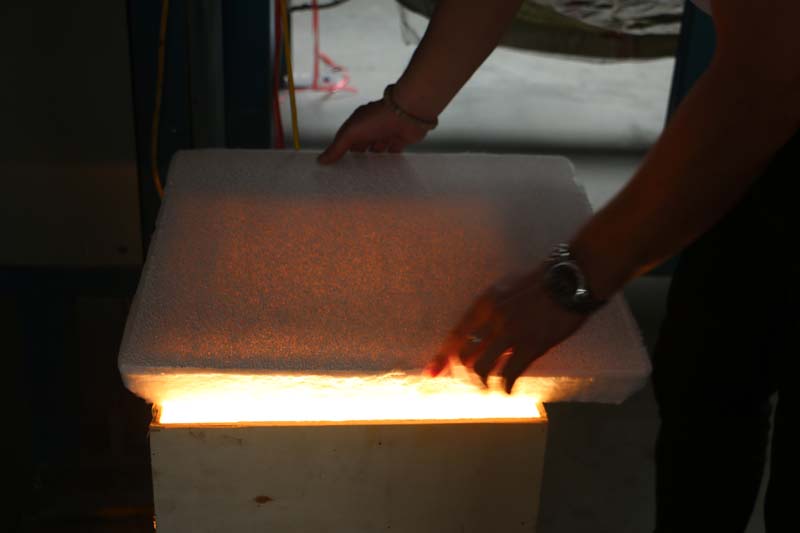
31 3月 Ceramic Filter 20 Inches
Ceramic Filter 20 Inches is used to filter molten aluminum before casting. The filtration process removes particles that may cause waste in the final product.
Use square foam ceramic filter plate aluminum liquid, use alumina refractory slurry as raw material, impregnated with mesh foam with specific porosity. Then, the soaked foam is dried and fired in a kiln. After the foam burns, the porous ceramic body is left as a filter.
Ceramic foam filter Dimension
660x660x50(26 inch)
584x584x50(23 inch)
508x508x50(20 inch)
432x432x50(17 inch)
381x381x50(15 inch)
305x305x50(12 inch)
228x228x50(9 inch)
178x178x50(7 inch)
When using a ceramic foam filter, install the Ceramic Foam Filters For Casting in the filters casthouse.
Pour the molten aluminum into the filter box through a ceramic foam filter. The filter traps the fine particles in the molten metal.
After the casting operation is completed, the aluminum slag remaining in the ceramic filter forms an almost solid piece of aluminum.
Ceramic Filter 20 Inches is the most commonly used ceramic foam filter in the aluminum casting industry.
Ordinary aluminum casting usually uses 10-40ppi ceramic filter plates.
Aviation and high-quality aluminum materials usually use 30-60ppi ceramic filter plates.
Ceramic foam filters can remove large amounts of such inclusions from molten aluminum. Foam ceramic filtration technology has become the main method of filtering commercial aluminum alloys worldwide.
Because of its low installation and operating costs and ease of use, the technology quickly expanded to aluminum foundries of various types and levels of complexity.
Over the years, it has been steadily developing towards the use of finer pore ceramic foam filters to provide higher melt cleanliness, which is a requirement for the continuous improvement of the quality of aluminum processed products.
For example, in the application of aluminum can body panels, 40 and 50 holes per inch (PPI) foam filters are now commonly used in panel production.
In addition, a finer pore filter is currently being evaluated.
However, the use of finer pore filters requires a lot of pretreatment to reduce the level of inclusions and prevent the filter from clogging prematurely or blocked by residual inclusions.
Solid particles such as oxides, carbides, nitrides, and borax compounds present in metals (such as aluminum) and insoluble inclusions in liquids (such as molten salts) will significantly affect the plasticity and the final metal during rolling or extrusion deformation. Surface Quality.
No Comments