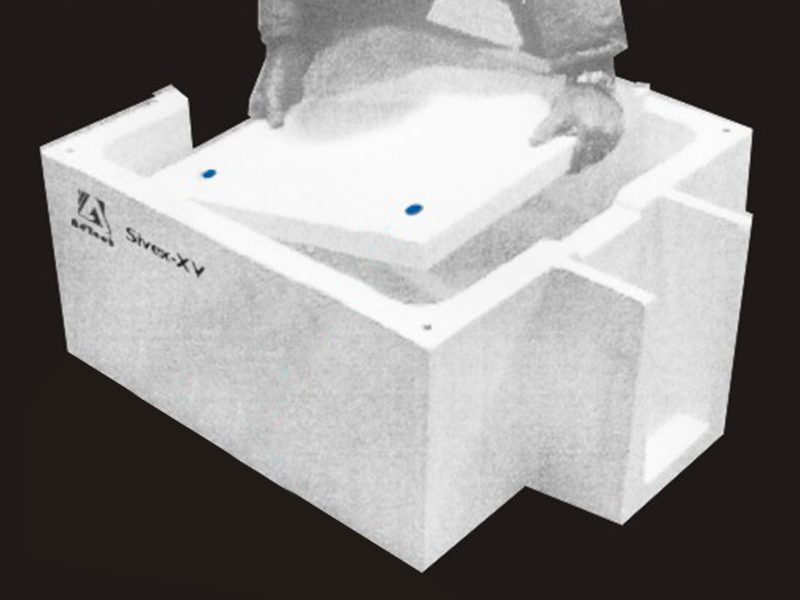
08 6月 Casthouse Filter
Casthouse Filter and two key issues of aluminum casting
Two key issues of aluminum casting
1. The mechanical properties of single-cast test rods cannot fully reflect the quality of the smelting quality. The performance of the single-cast test bar can only represent part of the melting quality and heat treatment quality. The amount of gas in the aluminum liquid, the size of shrinkage and oxidation tendency, and the content of slag inclusions cannot be fully reflected based on the mechanical properties of the single-cast test rod.
2. The influence of several elements on the structure and properties of aluminum alloy.
In actual production, it was found that when the content of Mg element in the aluminum alloy is close to the lower limit of the standard, it may cause the hardness of the casting to decrease, and when it is close to the upper limit of the standard, it may cause the elongation to decrease.
Ti element is the most commonly used refining agent in aluminum alloy, which is beneficial to alloy melting.
Fe element is the main harmful impurity in the alloy, which will reduce the mechanical properties of the alloy. It comes from citrus, smelting tools and charge, and should be strictly controlled.
Mn element can effectively reduce the harmful effect of Fe element on aluminum alloy, but the amount of Mn should not be too much, otherwise it will easily produce coarse and brittle compounds, and may also produce segregation, which affects the performance of castings.
Casthouse Filter used in the melting process and refining process of aluminum scrap.
Ceramic foam filter UAE is used for smelting and recycling of aluminum scrap.
Casthouse Filter is installed in CFF BOX Machine, used to filter aluminum alloy liquid impurities, to meet the high value-added, high technical performance aviation, transportation and other aluminum alloy precision casting production.
There are generally two methods for smelting aluminum scrap
Twice smelting
1. Melt aluminum scraps into ingots (recycled ingots) and stack them according to their chemical composition.
2. When smelting, mix the regenerated ingot into the furnace to smelt the finished product.
Analysis and prevention of defects caused by melting
Pinhole
Causes of aluminum alloy pinhole defects
1. The furnace material and smelting tools are not fully baked.
2. The melting temperature is too high or the melting time is too long.
3. After the deterioration, the aluminum liquid stays too long.
4. Alloy refining is not good.
5. The work site is too humid.
Preventive measures
1. Furnace materials and tools should be thoroughly dried.
2. Control the melting temperature, generally not exceeding 7400C, not exceeding the pouring temperature, but also to prevent local overheating of the alloy during the melting process.
3. The operation is rapid, and the melting time is shortened as much as possible.
4. Refining operation should be careful, refining is the best way to prevent stomata.
5. After the modification, the alloy liquid should be poured in a timely manner for 8-15 minutes; ⑥ Keep the smelting site dry.
Oxidized slag
Causes of defects in oxidized slag inclusion of aluminum alloy
1. The charge is not clean, and the amount of return charge is too much.
2. The slag in the alloy liquid has not been removed.
3. After the deterioration treatment, the rest time is not enough.
Preventive measures
After the charge is blown by sand, the return charge is controlled within 70% of the charge quality.
The degassing and slag removal should be thorough; after the deterioration, ensure sufficient standing time so that the slag has sufficient time to sink or float.
Use Casthouse Filter to remove oxidized slag and other aluminum slag.
Shrinkage and shrinkage defects
Causes of aluminum alloy shrinkage holes and shrinkage defects
1. The alloy grains are coarse.
2. The casting temperature of the alloy is too high.
3. The casting casting system design is unreasonable.
Preventive measures
1. The effect of alloy liquid refining and modification operations has a great influence on this type of defects, so it must be in place.
2. Strictly control the temperature of the aluminum liquid to prevent overheating. Under the condition of ensuring that the casting does not cause insufficient pouring, the pouring temperature should be as low as possible. The pouring temperature generally does not exceed 7300C.
3. Reasonable design of pouring system, so that the molten metal can be filled smoothly;
4. Appropriate adjustment of ingredients and control of appropriate impurity content also have an effect on enhancing the fluidity of the molten metal.
Sorry, the comment form is closed at this time.