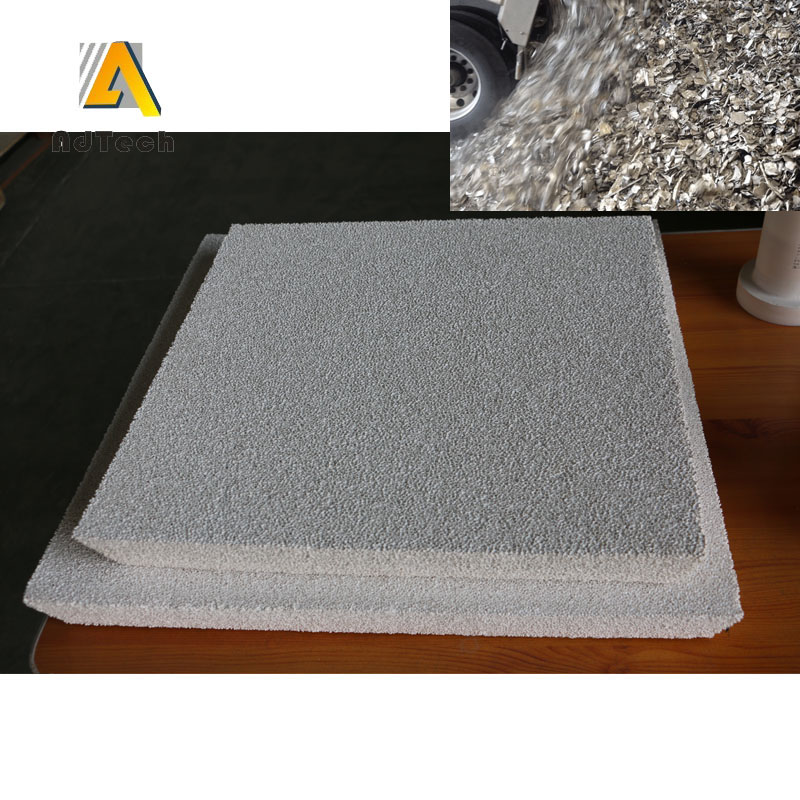
17 9月 Carbide Ceramic Foam Filter
Carbide Ceramic Foam Filter
Carbide Ceramic Foam Filter in capturing primary inclusions whose size exceeds the size of the holes on the supply side of the filter.
In this way, it is possible to capture only large particles, mainly in the form of films.
The formation of a Carbide Ceramic Foam Filter continues the filtering mechanism, when particles of a smaller size are gradually captured by the detained large particles.
The layer of inclusions on the surface of the filter gradually grows, while the flow rate of the metal slows down.
In the end, the filter becomes clogged. Very small inclusions up to 1-5 microns in size are also caught by the filter cake.
Depth filtering is performed by the entire filter volume.
Its principle is the adhesion (sticking) of inclusions to the walls of the channels of the ceramic filter and the connection of individual inclusions with each other.
During deep filtering, inclusions envelop the filter ceramics, individual particles accumulate and form “bridges”, the edges of which are attached to the filter channels.
The probability of particle capture during metal flow through the filter depends on the shape of the channels.
It is smaller in the case of even walls of a circular channel, higher when in contact with several walls of a rectangular channel, and is maximum in the case of non-linear channels of complex shape, providing swirling of the metal and a change in the direction of flow.
Refractory materials consisting of alumina and silica are widely used. Refractoriness increases with increasing alumina content.
Products with an alumina content of 20 … .40% are used as refractory fireclay bricks.
For more severe conditions of use, the amount of alumina increases: ceramics with alumina of more than 71.8% can work up to 1800 ° C.
With an alumina content of 90%, durable, finely granular ceramics are produced for specified mechanical conditions.
With a content of 96%, ceramics are produced that have excellent properties for special purposes in electronics, and with a content of 99.9% – solid, durable ceramics for harsh mechanical conditions and aggressive environments.
Carbide Ceramic Foam Filter Description
Alumina ceramic foam filter is designed as a new type of molten metal filter to reduce casting defect in recent years.
Carbide Ceramic Foam Filter has the characteristic features of light weight, high mechanical strength, large concrete surfaces, high porosity, excellent heat resistance, chemical corrosion and high stability temperature in the molten metal.
With a distributing pore structure, they are able to increase surface area and absorb agglomerate, the liquid metal becomes cleaner, problems with the quality of waste, such as sand pores and air pores, are much smaller, and casting quality is much better.
Function
Ceramic Foam Filter is made of impregnated foam in a controlled open pore structure to provide an excellent filtering effect. We provide an effective solution for the removal of oxides and non-metallic particles from a wide range of non-ferrous metals.
Benefits
Removing inclusions makes the metal more fluid, which facilitates mold filling, a better cast structure and a better thin casting section.
Removing inclusions and other non-metallic waste from the melt reduces the soldering and interaction of the molds with the metal, which affects the surface of the mold and the service life.
Oxide, as well as intermetallic inclusions create “hard spots” that damage tools during processing and finishing work. Filtration reduces tool wear and improves productivity.
The inclusion of nucleic porosity creates hot tears during solidification, causes surface defects that reduce appearance, and often reduces mechanical properties. In many cases, filtration compartments deviate from such causes to almost zero. Improving returns to 100% and lowering the deviation rate to 0% are common.
Sorry, the comment form is closed at this time.