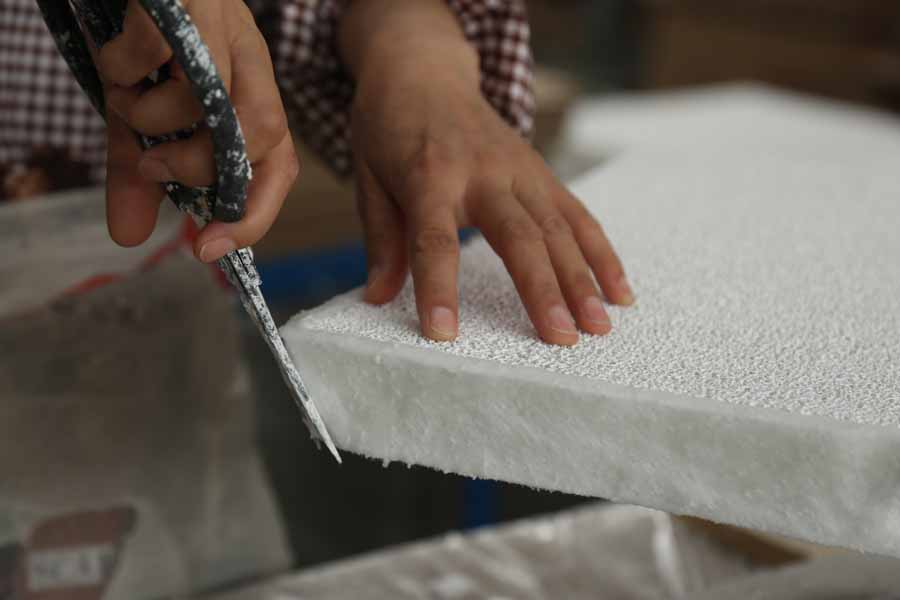
13 4月 Casthouse Metal Foam Filter
Casthouse Metal Foam Filter is an economical method of removing aluminum inclusions in aluminum melting and casting plants.
Due to the different conditions of use, the actual effect usually increases with the decrease of the size of the filter plate hole and the flow rate of the molten aluminum.
The Metal Foam Filter has been specially treated and is not easily broken. The ceramic filter has high strength, excellent aluminum water erosion performance and good thermal performance. It is an ideal choice for the production of various castings.
The manufacturing process of Metal Foam Filter is usually to squeeze out excess and dry polyurethane sponge in ceramic slurry, and finally fire and knot at high temperature to form a three-dimensional porous ceramic material with related original bubble structure.
Considering the filtration efficiency and strength, the prepared ceramic foam filter is no longer a three-dimensional network structure. Rather, they are interconnected, twisted, and unevenly thick pipes. This uneven wall surface plays a key role in the capture of small inclusions in the aluminum melt, which is the deep filtration. This is the fundamental difference between the screen mesh and the ceramic foam filter for cast plates. This three-dimensional network structure increases the flow path of the aluminum liquid, makes the aluminum liquid contact the filter plate, and increases the adsorption capacity of the inclusion particles.
In the initial stage, surface screening intercepts large particles, while small particles are removed by a deep filtration mechanism. With the formation of surface deposits, the deposits can retain large and small particles. Small inclusion particles can be captured by a deep filtration mechanism. At this time, the filtering effect of the ceramic foam filter will be better.
When the particle adsorption is saturated, that is, the number of particles adsorbed from the melt is equal to that when the particles are carried away by the melt flow, the slag removal ability is reduced.
Filter mechanism of Casthouse Metal Foam Filter
The main purpose of the ceramic foam filter for casting is to remove the inclusions in the aluminum melt. Inclusions in the melt usually exist in three forms: metal oxides, pulverization of refractory materials, and other foreign particles, that is, particles introduced during the smelting process.
There are three ways to remove suspended particles in the melt:
Sedimentation-the accumulation of particles at the bottom of the melt.
Floating-mixed floats gather on the surface of the melt.
Filtration-the separation of particles from the melt through porous media.
Natural sedimentation generally occurs when the particles are dense and coarse, and particles smaller than 90um are not very effective for static sedimentation.
Choose a molten aluminum ceramic foam filter
In addition to the geometric size, strength, chemical stability and thermal stability of the ceramic foam filter for casting, its filtering effect depends to a large extent on its internal structure.
At present, PPI (poreper inch) represents the pore size of the ceramic foam filter plate. The 40 PPI foam ceramic filter plate filter can remove 5 micron inclusions. Whether the particles can be removed depends on the probability of collision, and also on the ability of the filter to adsorb particles.
When selecting the pore size of the filter plate, priority should be given to product quality requirements. For civil profiles, such as cast rods and cast plates, please select 10-40ppi filter plates according to product category and melt cleanliness. High-grade aluminum foil, tin can plates and space materials require 30-80 PPI filter plates. The actual selection of the filter plate depends on the user’s practice and experience, combined with its use conditions. Finally, whether the cleanliness of the product meets the quality requirements is used as a measure.
No Comments