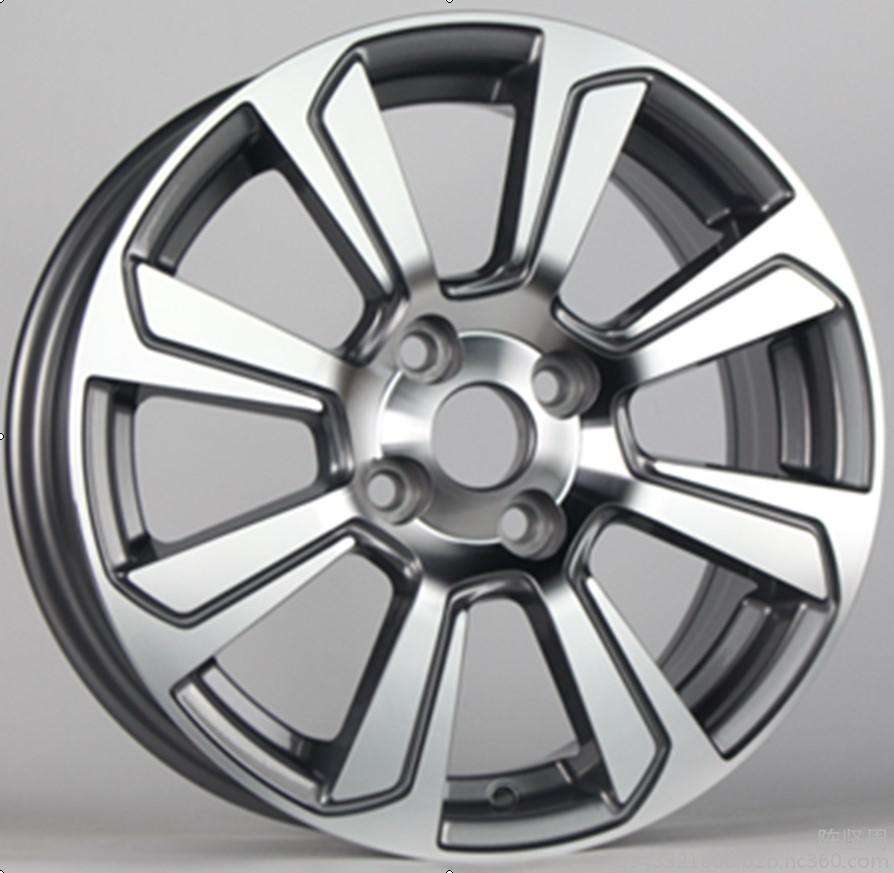
20 12月 Automotive aluminum frame will use adtech ceramic foam filter
Automotive aluminum frame will use adtech ceramic foam filter to get top purification which satisfy the following requirements.
Due to the unique physical and chemical properties of aluminum alloys, a series of difficulties and characteristics will arise during the welding process. When welding aluminum, we must consider its special properties.
1. Aluminum has strong oxidizing ability, and the affinity between aluminum and oxygen is very strong. It is easy to combine with oxygen in the air to form a dense and strong aluminum oxide thin film with a thickness of about 0.1um. The melting point of aluminum oxide is as high as 2050 ° C. It far exceeds the melting point of aluminum alloy, and its density is about 1.4 times that of aluminum.
During the welding process, the aluminum oxide film can hinder the good bonding between metals and easily cause slag inclusion. In addition, the oxide film also absorbs moisture, which can cause pores in the weld during welding.
Therefore, in order to ensure the welding quality, the aluminum oxide layer made of aluminum must be removed during the welding operation, and it is prevented from being oxidized again during the welding process.
2. Aluminum has a high thermal conductivity and specific heat capacity. These two parameters of aluminum are very large, about twice as large as steel. During the welding process, a large amount of thermal energy is quickly transferred to the interior of the base metal. Welding steel consumes more heat.
In order to obtain high-quality welded joints, a heat source with greater energy concentration and greater power must be used.
3. Aluminum has a high tendency to thermal cracks. The thermal expansion coefficient of aluminum alloy is about twice that of steel, and the volume shrinkage rate is 6.5% when solidified. Therefore, when welding some aluminum alloys, it is often due to excessive internal stress.
Thermal cracking occurs in the brittle temperature range, which is one of the most common defects when welding aluminum alloys, especially high-strength aluminum alloys.
To avoid external defects or deformation, pay attention to the high heating and cooling speed when welding. When welding thick or large pieces, preheat and control the cooling of the plate. After welding, cover the plate with a layer of fire The blanket reduces the cooling rate.
In some cases, the stress of the aluminum alloy weld is very large and it will become brittle. To prevent this, it is necessary to hammer the weld with a hammer to eliminate internal stress and increase the strength of the weld.
4. Easy to produce pores. Porosity in welded joints is another common defect that is prone to occur when welding aluminum alloys. Hydrogen is the main cause of porosity in fusion welding. The liquid molten pool of aluminum alloy is easy to absorb gas, and a large amount of gas is dissolved at a high temperature, and it is too late to precipitate in the process of cooling and solidification after welding, and gathers in the weld to form pores.
The moisture absorbed by the oxide film on the surface of the welding material and the base material is the main source of hydrogen in the weld gas. Therefore, it must be cleaned strictly before welding, and the welding process must be properly selected to prevent the generation of pores.
5. No color change. The color of aluminum does not change when heated. Use a temperature indicator when heating to prevent the aluminum material from being subjected to excessive temperatures and deformation. To prevent deformation, overheating must be avoided. When welding long welds, segmentation should be used. Welding prevents overheating.
In the welding of aluminum alloy in the body, the resistance spot welding operation is not used. The resistance of aluminum is about 1/5 of that of iron. When using resistance spot welding to achieve the appropriate resistance heat, the welding current must reach 30,000 amps. It is difficult to reach such a high current.
It requires high energy output. It is replaced by riveting in production and repair. Generally, aluminum inert gas shielded welding equipment is used for welding during repair.
Sorry, the comment form is closed at this time.