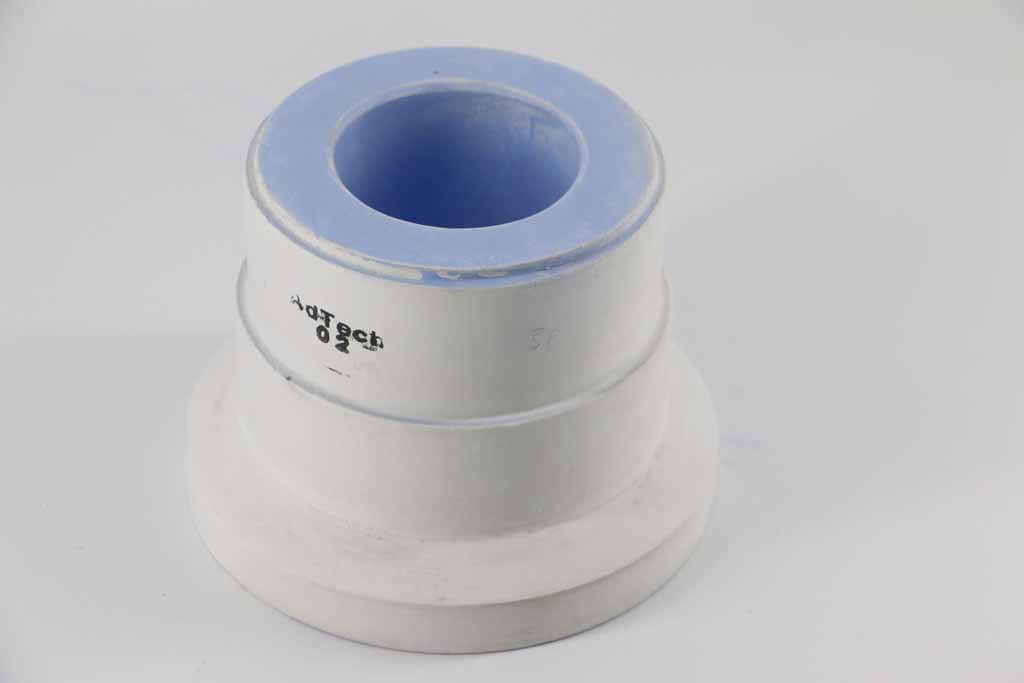
15 3月 Aluminum Rod Refiner
Aluminum Rod Refiner is white (slightly gray) powdery fine particles, the main components are chloride salt and fluoride salt, and there are other compounds. After proper heating and sieving, the particle size is uniform, which is beneficial to the refining tank in the carrier gas (N 2 or Ar) evenly into the lower layer of molten aluminum.
Through physical and chemical changes, countless small bubbles are formed in the molten aluminum to fully contact the molten aluminum, separating [H] and other harmful gases in the molten aluminum.
At the same time, some substances contained in the refining agent can strongly adsorb and melt the oxides and suspended solids in the melt and adhere to the bubbles together, and bring them to the surface of the aluminum liquid as the bubbles rise, so as to achieve degassing and slag removal. Purpose of purification.
It is environmentally friendly and economical, and meets the requirements for the production of aluminum alloy precision castings for aviation and transportation with high added value and high technical performance. Such as: computer hard disk, micron aluminum foil wool, PS board base for printing, canning material, jet turbine engine fan blade and other products.
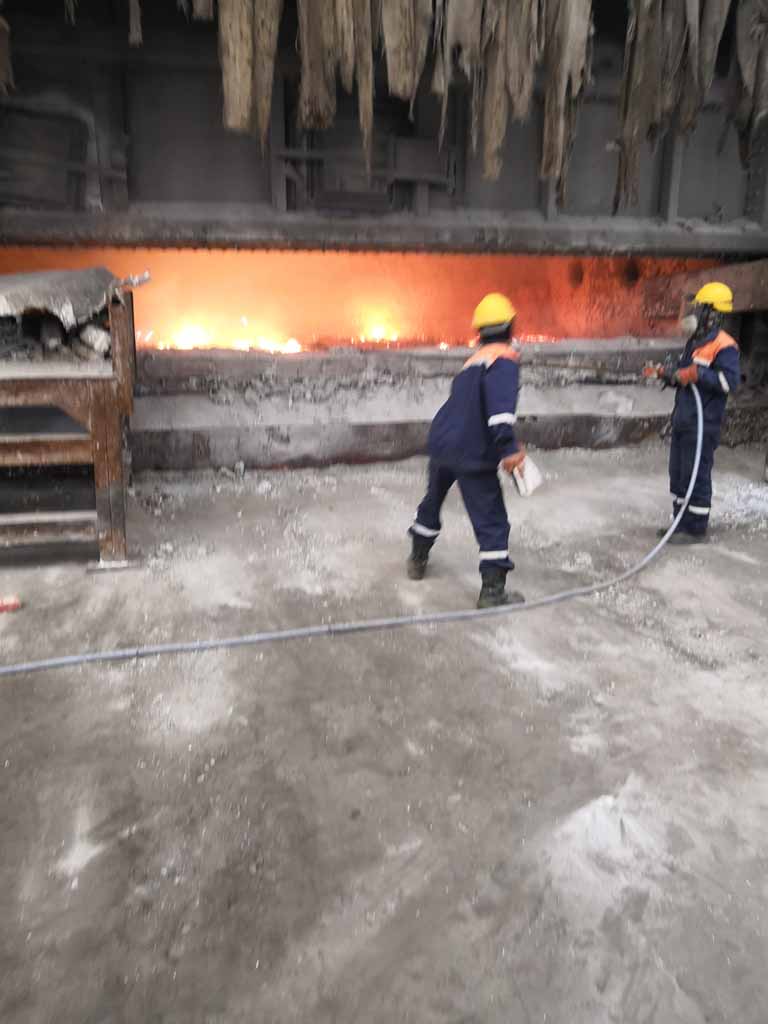
Aluminum Rod Refiner
The unevenness of Aluminum Rod Refiner deposition here means that the amount of Refine Flux deposited in an uneven or uniform manner helps to improve the wetting and spreading characteristics of the molten metal, or is harmful to the process.
By choosing the Refine Flux of aluminum, that is, the melting of aluminum alloy and the flow on the aluminum alloy substrate, restrictions are imposed on the choice of materials to be studied.
It was carried out through multiple hot-stage microscope experiments using aluminum-silicon alloy as a filler metal and potassium fluoroaluminate (Nocolok) as a flux.
Flux is applied in different spatial distribution patterns to reveal the different effects of its distribution on diffusion.
The uneven pattern of Refine Flux deposition shows the effect on diffusion, but the effect is not always conclusive due to the effective diffusion of Refine Flux before aluminum melting and the related ambiguity of the coverage distribution achieved.
It has been concluded that if the diffusion of molten Refine Flux exceeds the distance of the final metal diffusion, then uneven Refine Flux deposition does not necessarily mean that the diffusion of molten liquid metal is uneven or less uniform.
Through the contact angle and spread ratio under different surface conditions, the wetting and spreading conditions of the filler metal on the metal surface are analyzed.
The contact angle is the angle measured between the tangent to the liquid-vapor interface and the solid surface.
At the same time, the expansion ratio is measured based on the diameter change of the expanded shape geometry of the filler metal.
Since the filler metal can reduce the influence of heat on the metal, the use of the low melting point temperature of the molten metal has become more and more common.
However, low diffusion and dehumidification conditions limit the application of filler metals because these conditions have an adverse effect on bonding ability.
However, in general, this study of the different surface conditions of these metals aims to determine the wetting and spreading behavior of filler metals.
In this work, Al-Si-Zn filler metal heated by torch brazing was applied to the surface of AR500 steel and AA7075 aluminum alloy with different types of surface conditions.
The experimental results show that, compared with the rough surface of the metal, the spreading area of ??the filler metal on the smooth surface is larger.
No Comments