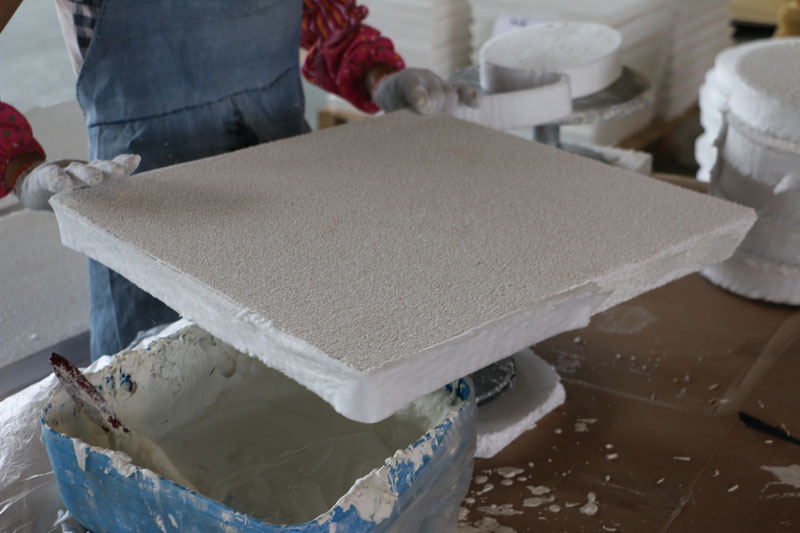
15 4月 Casthouse Ceramic Foam Filter Manufacturers India
Casthouse Ceramic Foam Filter Manufacturers India Hindalco Industries Limited said that, the correct selection and design of ceramic foam filters and filter holders is very important.
Hindalco Industries Limited introduces that a sealing gasket is installed around the ceramic filter plate to act on the contact surface of the filter plate and the filter box to prevent the aluminum liquid from leaking through the contact surface.
Our filter plate has three types of gaskets
1. Expandable gasket seal
2. Fiber cotton seal
3. Fiber paper seal
AdTech Casthouse Ceramic Foam Filter uses organic foam as a carrier, and these organic foams have a three-dimensional network structure.
Put the foam carrier into a special ceramic slurry with thixotropy. Then, the technician uses a special roll extrusion process to evenly coat the ceramic slurry on the carrier.
The final ceramic filter plate after drying and solidification is fired at a high temperature. There is a sealing lining around the Casthouse Ceramic Foam Filter. It is mainly used for the contact surface between the filter plate and the Casthouse to prevent the aluminum liquid from leaking through the contact surface.
The ceramic foam filter makes the aluminum water fill the cavity more evenly.
Molten aluminum has a higher tendency to turbulence during the casting process. The molten aluminum passes through the three-dimensional pore structure of the ceramic foam filter in the aluminum factory and finally transforms into a very stable laminar flow. Laminar flow can better fill the cavity, thereby reducing the impact corrosion of molten metal to the cavity. If you are interested in our products, please feel free to contact us.
Casthouse Ceramic Foam Filter Manufacturers India said(Hindalco) that.
(1) Filter the inclusions in the casting, reduce the gas in the casting, reduce the turbulence when filling the molten metal, reduce the surface defects of the casting, and significantly reduce the rejection rate of the casting.
(2) Improve the compressibility of castings, increase elongation and tensile strength, and improve the surface finish of castings. Improve the fluidity of molten metal, improve the filling ability and shrinking ability of castings.
(3) Reduce processing time and tool damage, and improve the surface quality of castings.
(4) It has extremely high temperature working strength, thermal shock resistance and metal flow impact resistance. There is no slag or cracking during work, which ensures the filtering quality of molten metal.
(5) It can effectively reduce the turbulent flow of molten metal caused by pouring, make filling gentle, and avoid surface defects of castings.
(6) The metal flow is large and the flow is stable. Even in the case of a large amount of inclusions in the molten metal, normal use will not cause blockage of the ceramic foam filter manufacturer.
(7) It has high dimensional accuracy and can be used to automatically place filters on the production line.
No Comments