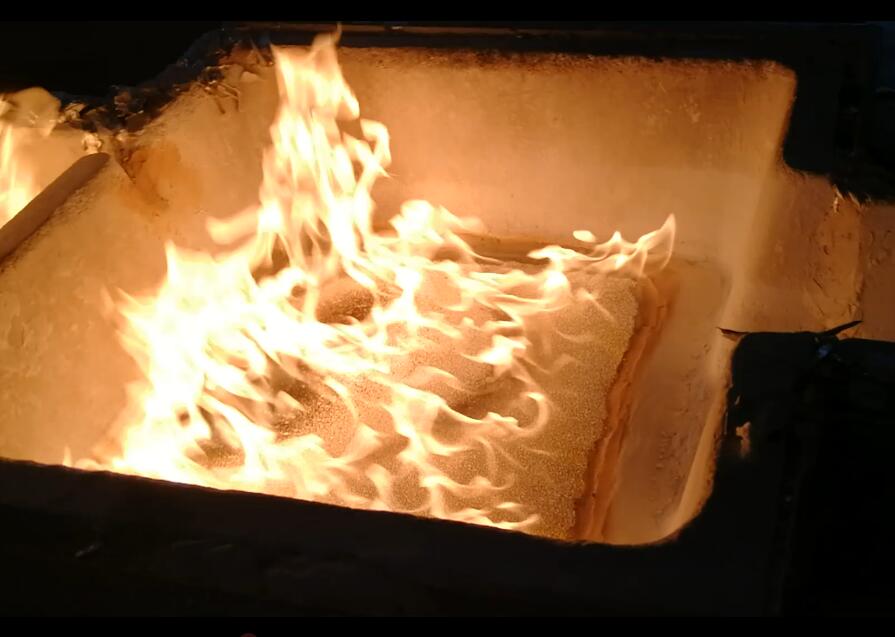
24 7月 Casting Filters
Casting Filters can effectively remove various inclusions in the aluminum water with a fineness of micrometers.
Make the aluminum water into a smooth laminar flow, which is conducive to flushing, good mechanical strength and chemical stability, and superior aluminum water erosion resistance.
Strictly controlled hole size and through hole rate can obtain stable filtration effect.
There is a sealing ceramic fiber liner around the foam ceramic filter plate, which helps to seal the filter in the filter box and ensures that there is no side flow of molten metal.
Casting Filters are mainly used in the purification process of aluminum and aluminum alloy production. They are also used as various gas-solid, liquid-solid separation media, catalyst carriers, burners, sound absorption and environmental protection.
Product Advantages
1. High dimensional accuracy, high mechanical strength, stable chemical composition
2. Anti-corrosion of liquid aluminum and its alloys, phosphorus-free, environmentally friendly purification of aluminum liquid, improve the quality of aluminum materials, reduce defects, reduce the rate of defective products, reduce costs, and increase production efficiency.
3.Easy to use, flexible size from 40mm to 600mm to meet different aluminum water flow rates.
Adtech’s alumina ceramic foam Casting Filters are surrounded by a sealing land Casting Filter gasket, which helps to seal the filter in the filter box and ensures that there is no side flow of molten metal.
When using a ceramic foam filter, the pore size of the filter should be determined according to the quality requirements of the casting and the number of inclusions in the molten metal.
The size of the filter is determined according to the pouring speed and pouring weight.
In order to ensure the filtering effect of the filter, the placement of the filter, the design of the gating system should also follow certain specifications.
The filter must be placed as close as possible to the casting to obtain the maximum filtration efficiency and flow adjustment.
Considering practical factors, such as the position that can be placed in the mold and the design of the gating system, the filter is often placed in the runner.
Sometimes the filter is placed at the bottom of the sprue, but this is not recommended.
Because the filtering effect and the flow of the ceramic foam filter will be affected by the turbulence from the bottom of the sprue to the runner.
Sorry, the comment form is closed at this time.