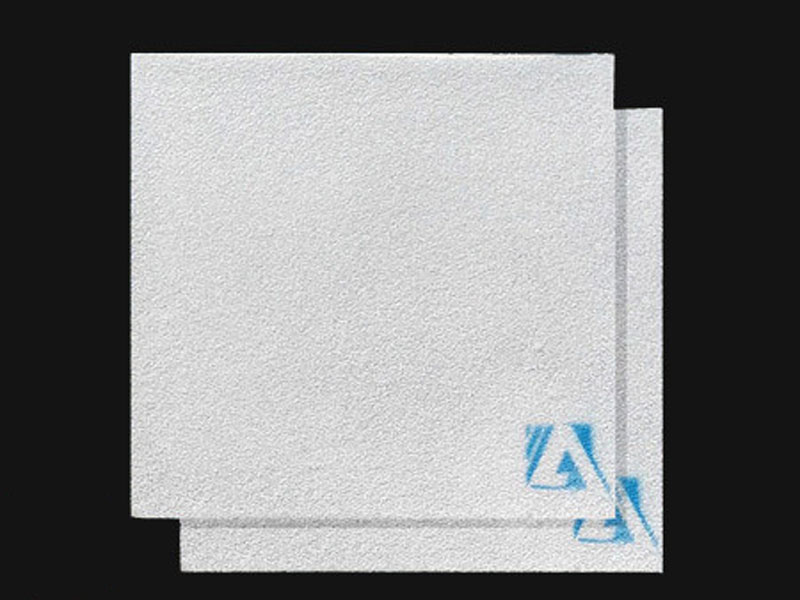
01 8月 Aluminium Scrap Recycling Process
Aluminium Scrap Recycling Process
These can be removed via pre-treatment processes or in the melting furnaces.
Scrap such as used beverage cans (UBCs) and turnings sometimes require the removal of coatings or oils prior to melting, to
improve metal recovery and to reduce potential emissions.
AdTech ceramic foam filter for Aluminium Scrap Recycling Process
Specifications: 7*7in 9*9in 12*2in 15*15in 17*17in 20*20in 23*23in 26*26in, or customized according to customer requirement.
Pore size (mesh): 25 30 35 40 45 50 55 60.
Performance and application:
Filter-PZr filter is produced from high temperature sintering ZrO2 molten material, usable at high temperature, high strength, erosion resistance, minimal volume change, can effectively filter out micron-scale inclusions in molten aluminum, mainly used in aviation, transportation and other aluminum alloy precision casting.
Aperture microgram: (Aperture microgram)
Ceramic Foam Filter Features
-Reduce scrap related to inclusions.
-Reduce costs related to inclusion defects.
-Increase productivity with higher extrusion or rolling speeds.
-Increase casting flexibility with easy alloy changes.
-No holding metal.
The choice of furnaces is to a large extent determined by the level and type of impurities. Scrap refining process can be
generically described with the following steps:
Adtech Refining Flux Application
Fine white ( gray) powder shaped, main components are chloride and villiaumite, and other chemical compound. Been heat and screen treatment,this product has even granularity,which is convenient for boiling kiln.Widely applied for the refining of casting Aluminum / Alloy in reverberatory furnace and holding furnace.
Adtech Refining Flux Performance
The product powder carried by carrier gas ( N , Ar) evenly goes under 2 molten Aluminum through powder spraying boiling kiln, after physicochemical response and forms tiny bubbles that fully access with molten aluminum,and get rid of Hand other harmful gas,moreover, there are some material in the product that can strongly attach or absorb oxides and other impurities
and who carry them to surface,so that purification can be done.
Adtech Refining Flux Advantages
1.Good Liquidity, good performance in deslagging and degassing.
2.Good purification, less pollution, less dosage, low cost.
3.Easy separation of aluminum and slag.
Combinations of different scraps (sized and/or pre-treated) are selected based on the analysis of their alloy composition for charging into the melting furnaces.
In the melting furnaces, salt fluxes are added to cover the molten metal to remove impurities and meanwhile protect metal from oxidisationAfter melting, the molten metal is transferred to holding furnaces for further refining processes such as de-gassing, reduction of magnesium content (a process known as “de-magging”) and for adding alloying elements.
From the holding furnaces, molten metal is either tapped to the casting unit to produce ingot or slabs, or into crucibles for liquid aluminium delivery.
Energy is consumed throughout the refining process. The transformation of scrap into recycled aluminium alloys requires approximately 5% of the energy input needed to produce primary ingot from bauxite. Depending on the impurities in the scrap, various air emissions may be generated, such as organic compounds and dust. Solid wastes such as dross, skimmings and salt slag
can also be generated in the refining process. Dross and skimming are processed, often in the same plant, to recover the metal.
Salt slags are recycled in specialised facilities to recover the metal and other products.
No Comments