si3N4 or Sialon/Syalon material is suitable for molten aluminum liquid degassing pipe and rotor.
In order to remove hydrogen from molten aluminum, a silicon nitride pipe is used to feed nitrogen or argon, while silicon nitride rotor is used to stir up and disperse the gas bubble, and then take the Nitrogen out with the bubble throughout the molten bath, thus get the result of hydrogen remove.
The high-temperature mechanical strength and resistance to contact fatigue of Si3N4 material assures reliable, stable and long operation of rotor in high speed rotation.
Unlike graphite, silicon nitride is hardly volatilized by oxygen at elevated temperature. This permits long operating life. And this character is most popular in the casting industry of aluminum alloy.
High thermal shock performance allows the pipe and rotor to insert in and pull out repeatedly from molten aluminum in operation. Pipes and rotors will not be cracked and damaged. Therefore, operation and maintenance become very convenient.
Excellent corrosion resistance, wear resisting and low wettability, resistance to molten aluminum liquid corrosion makes the operation life longer, and less slagging. If proper maintenance, the using life can be up to 2-3 years.
According to actual working condition, our company is able to make optimized design of rotor impeller structure to achieve better degassing effect.
Dual rotor degassing
1.Dual rotor degassing, with better degassing effects. Independent rotor control to improve degassing effects.
2.Electric lift, convenient for consumable parts replacement. The two rotors can be dismounted separately, convenient for maintenance.
3.Mechanical-electrical separated, remote control available. Special dross removal window, no interfere to degassing.
4.Press control, easy and convenient, manual/auto mode switchable, no man supervision in auto mode.
5.User defined degassing time: 0.01S~999H. Warning light alert and alarm when degassing time ends.
6.Efficiently use of nitrogen or argon, no labor mixing required, less degassing time and degassing automation.
7.High efficiency degassing, more homogenized metal melt.
8.Remarkable degassing effects to raise yielding rate of casting and improve cast mechanical performance.
9.Best rotate speed and gas volume setting available according to the various melts density.
10.Compact and durable, low cost maintenance.
No Comments