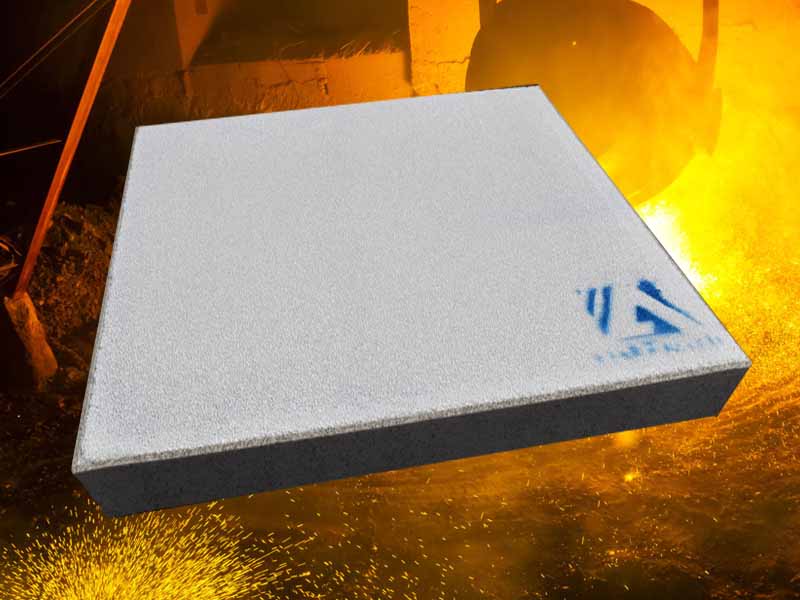
24 12月 Ceramic Filter Indonesia Aluminum Company
Ceramic Filter Indonesia Aluminum Company can effectively control the oxidized inclusions in the melt to improve the quality of cast rods and rolled plates has become a common goal pursued by the metallurgical, casting and material industries of all countries. At present, filtration and purification methods are widely used to remove inclusions in aluminum alloy melts.
China is a major producer of aluminum products, and the output of aluminum products has always been the world’s largest, but mainly low-end products.
With the continuous expansion of market demand, aluminum products must move towards high-end. The use of foam ceramic filter plates can improve the quality of aluminum products, improve product grades, and make them meet the requirements of the high-end market. Therefore, the demand for filter plates
The development of Ceramic Filter Indonesia Aluminum Company began in the 1970s and is a porous material with high temperature characteristics.
Its pore size ranges from nanometers to micrometers. It has a high porosity porous ceramic body with a three-dimensional space grid structure. The porosity is between 20% and 95%. Its shape is like tempered foam or porcelain. Sponge body, the use temperature is from room temperature to 1600℃.
Since the United States invented the use of ceramic slurries such as alumina and kaolin in 1978 to successfully develop foam ceramics for aluminum alloy casting and filtration, countries such as Britain, Japan, Germany, and Switzerland have competed in research.
The production process is becoming more and more advanced, and the technical equipment is becoming more and more mechanized and automated. According to different application purposes, a variety of materials have been developed for foam ceramic filters for different purposes.
Such as A1203, ZrO2, Sic, silicon nitride, boride and other high-temperature foam ceramics, and some also add certain minerals, such as mullite, Dong Qingshi, fly ash, coal ash, etc., and the products have been serialized and standardized , Forming a new industry.
Foam ceramic filtration is the last process of aluminum melt purification treatment.
It needs to be specially pointed out that to prevent the secondary pollution of the melt that may occur in the process of the aluminum melt after leaving the filter box to solidification and forming.
In this process, use long-life, high-strength, non-stick aluminum, and good thermal insulation fused silica ceramic sintering trough, front box, distribution plate, and hot cap, and timely dehumidification and cleaning to eliminate possible pollution sources .
It cannot be ignored to ensure the cleanliness of the aluminum melt.
No Comments