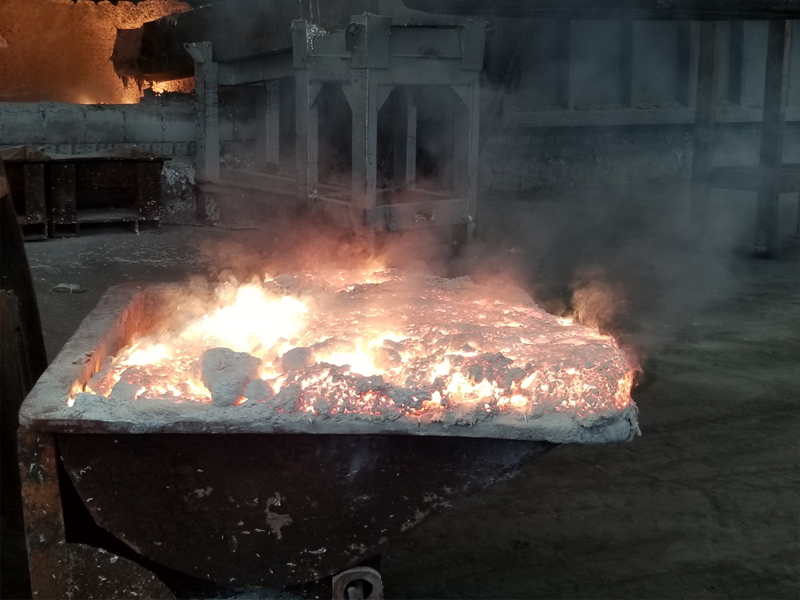
12 6月 Aluminium Refiner
Aluminium Refiner is used in the purification process of aluminum alloy melts. Classification of fluxes. Requirements. Composition of commonly used fluxes. Scope of application and methods of use.
In the smelting process of aluminum and aluminum alloys, hydrogen and oxidized inclusions are the main substances polluting the aluminum melt.
Aluminum can easily produce A1202 or sub-alumina (Al2O and A10) with oxygen.
At the same time, it is also very easy to absorb gas (H) whose content accounts for 70-90% of the total gas in the aluminum melt, and the main defects in the cast aluminum alloy-pores and slag inclusions, are due to the gas and oxidation remaining in the alloy Caused by solid particles.
Therefore, to obtain a high-quality melt, not only the correct and reasonable smelting process must be selected, but also the refinement and purification of the melt is very important.
There are many refining and purification methods for aluminum and aluminum alloy melts, mainly including float method, flux refining method, melt filtration method, vacuum method and combined method.
This article introduces the application of Aluminium Refiner in aluminum alloy melting.
The role of flux
Salt flux is widely used in the production of primary aluminum and recycled aluminum to improve the quality of the melt and the recovery rate of metallic aluminum.
The flux has four functions
1. Change the wettability of the aluminum melt to the oxide (alumina), so that the aluminum melt is easily separated from the oxide (alumina), so that most of the oxide (alumina) enters the flux and reduces the melt The content of oxides.
2. Flux can change the state of the oxide film on the surface of the melt. This is because it can break the strong and dense oxide film on the surface of the melt into fine particles, which is conducive to the hydrogen in the melt to escape through the voids of the particles in the oxide film and enter the atmosphere.
3. The presence of the flux layer can isolate the contact between the water vapor in the atmosphere and the aluminum melt, make it difficult for hydrogen to enter the aluminum melt, and at the same time prevent the melt from oxidizing and burning.
4. The flux can absorb oxides in the aluminum melt, so that the melt can be purified. In short, the removal of inclusions in flux refining is mainly achieved by adsorption, dissolution and chemical interaction with the oxide film and non-metallic inclusions in the melt.
Flux classification and selection
Refining Flux classification and requirements
There are many types of fluxes used in aluminum alloy smelting, which can be divided into covering agents (fluxes to prevent oxidative burning of the melt and gettering) and refining agents (fluxes for degassing and inclusion removal). Different aluminum alloys are used The covering agent and refining agent are different. However, any flux used in the aluminum alloy melting process must meet the following conditions.
1. The melting point should be lower than the melting temperature of the aluminum alloy.
2. The specific gravity should be less than that of aluminum alloy.
3. Can absorb and dissolve the inclusions in the melt, and can remove the gas from the melt.
4. It should not play a chemical role with the metal and the furnace lining. If it interacts with the metal, it should only produce inert gas that is insoluble in the metal, and the flux should be insoluble in the melt metal.
5. The hygroscopicity should be small and the evaporation pressure should be low.
6. Should not contain or produce harmful impurities and gases.
7. To have proper viscosity and fluidity.
8. Easy to manufacture: cheap price.
Flux composition and molten salt discretion
Aluminium Refiner is generally composed of alkali metal and alkaline earth metal chloride and fluoride, and its main components are KCl, NaCl, NaF. CaF,. , Na3A1F6, Na2SiF6, etc. The physical and chemical properties of the flux (melting point, density, viscosity, volatility, hygroscopicity, and interface with oxides, etc.) play a decisive role in the refining effect.
Chloride
Chloride salt is the most common basic component in aluminum alloy flux, and the mixed salt of 45%NaCl + 55%KCl is the most widely used.
Because of their strong wetting ability to solid Al2O3, inclusions and oxide film (wetting angle with Al2O3 is more than 20 degrees) and the specific gravity of NaCl and KCl at the melting temperature is only 1.55g/cm3 and l. 50g/cm3 is significantly smaller than the specific gravity of aluminum melt, so it can spread well on the surface of aluminum melt, crush and adsorb the oxide film on the surface of the melt.
However, for the flux containing only chloride salts, the crushing and adsorption processes proceed slowly, and manual stirring must be performed to accelerate the above process. Chloride has low surface tension, good wettability, and is suitable as a covering agent. Among them, chloride salts with molecular crystal forms such as CCl4, SiCl4, A1C13, etc. can be used alone as purifiers, while chloride salts with ion crystal forms such as LiCl , NaCl wool KCl, MgC12: suitable for mixed salt flux.
Fluoride
Add NaF to the chloride salt mixture. Na3A1F6, CaF2. A small amount of fluorine salt, mainly plays a refining role, such as adsorption and dissolution of Al2O3.
Fluoride salt can also effectively remove the oxide film on the surface of the melt and improve the degassing effect.
This is because:
a) Fluoride can chemically react with aluminum melt to produce gaseous A1F, SiF4, BF3, etc. They mechanically promote the separation of the oxide film from the aluminum melt, and squeeze the oxide film and push it into the flux.
b) The current generated at the interface where the above reaction occurs also causes the oxide film to be “washed” and broken. Therefore, the presence of the fluorine salt significantly accelerates the destruction process of the oxide film on the surface of the aluminum melt, and the hydrogen in the melt can escape more conveniently.
c) Fluoride (especially CaF2:) can increase the surface tension of the mixed molten salt, make the molten salt of the adsorbed oxide spherical, facilitate separation from the melt, and reduce the loss caused by the solid molten slag wrapped in aluminum, and Due to the increase in the surface tension of the flux, the melt accelerates the process of flux adsorption and inclusion.
Sorry, the comment form is closed at this time.