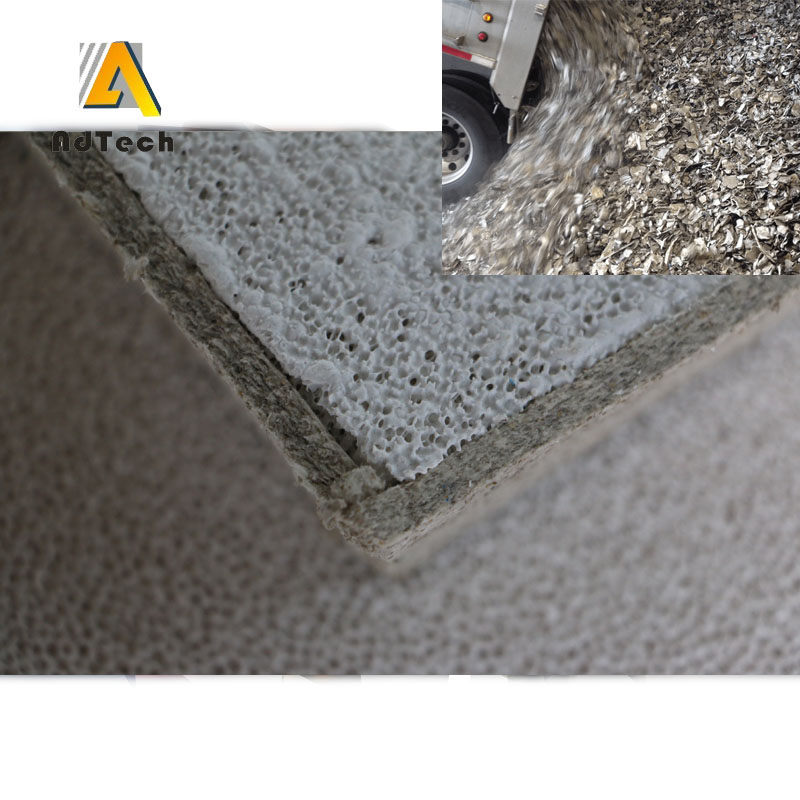
16 5月 Aluminium Foundry Casting Metal Foam Filter
Metal Foam Filter
Metal Foam Filter, also known as foam ceramic filter plate, consists of alumina ceramic filter plate, silicon carbide ceramic filter plate and zirconia ceramic filter plate. Traits: three-dimensional network uniform skeletal structure, pink or white lumps.
Metal Foam Filter use good portiforium foam and high purity ceramic as raw material, can removes non-metal solid mixture from molten aluminium and aluminium alloy fusant effectively in your aluminium casting industry.
Metal Foam Filter Advantages
Ceramic Foam Filter offer the best way to eliminate non-metallic inclusions, foreign materials that are a major source of quality problems in casting. and help you meet ever increasing demands for quality.
Get rid of the impurity, refractory scrap, solid refractory alloy, sinter, in the molten metal liquid when casting the products, get rid of turbulent flow, reduce the air cavity of castings, raise the quality of cast. So our ceramic foam filters (foamed ceramics) are widely used in the aluminum foundry industry, for preventing defects caused by oxides, dross, gas, slag and other impurities.
Eliminates turbulence in the metal stream, Smoothes out metal flow, avoiding sprays, splatter and backset. Improve fluidity, castability, machinability, yield and cost-effective.
Metal Foam Filter Features:
It can effectively remove large inclusions in aluminum liquid and adsorb micron-sized fine inclusion particles to improve surface quality, improve product performance, improve microstructure and improve yield. It is widely used in the production fields of aluminum profiles, aluminum foils, and aluminum alloys.
Metal Foam Filter Instructions
1. Clean the filter box.
2. Gently put the filter plate into the filter box and press the sealing gasket around the filter plate by hand to prevent the aluminum liquid from flowing.
3. Evenly preheat the filter box and filter plate to bring it close to the temperature of the aluminum liquid. Preheat to remove moisture and facilitate initial transient filtration. Preheating can be carried out using electrical or gas heating. Under normal circumstances, it takes about 15–30 minutes.
4. Pay attention to the change of aluminum hydraulic head during casting. The normal starting pressure head is 100-150mm. When the aluminum liquid begins to pass, the pressure head will drop below 75–100mm, and then the pressure head will slowly increase.
5. During the normal filtration process, avoid knocking and vibrating the filter plate. At the same time, the launder should be filled with aluminum water to avoid too much disturbance of the aluminum water.
6. After the filtration is finished, remove the filter plate in time and clean the filter box.
Sorry, the comment form is closed at this time.