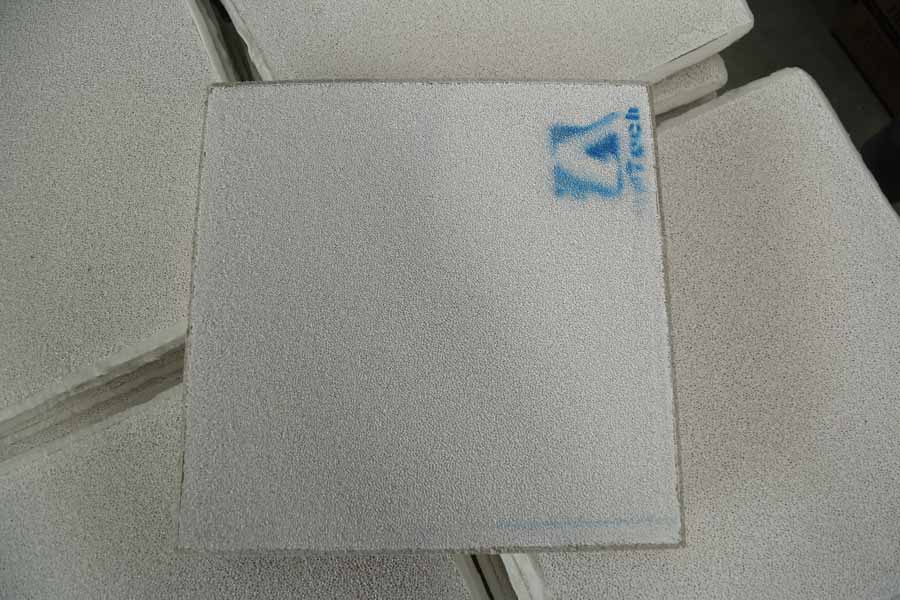
29 4月 Ceramic Filter Foam
Ceramic Filter Foam
Ceramic Filter Foam have three types
Silicon Carbide(SiC) Foam Ceramic Filter for Iron casting.
Zirconia Foam Ceramic Filter for Steel Casting.
Alumina Foam Ceramic Filter apply to improve quality of aluminimu alloy casting and other non-ferrous alloy casting.
Shape in square, round, cylinder.Special size is available upon request.
Adtech Ceramic Filter Foam with its characteristics of light-weight, high mechanical strength, large specific surface areas, high porosity, excellent thermal shock resistance, erode resistance, high-performance, competitively priced, is designed for filtering impurities from liquid metals. With the distributing pores net structure, they are able to increase the surface areas, and absorb the sinter, the liquid metal becomes more pure, waster quality problems such as sand pore and air pore are much less. And the cast quality becomes much better.
Ceramic Filter Foam Advantages
A complete filter box system
Supplied to the exact requirements of the customer
Available with or without a heating system
Variable operating height for ease of use and connection to existing launder system
“Tile-saving technology” is popular within casthouse application. With this kind of design, usually, one tile can be used up to six casts.
Here we introduce the use of Ceramic Filter Foam
1. Inspect and clean debris on the surface of the filter box to keep the filter box clean and free from damage;
2. Put the filter plate into the filter box gently and press the sealing gasket around the filter plate to prevent the aluminum liquid from flowing or floating.
3. Evenly preheat the filter box and filter plate so that they are close to the temperature of the aluminum liquid. The preheating temperature of the filter plate is not lower than 460°C. The expanded cotton is automatically sealed by the thermal expansion. The filter plate is not easy to float and is preheated to remove the adsorbed water. Parts, more conducive to help open the initial filter aperture opening, to prevent the thermal expansion and contraction to bring some plug to the filter plate. Preheating can be electric or gas heating, normal heating 15-30 minutes;
4. Pay attention to observe the change of the aluminum hydraulic head when casting, and maintain the flow of normal demand aluminum liquid. The normal initial pressure head is 100-150mm. When the aluminum liquid starts to pass
The indenter will fall below 75-100mm, and then the indenter will slowly increase;
5. During the normal filtration process, avoid knocking and vibrating the filter plate. At the same time, the flow tank should be filled with aluminum water to avoid the perturbation of the aluminum liquid;
6. After the filtration is completed, remove the filter plate in time and clean the filter box.
Sorry, the comment form is closed at this time.