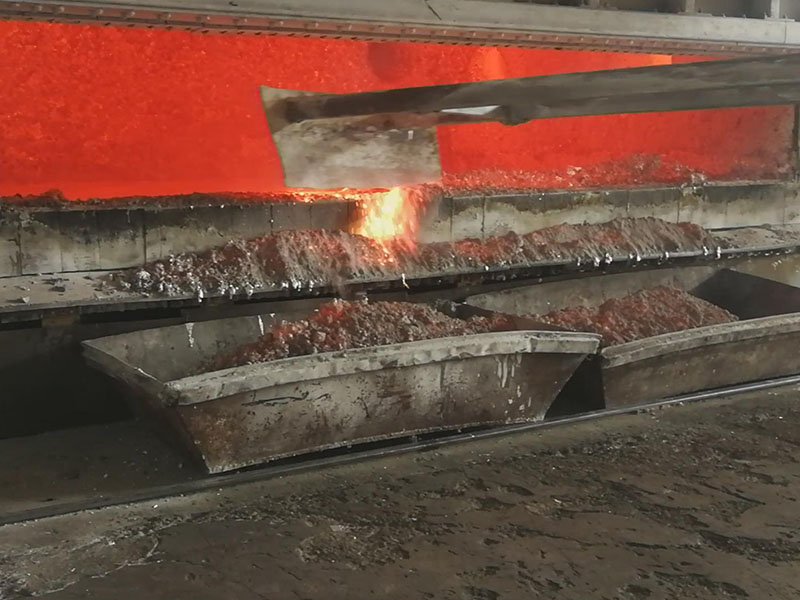
12 6月 Aluminium Refining Agent
Aluminium Refining Agent has a good effect on the discharge of non-metallic inclusions. However, in addition to the physical and chemical properties of the flux, the degree of purification of the non-metallic inclusions in the melt depends largely on the refining process conditions , Such as the amount of flux, the contact time of the flux with the melt, the contact area, stirring conditions, temperature, etc.
To refine aluminum alloy melts, hundreds of fluxes have been developed, and chloride fluxes based on sodium and potassium are the most widely used.
For aluminum alloys with low magnesium content, sodium-potassium-based chloride refining agents are widely used. For aluminum alloys with high magnesium content, sodium-containing carnallite-based refining fluxes are used to avoid sodium brittleness.
Composition and function of fluxes commonly used in aluminum alloy melting process in China
Type of solvent, component content,%
NaCl KCl MgCl2 Na3AlF6 Other components Suitable alloys
Covering agent 39 50 6.6 CaF2 4.4 Al-Cu series, Al-Cu-Mg
system, Al-Cu-Si system, Al-Cu-Mg-Zn system
Na2CO385. CaF15 general aluminum alloy
50 50 General aluminum alloy
KCl, MgCl280 CaF220 Al-Mg series Al-Mg-Si series alloy
31 14 CaF210 CaCL244 Al-Mg series alloy
8 67 CaF210, MgF215 Al-Mg series alloy
Refining agent 25-35 40-50 18-26 Other alloys except Al-Mg series, Al-Mg-Si series
8 67 MgF215, CaF210 Al-Mg series alloy
KCl, MgCl260, CaF240 Al-Mg series Al-Mg–Si series alloy
42 46 Bacl26 (No. 2 flux) Al-Mg series alloy
22 56 22 General aluminum alloy
50 35 15 general aluminum alloy
40 50 NaF10 general aluminum alloy
50 35 5 CaF210 general aluminum alloy
60 CaF220, NaF20 general aluminum alloy
36-45 50-55 3-7 CaF 21. 5-4 General aluminum alloy
Na2SiF630-50, C2Cl650-70 general aluminum alloy
40.5 49.5 KF10 can alloy
The content of some flux components varies widely and can be determined according to the actual situation.
First of all, it should be determined according to the content of alloy elements, because the content of the main elements in most aluminum alloys can be changed within a certain range, and secondly, it should be determined according to the content and content of impurities removed.
Therefore, in addition to using the flux produced by the flux factory, it is best for the manufacturer to adjust the flux component ratio according to the composition of the aluminum alloy being smelted to find the best flux composition.
It is not difficult to see from the above various fluxes, when the composition of the aluminum alloy to be melted is determined, the design of the flux composition is firstly the choice of the proportion of the main component (such as chloride), and the second is the addition of components (such as fluoride) select.
After the flux is prepared, it is best to use it after smelting, condensing into pieces, and then crushing, because the effect of mechanical mixing is not good.
Aluminium Refining Agent usage
When smelting aluminum alloy waste, the quality of the waste is different, and the amount of covering agent and refining agent is also different.
Alloys and products Melting furnace Static furnace
High magnesium alloy No. 2 flux 5-6kg/t No. 2 flux 5-6kg/t
Special products except high-magnesium alloy Common flux 5-6kg/t Common flux 6-7kg/t
LT66, LT62, LG1, LG2, LG3, LG4 use common flux, laminated flux dam
Other alloys Common flux 5-6kg/t
Note: 1. In wet areas and wet seasons, the amount of flux should be increased
2. For large-sized round ingots, the amount of flux should also be increased appropriately.
How to use Aluminium Refining Agent flux
Refining Agent method The following methods are commonly used in the production of aluminum alloy smelting
1. The melt is refined in the ladle. First put a package of flux in the ladle, then inject the melt, and stir well to increase the contact area of the two.
2. The melt is refined in the induction furnace. The flux is loaded into the induction furnace, and the flux and the melt are fully mixed by means of the stirring action of the induced magnetic field to achieve the purpose of refining.
3. Refining with a mixer in the ladle or furnace, so that the flux is mechanically dispersed in the melt.
4. The melt is refined in the magnetic field stirring device. This method relies on the electromagnetic force to continuously deliver the melt to the flux-metal interface to achieve active contact between the aluminum melt and the flux. The higher the melt rotation speed, the better the refining effect. ⑤ Electric flux refining. In this method, the melt is passed through the flux layer to which an electric field (on the metal-flux interface) is applied for continuous refining.
Sorry, the comment form is closed at this time.