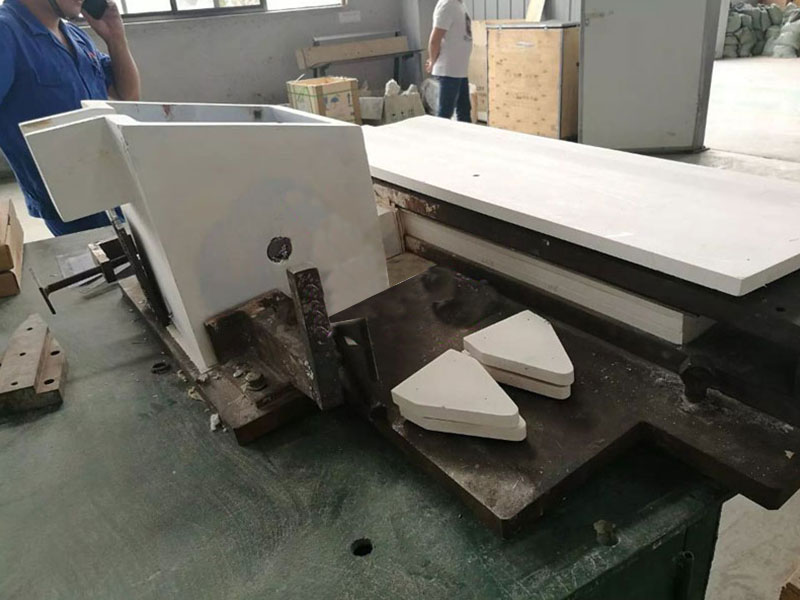
25 12月 Automatic Control of Molten Metal Flow
Automatic Control of Molten Metal Flow
The ways to gain better quality and higher casting performance is an urgent topic among aluminium producers today.
This issue is also often on the agenda at conferences like this and the subjects and technologies to achieve this vary.
Controlling the molten metal flow by maintaining predefined levels or level patterns is one powerful tool on the way to attain this.
Perimeter is specialized in applications for non-ferrous molten metal level measurement and molten metal flow control.
By integration of Precimeter products, any casting machine or process can have automatic level and flow control.
By retrofitting, any existing casting line with traditional technology can easily be upgraded with Precimeter technology and improve casting performance in a cost-efficient way. This paper will focus on the main benefits of automatic level control and how some plants have achieved improvements in their casting process of DC (Direct Chill) slab (or rolling ingot) casting after implementing Precimeter technology.
1. Introduction
When casting slabs there are a lot of different factors and parameters that affect the quality of the product. The cooling system, water flow and temperature, degassing, filtering, melting temperatures, grain refining, casting speeds etc. are all important factors and without any direct relation to metal level control.
However, when we look at, metal distribution, metal transfer, fill rates, cooling optimization and metal solidification, metal level control is a powerful tool that is needed to reduce the shell zone, prevent butt curls and cracks and improve the surface structure.
Metal level and flow control will also enable repetitiveness and traceability through recipes. By accurately controlling the metal level the plant will gain productivity through higher recovery, shorter cycles and less downtime. On top of this, maybe the most important thing of all, operator safety will be highly increased due to atomized start and shutdown operations.
2. Metal Level and Flow control equipment for DC slab casting
A typical fully automatic casting system can consist of ProH metal level sensors, starter dams, pin positioners and a furnace control system (such as a tap-out actuator or a tilting furnace control system). This equipment is easily installed on the existing launder system by local resources or using the flexible Precimeter mounting rig suitable for any launder type and size.
2.1 Sensors
The Precimeter digital camera laser sensor has been developed exclusively to measure on molten metal surfaces. The Precimeter ProH series is specifically designed for high performance in different aluminium (and other non-ferrous metals) applications. Measuring stability and accuracy (typically 0.1mm) with any alloy makes it one of the best-performing sensors for mould level control available on the market today. The Precimeter ProH sensors are being used worldwide by most major aluminium producers and are also integrated by many casting equipment manufacturers in their
casting lines and machines.
2.2 Actuators
To control the metal flow in a DC slab casting machine a pin position actuator is used to adjust the metal flow through the pin/nozzle setup. Adjustment is very precise using stepper motors to control the pin movement in steps as small as 0.01mm. The failsafe design of the actuators by an emergency close function that stops (or opens if desired) the metal flow in any case of power loss or other emergency conditions is another important feature in DC slab casting machines.
Other types of actuators, such as adjustable dams and tap-out actuators are also available to provide complete metal transfer and flow control.
2.3 Metal Level Control Systems (MLC)
A Precimeter MLC system is a control system using high-performing PLC systems, HMI interfaces and computers to control, record and analyze the casting process and metal flow control. The MLC system is easily integrated and combined with existing control systems for casting
machines and various pit utility systems.
2.4 Cast house implementation
Automatic mould level control is available from most suppliers today when purchasing a new casting line or casting machine. For a lot of companies, especially smaller producers, this may lead to heavy investments in replacing all (or parts) of their equipment in their casting line. What everyone
might not be aware of, is that some of the benefits from new casting machines can be achieved with less investment and without replacing any of the existing equipment. By retrofitting your casting machine with Precimeter products for molten metal level control some of the benefits from new
equipment are achieved with increased casting quality as a result.
3. Quality factors
3.1 Low metal head
It is well known that casting with a low metal head minimizes butt curl and reduces shell zones, resulting in superior surfaces and high recovery rates. This results in significant savings in downstream scalping and edge-trimming operations.
3.2 Fill rate control
By controlling the actual fill rate of the mould, the initial filling of the moulds can be optimized to suit the alloy behaviour and the cooling efficiency of the moulds. This will help to reduce material tensions and stress that cause cracks and butt curls. When the perfect fill rate for that specific casting condition is found, the MLC-system casting recipe will store and repeat this through every cast.
Plant example:
One example of reducing cracks by fill rate control is a slab casting plant in the UK. After upgrading from level control by steady eddy to automatic level control with Precimeter products, the number of cracking slabs was reduced from 10% to 5% (casting their most difficult Alloy).
Start table drop
Fig. 6 – Metal level casting curve that adjusts (from recipe) mould fill rate, casting table drop, and metal levels throughout the entire cast.
Fig. 7 – No floaters are needed in the molten metal. Level measuring by non-contact camera laser sensor
By elaborating and adjusting the mould fill rates differently depending on mould sizes (and types) and alloys, the plant managed to reduce the material tensions and stress created at the start of the cast.
Once you find the optimal settings, different recipes for different products enable repetition from cast to cast.
No Comments