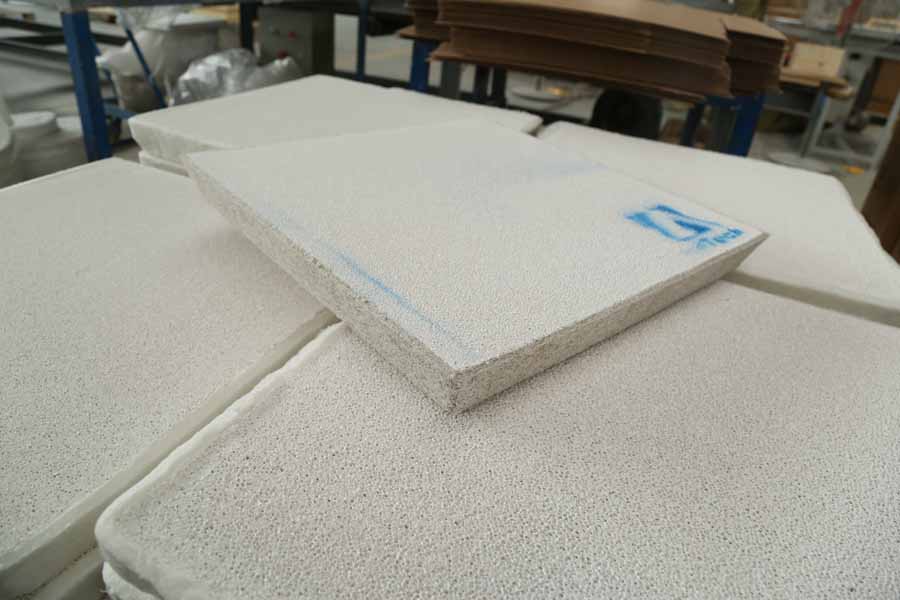
15 5月 Ceramic Filter For Foundry Australia
Ceramic Filter For Foundry Australia can effectively remove large inclusions in the aluminum liquid and adsorb small micron-level inclusion particles, which has a certain effect on improving the surface quality, product performance, microstructure and yield of the aluminum liquid.
Zirconia ceramic filter plate is a kind of ceramic filter plate, which is indispensable for aluminum profile, aluminum foil and aluminum alloy melting casting process.
The zirconia-based ceramic slurry is evenly coated on the skeleton of the three-dimensional network structure, and the organic foam cotton connected to the pores is used as a carrier, then dried and solidified, and then baked at high temperature.
Using zirconia powder as the main raw material, alumina powder and yttria powder as sintering aids, a high-performance zirconia foam ceramic filter plate was prepared by the organic foam impregnation method.
The effects of firing temperature and holding time on the sample bulk density, thermal shock resistance and compressive strength were studied. The performance of the samples was characterized by universal testing machine, comprehensive thermal analyzer, X-ray diffractometer and scanning electron microscope.
The experimental results show that when the firing temperature is 1580 ℃ and the holding time is 120min, the prepared zirconia foam ceramic filter plate has the best performance.
Ceramic Filter For Foundry Australia can be used in Pacific Aluminium, Pacific Aluminium Nzas, Pacific Aluminium Rio Tinto, Pacific Aluminium Nz, Pacific Aluminium Samoa, Pacific Aluminium Group, Pacific Aluminium Australia, Pacific Aluminium Brisbane, Pacific Aluminium Tasmania, Pacific Aluminum, Pacific Aluminum Company, Aluminum Pacific, Pacific Coast Aluminum Products, Aluminium Pacific, Fletcher Aluminium Pacific Suite, Pacific Aluminium Bell Bay, New Zealand Aluminium, New Zealand Aluminum…
Ceramic Filter For Foundry Australia Product Features
1. Effectively filter metal particles and impurities, such as slag and refractory fragments to the micron level, to reduce the loss of cutting tools during the casting process.
2. Stable filling of liquid metal and uniform casting structure, thus improving the mechanical properties of casting surface hardness, tensile strength, fatigue resistance and other properties.
3. The three-dimensional grid structure has a good correction effect on metal turbulence, and has a good control effect on non-metallic inclusions and secondary oxidation caused by turbulent erosion of the cavity.
4. Simplify the pouring system and improve the cavity utilization.
5. The surface of the casting is clean, which reduces the processing margin, shortens the cleaning time, and improves the transportation efficiency.
Sorry, the comment form is closed at this time.