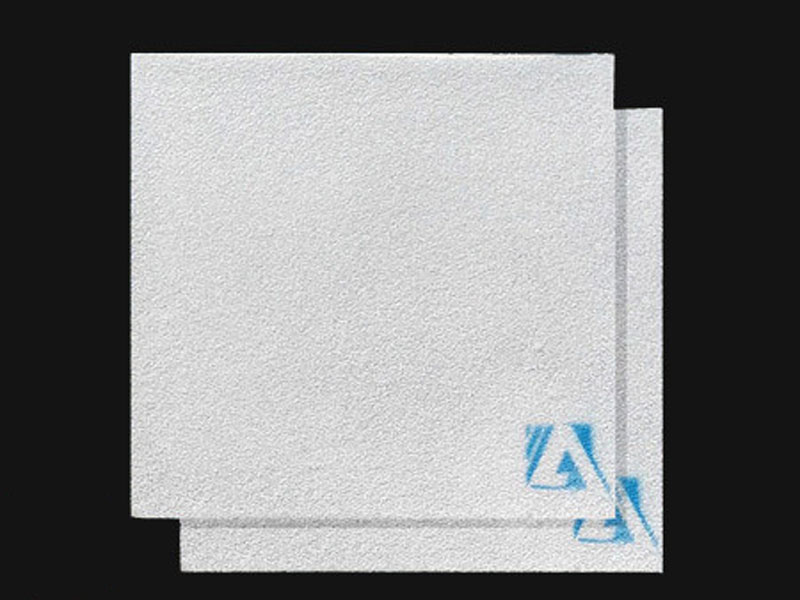
14 8月 Aluminum Casting Using Alumina Ceramic Foam Filter
Aluminum Casting Using Alumina Ceramic Foam Filter
Instructions for Aluminum Casting Using Alumina Ceramic Foam Filter
Inspect and clean the surface of filter bowl, keep it clean and intact.
Gently lay the filter in the filter bowl, press sealing gasket around the filter by hand to prevent molten aluminum from dispersing or floating away.
Use electric or gas burning to preheat filter bowl and ceramic foam filter evenly for 15-30 minutes, make sure their temperature close to molten aluminum. The preheating temperature for ceramic foam filter should above 260℃. Expanding cotton will seal after preheating. This procedure makes ceramic foam filter steady fixed in molten aluminum. Preheating also leads ceramic foam
filter pores open and avoid occlusion caused by thermal expansion and contraction.
Observe the change of molten aluminum height, hold molten aluminum flow in standard needs. Normal starting molten aluminum height is 100-150mm. The height falls down below 75-100mm when molten aluminum flows, and it will slowly increase later.
Do not hit or shake ceramic foam filter in filtration. At the same time, control molten aluminum flow rate in launder, never to be too much or too little.
Take out ceramic foam filter and clean filter bowl in time after filtering.
Features of Aluminum Casting Using Alumina Ceramic Foam Filter
-Reduce scrap related to inclusions.
-Reduce costs related to inclusion defects.
-Increase productivity with higher extrusion or rolling speeds.
-Increase casting flexibility with easy alloy changes.
-No holding metal.
No Comments