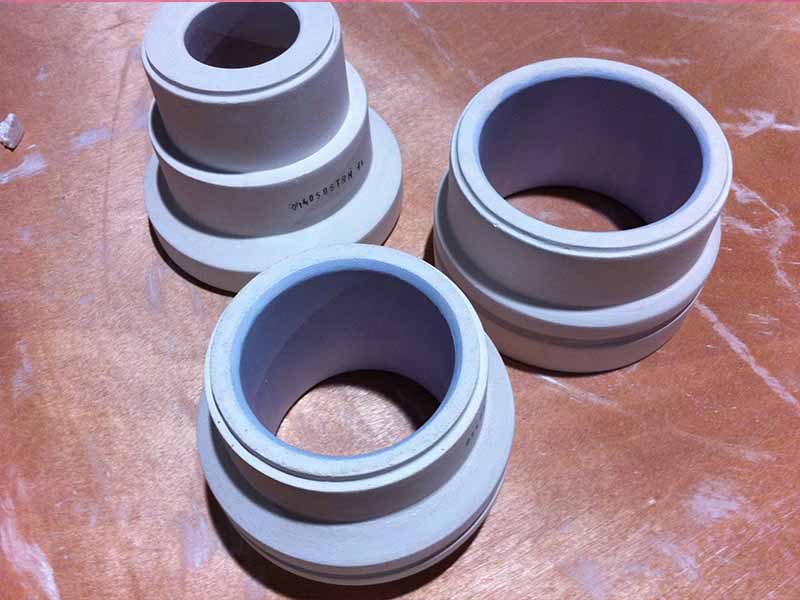
02 11月 Casting Thimble
Casting Thimble is made of two materials: high silicon melting 140 and Al-Si. It has strong corrosion resistance, high geometric accuracy, smooth casting surface, long life, low maintenance cost, and no pollution to molten metal. It is the best choice for hot top casting , To meet the technical needs for the production of aluminum alloy precision casting products such as aviation, transportation, and electronic products that require high added value and high technical performance.
AdTech is a manufacturer specializing in the development of new materials and the production of Casting Thimble and draft tubes for hot top casting.
Since 2012, the company has developed and produced hot top casting products: casing, adapter plate, diverter plate, hot top cap, graphite ring, diverter groove and other products are used in molten metal casting equipment, especially with wagstaff gas sliding casting table It is used for precision casting. During casting, the aluminum liquid of the distribution plate is connected to the mold crystallizer to form, and it has been recognized by more than 98% of the existing customers.
Hot top casting refers to a casting form in which there is an area with good heat preservation performance on the top of the mold. The fundamental purpose of hot top casting is to slow down the primary cooling of the upper part of the mold, not to slow down the primary cooling of the entire mold.
Aluminum casting generally adopts vertical or horizontal water-cooled semi-continuous casting method.
In order to improve the structure and surface quality of the billet in vertical casting, electromagnetic crystallization tanks, short crystallization tanks and hot top casting methods (see solidification of metals) have also been developed.
The water-cooled semi-continuous casting method is to introduce liquid metal into a water-cooled crystallizer through a launder, so that the liquid metal is cooled to form a solidified shell, which is pulled by the base of the casting machine or dropped out of the crystallizer by its own weight to form an ingot.
The process parameters vary greatly due to the alloy composition and billet size.
Generally, the casting speed and cooling rate should be increased as much as possible, and the height of the crystallization tank should be reduced. The casting temperature is usually 50 to 110°C higher than the liquidus line of the alloy. In addition, the continuous casting and rolling process of aluminum strip has been developed.
Cast aluminum alloys have the same alloy system as wrought aluminum alloys, and have the same strengthening mechanism as wrought aluminum alloys (except for strain strengthening). The main difference is that the maximum content of alloying element silicon in cast aluminum alloys exceeds that of most wrought aluminums. The silicon content in the alloy.
In addition to the strengthening elements, the cast aluminum alloy must also contain a sufficient amount of eutectic elements (usually silicon), so that the alloy has considerable fluidity and is easy to fill the shrinkage joints of the casting during casting. At present, the basic alloys only have the following 6 categories
AI-Cu alloy
AI-Cu-Si alloy
AI-Si alloy
AI-Mg alloy
AI-Zn-Mg alloy
AI-Sn alloy.
Casting properties usually include fluidity, shrinkage, porosity, component segregation, gas absorption, casting stress and cold cracking tendency, etc.
Sorry, the comment form is closed at this time.