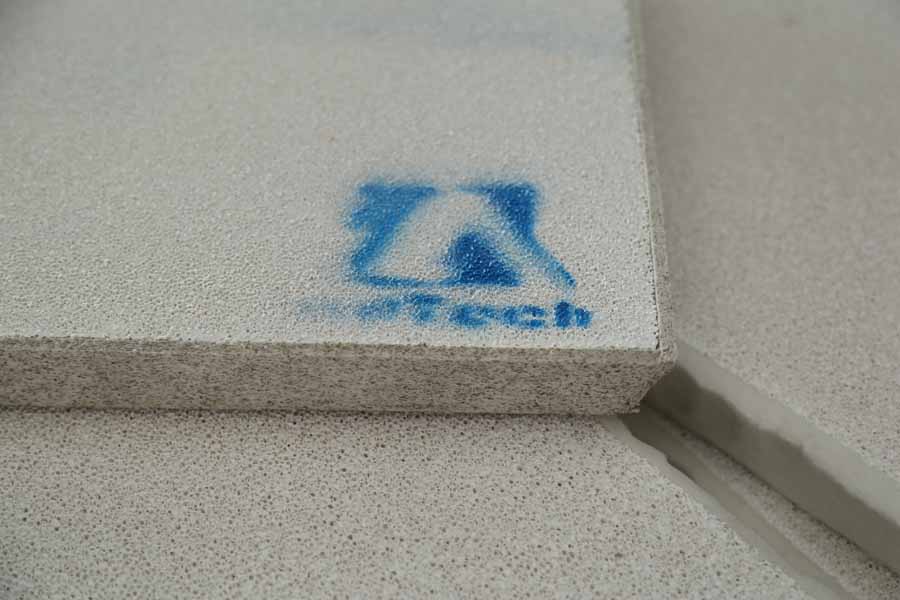
12 4月 Casthouse Porous Filter Material
Casthouse Porous Filter Material plays an important role in the production of aluminum alloy casting industry. It can improve the surface quality, product performance and microstructure of aluminum, and increase the yield of aluminum.
Gently put the ceramic foam filter plate into the filter box. Then press the gasket around the filter plate by hand. Prevent lateral flow of molten aluminum. Preheat the filter box and filter plate evenly. In order to make the temperature close to the temperature of molten aluminum. Preheating can remove moisture and facilitate rapid filtration. The preheating method can be electric heating or gas heating. Usually, the preheating time is 15-30 minutes.
Since the molten aluminum filter was first used in 1978, molten metal filtration technology has developed rapidly.
The ceramic filter uses polyurethane foam as a carrier and is immersed in a suspending agent composed of ceramic powder, binder, sintering agent and paint to squeeze out the excess paint. The paint is evenly coated on the carrier skeleton to form a green body, and then the green body is dried and baked at a high temperature.
Molten metal filters are divided into bonding type and sintering type. The former relies on a binder to bind ceramic particles together. The latter relies on high temperature insulation to sinter and fuse relatively pure micron ceramic particles.
The ceramic foam filter has a unique three-dimensional interconnected curved pore network skeleton structure, its open porosity can reach 80%-90%, and has the following three filtration and purification mechanisms: one is mechanical interception, the other is distillation scum, and the third is Deep adsorption. Through these three filtering and purification mechanisms, the large inclusions of liquid metal and a large number of small floating objects can be effectively filtered out to tens of microns, thereby reducing the rate of casting rejects and welding repair rates.
In addition, it can also simplify the pouring system and improve the metallographic structure, thereby increasing the output and productivity of the casting process, and improving the quality and performance of the castings. Therefore, the foam ceramic filter has a good application prospect.
Casthouse Porous Filter Material has the advantages of large filtration area, good thermal shock stability, high chemical stability, good metal erosion resistance and good filtration efficiency.
Therefore, as a new type of high-efficiency filter in the metal melt filtration and purification technology, people’s attention has been paid.
At present, its application range has been extended to precision casting, cast steel industry and foundry industry. Foam ceramic filters can improve the mechanical properties of castings, reduce the rate of casting rejects, increase the rate of finished castings, and extend the service life of metal cutting tools.
Due to the closed cells in the ceramic foam, its thermal efficiency is reduced and the heat transfer in the convection process is reduced, so that the ceramic foam has the characteristics of low thermal conductivity and good thermal shock resistance. It is an ideal heat-resistant material.
Casthouse Porous Filter Material should have the following characteristics
It has sufficient mechanical strength at normal temperature and high temperature, so that it can withstand the impact of transportation vibration, extrusion and high-temperature molten metal during use.
It has suitable refractoriness and low thermal expansion coefficient, so that it will not soften and deform under the long-term action of high-temperature molten metal.
It has excellent high temperature chemical stability, so that it will not be corroded by high temperature molten metal and avoid metal pollution.
No Comments