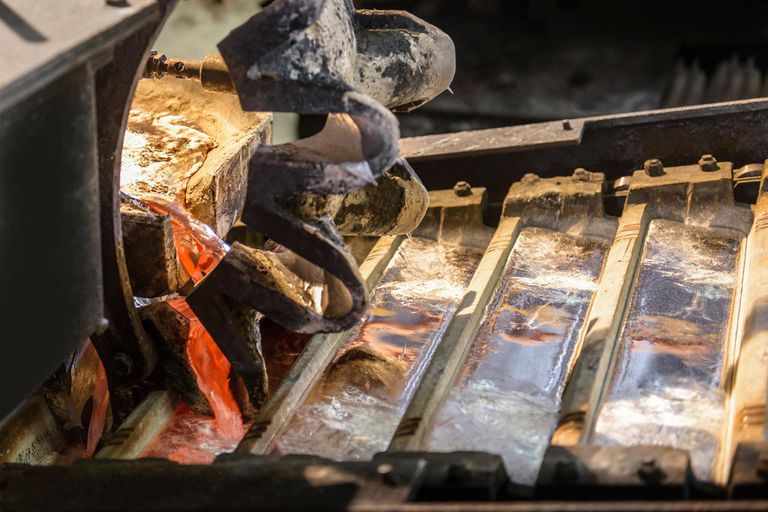
23 6月 Britain China Foundry Filter
Britain China Foundry Filter can effectively remove the fineness of molten aluminum, reaching micron-level inclusions, allowing the molten aluminum to enter a stable laminar flow, which is conducive to punching.
Britain China Foundry Filter is used to purify liquid aluminum plate, strip aluminum foil, and its products (such as tanker blanks, exquisite decoration materials, PS plates, etc.) have brought huge benefits. Manufacturers have the following obvious advantages for aluminum alloy profiles
1. Improve the extrusion survival rate: When the Foam Furnace Filter is used to purify 15% alloy extruded billets, we use specific die tracking and find that the extrusion speed has increased by 20% and the production efficiency has increased by nearly 6063.
2. The service life of the mold is extended, and the number of mold repairs is reduced.
3. Reduce extrusion pressure: When the filter plate is used to purify molten aluminum, the pressure of 6063 is 3% higher than that of non-filtering.
The surface quality of aluminum profiles is significantly improved.
4. The foam ceramic filter has the characteristics of large specific surface area, high mechanical strength, thermal shock resistance, etc.
5. Purification of metallic liquids, removal of non-metallic impurities and gases.
6. The filling of liquid metal is stable and the eddy current is reduced.
7. Simplify the pouring system and improve the process yield.
8.Refractory Molten Aluminum Filtering Medium can reduce the porosity of castings, optimize and refine the metal structure.
9. Improve the surface quality and mechanical properties of castings, and reduce the rejection rate of castings.
10. It can reduce the machining allowance, increase the service life of the tool, and reduce the casting cost.
Inclusions in the matrix affect the fracture process of aluminum alloy specimens
When the specimen is subjected to tensile force, severe concentrated stress appears at the front of the crack. When the tensile stress exceeds the yield strength, plastic deformation occurs first near the crack tip to form a plastic zone, which leads to stress relaxation and blunt crack tip.
As the plastic zone expands, the inclusions at the front end of the crack enter the plastic zone.
Due to the weak bonding force between the inclusions and the matrix, under the action of tensile stress, the inclusions are separated from the matrix to form initial micropores.
As the load continues to increase, the internal necking between the crack tip and the micro-holes intensifies, causing the crack tip and the micro-holes to gather quickly, and the cracks begin to expand forward.
Therefore, inclusions are conducive to the formation of initial micropores and have a greater impact on the propagation of cracks.
The wheel structure of aluminum alloy wheels largely determines the difficulty of low-pressure casting. The reason for the cracks on the surface of the casting is that during the filling process of the casting, the turbulent flow of the molten metal forms secondary oxidation and clamping, resulting in cracks and internal pores on the surface of the casting.
In order to avoid secondary oxidation and retention caused by the turbulent flow of molten metal, reduce the surface cracks and internal pores of the castings caused by this. After testing different models, different models, and different specifications of filters, Aluminum Indonesia finally chose the “20ppi” ceramic foam filter produced by AdTech.
No Comments