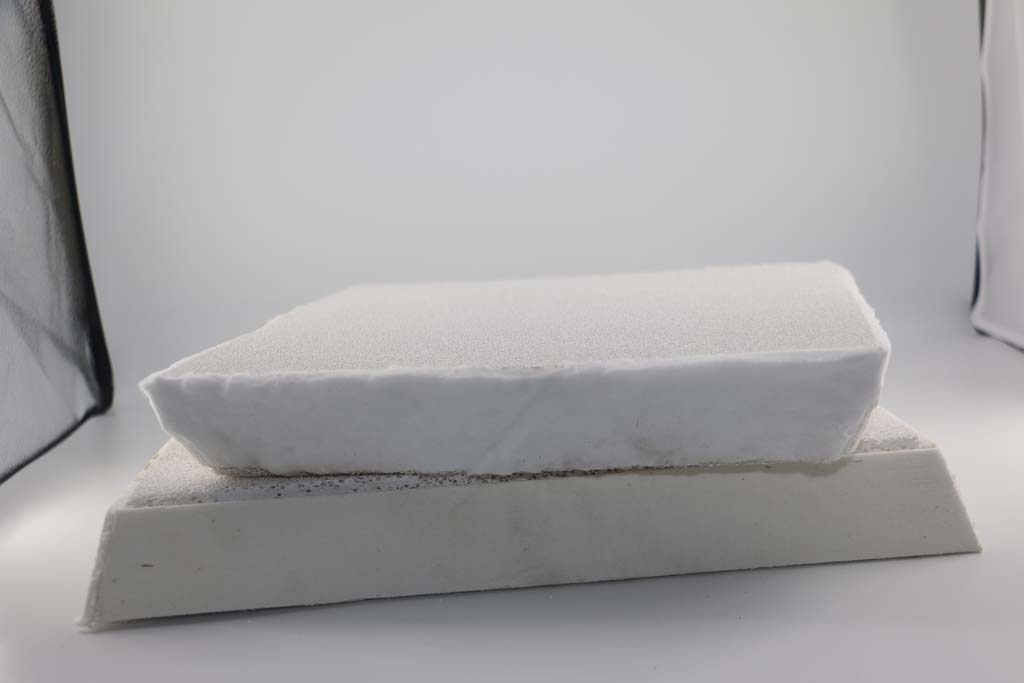
26 2月 Ceramic Filter Ceramic Product
Ceramic Filter Ceramic Product can effectively remove or reduce the inclusions in the molten metal, improve the purity of the molten metal, and make the surface of the molten metal castings smooth, uniform in structure, increased in strength, and reduced in rejects, while further reducing machining Loss and increase labor productivity.
Ceramic Filter Ceramic Product is suitable for casting aluminum rods, aluminum ingots, aluminum plates, and other aluminum alloys.
Therefore, the products are widely used in automobiles, shipbuilding, locomotives, agricultural machinery, construction machinery, aviation, aerospace, machine tools, electrical appliances, engineering pipelines, valves, pipe fittings, etc.
Since the ceramic foam filter is used in the casting process to filter the metal oxide and other solid slag contained in the molten metal, thereby improving the quality and yield of aluminum alloy, the use of ceramic foam filter promotes the technological progress of the casting industry. Ceramic Foam Filter Suppliers sales@adtechamm.com
Ceramic Filter Ceramic Product
A ceramic filter having two end faces and an outer peripheral surface and separated by a partition wall is formed with a plurality of porous bodies from one said end face to the other said end face of the main flow path of the purified fluid.
And a filter membrane arranged on the inner wall surface of the main flow channel, by allowing the purified fluid flowing into the main flow channel from the opening on the one end surface side to pass through the filter membrane and the porous body The inside is purified, and as a purification fluid is taken out from the outer peripheral surface of the porous body.
Purification is performed by allowing the fluid to be purified flowing in from the outer peripheral surface of the porous body to pass through the interior of the porous body and the filter membrane, and as a purified fluid from at least the main flow path The opening on the one end surface side is taken out.
Continuous casting can be divided into mixed furnace casting and external casting.
All use continuous casting machines. Mixing furnace casting is the process of casting molten aluminum into the mixing furnace, and is mainly used to produce aluminum ingots for remelting and casting alloys.
Outer casting is directly cast from the ladle to the casting machine, which is mainly used when the casting equipment cannot meet the production requirements, or the quality of the incoming materials is too poor to be directly into the furnace.
Since there is no external heating source, the ladle is required to have a certain temperature, generally 690-740°C in summer and 700-760°C in winter to ensure that the aluminum ingots have a better appearance.
No Comments