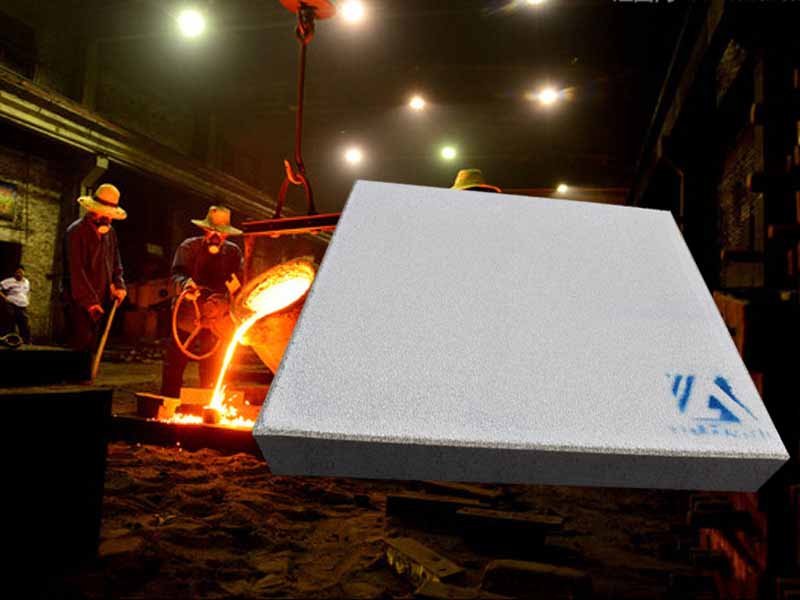
24 11月 Ceramic Filter Delemar Aluminum
Ceramic Filter Delemar Aluminum effectively removes various impurities in molten aluminum and greatly improves the cleanliness of molten aluminum, which is beneficial to improve the product quality of aluminum ingot factories and reduce costs.
The foam aluminum ceramic liquid filtration and purification process and device are suitable for all aspects of aluminum production, including thin plates, strips, foils, bars, pipes, wires, extrusions, forgings, primary aluminum ingots, secondary aluminum ingots, and continuous cast aluminum . Daga et al.
The quality of aluminum smelting is very important, it greatly affects the performance of the post-processing and the quality of the final product. Therefore, countries all over the world attach great importance to the purification of molten aluminum.
There are many reasons for aluminum pollution. On the one hand, during the refining process, aluminum is exposed to the atmosphere in the furnace in a molten or semi-molten state. Such as lining fragments, chlorides and carbides in flux, coarse particles of intermetallic compounds, etc.
On the other hand, part of the waste that constitutes the charge brings some non-aluminum impurities into the circulation process. Because the waste generated in each process in the factory comes from process waste, engineering waste and off-site waste, the paths are different, the installation is complicated, and the quality is poor.
The above-mentioned impurities often produce bubble impurities in the cast plate, which seriously affects the purity of the molten metal, and further affects the processing performance, mechanical properties, wear resistance and appearance of the product. At present, there are many ways to remove these harmful substances to purify molten aluminum.
According to the different methods, these methods can be divided into kiln processing and continuous out-of-furnace processing (that is, online processing). According to the function, it can be divided into two types: degassing or deslagging.
Delemar Aluminum purchased the Ceramic Filter Delemar Aluminum through sales@adtechamm.com for the filtration of molten aluminum in the foundry.
Delemar Aluminum engineer said that the continuous casting and rolling method is the crystallization of liquid aluminum in a double-belt caster.
The continuous casting machine has a high cooling rate, which is easy to obtain a smaller grain size, the crystal structure of the billet is dense and fine, the dendrite spacing is small, and the solid solubility of alloy elements is large, which improves the product performance to a certain extent.
Compared with the casting-rolling method to produce aluminum alloy strips, the continuous casting and rolling method can meet the production of alloy varieties with a wider crystallization range.
In terms of production cost, energy saving and consumption reduction, both the casting-rolling method and the continuous casting-rolling method have advantages over the traditional ingot-rolling method.
However, the export thickness of the cast-rolling method is much thicker than that of the continuous casting and rolling method, and the subsequent cold rolling passes need to be increased; and the cast-rolled slab is mostly in the as-cast structure, which is not good for the subsequent processing.
The continuous casting and rolling method is the same as the casting and rolling method, eliminating the energy consumption of aluminum ingot cutting, milling and aluminum ingot preheating of the traditional aluminum ingot rolling method, and the lower limit of the thickness of the hot strip of continuous casting and rolling is only 1mm, which is much thinner than the traditional aluminum ingot rolling method, which can save most of the cold rolling passes.
In the continuous casting and rolling method, hot top accessories such as flow control box, float, flow trough, casting nozzle plate, etc. can well control the flow of molten aluminum.
No Comments