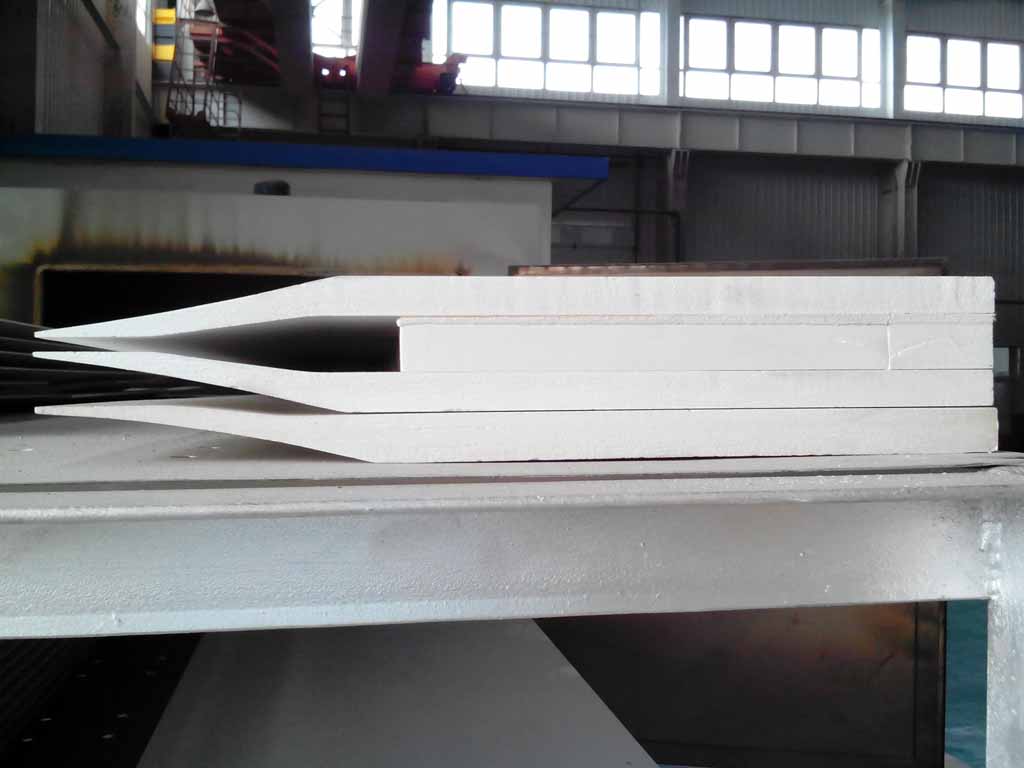
08 3月 Cast Rolling Tip Cavity
Cast Rolling Tip Cavity is a key component that directly feeds the aluminum melt into the high-throughput continuous casting and rolling mill, and its material and structure are very important.
Cast Rolling Tip Cavity structure can be adjusted according to the production situation. In the production of aluminum alloys with high magnesium content, the casting nozzle is prone to blockage, and the casting nozzle can only be stopped to replace the nozzle to continue production. This process not only wastes a lot of manpower and material resources, but also greatly reduces production. effectiveness.
The analysis mechanism of nozzle clogging and the production of nozzles for high-throughput continuous casting and rolling can reduce the time cost of the aluminum plant workshop.
In terms of material analysis, Adtech systematically analyzes the nozzles used in high-throughput continuous casting and rolling from the appearance, microstructure, structure and performance, and analyzes the differences in the nozzle materials and the nozzle Cavity Ear.
In terms of nozzle structure, computer simulation is used to simulate the flow of melt in the nozzle cavity and analyze its laws.
This makes the temperature and speed distribution of the molten aluminum more uniform, improves the surface quality of the cast-rolled billet, reduces the surface dark lines of the aluminum foil produced in the later stage, and improves the quality.
Cast Rolling Tip Cavity consists of two upper and lower plates, side baffles connecting the sides of the two upper and lower plates, and a bottom plate connecting two upper and lower plates and two side baffles. The middle of the bottom plate is provided with a melt inlet, and the melt inlet is opposite. One side is the melt outlet, and a plurality of shunt blocks are arranged between the two upper and lower plates. The melt inlet is directly opposite to the middle shunt block. The central axis of the middle shunt block is the symmetry axis, and the shunt blocks on both sides are about the Symmetrical axis is distributed symmetrically.
Mechanism of Cast Rolling Tip Cavity clogging
1.During the flow of molten aluminum, the temperature gradient of the casting nozzle at the fixed position of the iron plate is higher than that of other areas.
2.The uneven distribution of molten aluminum flow rate leads to uneven temperature distribution, and the temperature of the molten aluminum in the contact area with the casting nozzle wall is low, and slagging is prone to occur.
3. The high-temperature molten aluminum reacts with the SiO2 in the nozzle material to form Al2O3 slag and elemental silicon. The formation of Al2O3 will increase the surface roughness of the nozzle wall, and at the same time, it will enter the molten aluminum to increase its viscosity and change the flow rate. Slow, unable to wash off the slag on the surface of the casting nozzle wall in time, causing the slag inclusion on the casting nozzle wall to increase continuously, and finally causing the casting nozzle to block.
No Comments