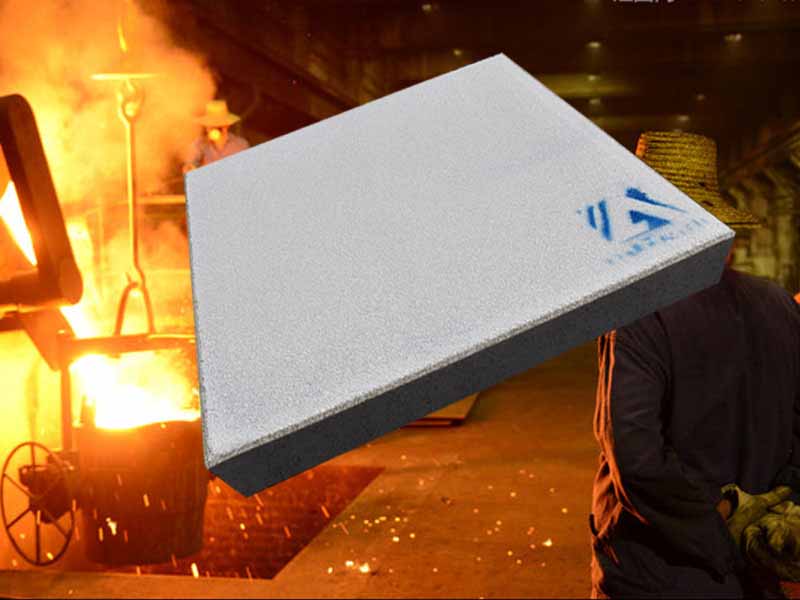
12 11月 Ceramic Filter Aluminium Myanmar
Ceramic Filter Aluminium Myanmar uses polyurethane foam as a carrier and immerses it in a coating made of ceramic powder, binders, sintering aids, suspending agents, etc., and then extrudes the excess coating to make the ceramic coating evenly coated. On the carrier. The skeleton becomes a green body, and the green body is dried and fired at a high temperature.
Ceramic Filter can effectively remove large inclusions in molten aluminum, absorb micron-sized particles of small inclusions, improve surface quality, improve product performance, improve microstructure, and increase yield. It is widely used in the production of aluminum profiles, aluminum foils, and aluminum alloys.
Characterization of ceramic foam filter
Ceramic Foam Filter characterizes a specific reaction structure in terms of pore size, pore distribution, pore shape and porosity.
Manufacturing process of cast aluminum foam ceramic filter
The ceramic foam filter for cast aluminum takes the three-dimensional network structure and the organic foam sponge connected with the pores as the carrier, which is impacted into a special ceramic slurry with thixotropy, and the ceramic slurry is uniformly applied by a special rolling extrusion process Ground is fixed on the carrier frame.
Then, it is dried and cured, and then baked at a high temperature.
Cast ceramic foam filter for aluminum alloy Since the first research in 1978, foam ceramic filter technology has developed rapidly.
Ceramic Filter Aluminium Myanmar is placed in the casthouse and is a very important filter element in the aluminum rod casting process.
The rotary degasser uses a rotor that rotates at a high speed and sprays inert gas to break up large inert gas bubbles into very fine small bubbles, and make them evenly dispersed in the molten metal. By reducing the bubble diameter, the total surface area of these bubbles increases sharply, which allows more inert bubble surfaces to contact the hydrogen and impurities in the molten metal to bring these harmful substances to the surface of the liquid.
The key to the degassing of the rotary degasser is that the rotor can break the large bubbles of inert gas that enters into very small bubbles, and make them diffuse in the entire molten metal. By reducing the bubble diameter, the surface area of the inert gas is increased sharply, so that more inert gas surfaces are in contact with the hydrogen and impurities in the molten metal, and the hydrogen or impurities are removed from the molten aluminum as the bubbles rise.
The flow control of the inert gas entering the molten aluminum can be adjusted according to the volume of the metal liquid to be processed. The speed of the rotating rod and the rotor can be adjusted to generate bubbles of appropriate size to facilitate the diffusion of the inert gas.
Both argon and nitrogen can be used as inert gases to degas molten aluminum. The purity of the inert gas must be above 99.99%.
Degassing is to spray inert gas into molten aluminum to achieve the purpose of removing hydrogen. In addition, degassing is also considered to be a very effective way to float impurities. Two main theoretical models have been proposed to explain the principle of degassing. The macro model assumes that the removal of each impurity is similar in nature. The microscopic model, that is, according to this theory, due to the higher vapor pressure of hydrogen, the dissolved hydrogen diffuses into the injected aluminum liquid gas. Theoretically speaking, after an inclusion with a diameter of 10 microns is in contact with a bubble, it is adsorbed on the bubble and floats to the surface of the liquid.
No Comments