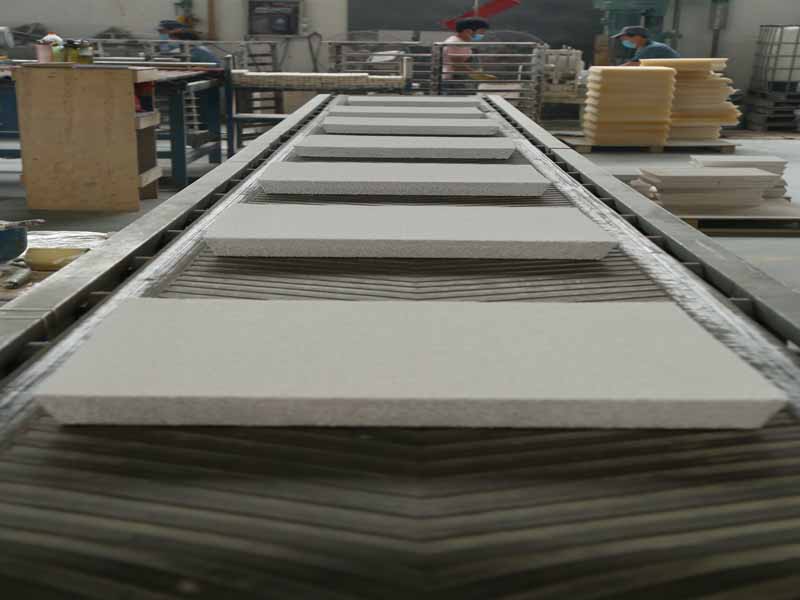
13 4月 Casthouse Filter Foundry
Casthouse Filter Foundry should determine the pore size of the filter according to the quality requirements of the casting and the number of inclusions in the molten aluminum. The size of the filter is determined according to the pouring speed and pouring weight.
After removing the impurities in the cast aluminum filter, the quality of the ingot can be significantly improved and the rate of rejects can be reduced.
The development of cast aluminum filter materials has promoted its wide application in the metallurgical industry.
Cast aluminum filters are usually used to produce a three-dimensional network structure, and organic foam is used as a carrier for interconnected pores.
It is immersed in a special ceramic slurry with thixotropy, and a special roll extrusion process is used to make the ceramic slurry uniform. The ground is coated on the skeleton of the carrier, but the classic method is dry curing and high temperature baking.
Casthouse Filter Foundry’s filtering function
- Removal of impurities and slag: purification of molten metal and degassing at the same time (turbulence adjustment):
- After filtering, the viscosity of the molten metal is reduced, and the fluidity of the aluminum alloy liquid is increased by 10% -15%. 3. The flow of the molten metal before filtration is turbulent, and after filtration is laminar flow (the tortuous flow path of the foam ceramic filter), which reduces the gas volume and the formation of secondary slag.
- As the filtration progresses, the filtration mechanism ranges from sieving, filter cake to deep bed filtration, and the purity of the filtered metal liquid is getting higher and higher (not exceeding the filtration capacity of the ceramic foam filter).
- Reduce the scrap rate of parts
- Improved parts cutting performance
- The mechanical properties of the material are significantly improved, especially the elongation.
No Comments