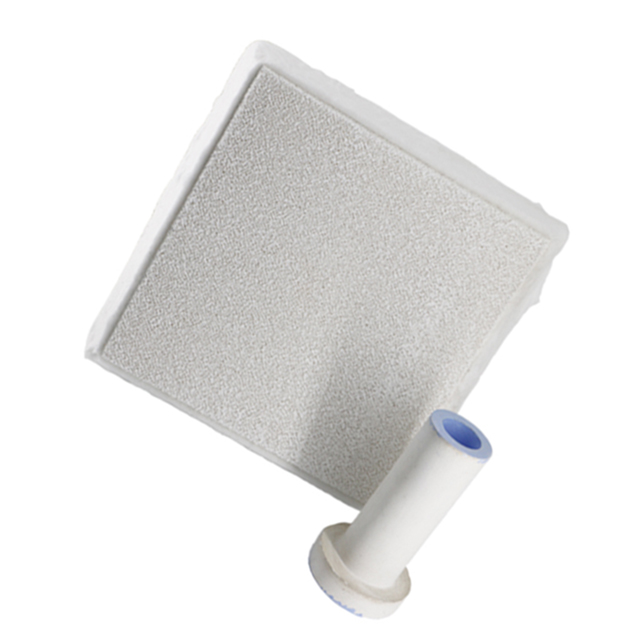
24 6月 Ceramic Foam Filter For Metal Filtration
Ceramic Foam Filter For Metal Filtration
When we choose any project, I believe everyone wants to choose a cost-effective one. In other words, choose high-quality products with good performance, good quality and long life. Then we are no exception when choosing ceramic filter plates. Here, we hope to be able to choose an efficient ceramic filter plate. So how do we choose ceramic filter plates to ensure high efficiency? The editor summed up a few notes when selecting, let us take a look.
1. There are many impurities and the quality of castings is average. Ceramic filter plates with large mesh openings can be used. Add glass fiber cloth coarse filter in front of the filter plate. At this time, it is important to filter the semi-continuous casting with glass fiber cloth first. When opening the hole, it can trap the slag and the slag washed down by the flow groove to prevent the filter plate from clogging.
2. High quality requirements for casting products, using new small-net large-net foam ceramic filters.
3. The choice of ceramic filter plate specifications depends on the melt flow rate and total flow.
4. Pure color, no noise, indicating that the material is uniform; sticking hands without sticking hands means that there is no glue on the surface, which will not cause secondary pollution.
5. When purchasing filter materials, the effective specific surface area or porosity of the foam should be carefully evaluated. Observe the uniform state of the mesh on the surface of the filter plate, and then observe the uniform state of the mesh on the cross section of the filter plate. If possible, the porosity can be calculated using the drainage method. The three-dimensional grid is uniform and the porosity is large. It is an excellent ceramic filter plate.
Ceramic Foam Filter For Metal Filtration is mainly made of materials with excellent strength, high temperature impact resistance and chemical corrosion resistance. Can withstand high temperatures up to about 1760 ℃. Therefore, it is suitable for the casting of all copper alloys and cast iron. Foam ceramic filter can significantly improve the quality of cast iron parts and reduce the scrap rate. They can also be used in continuous casting and rolling processes and can be manufactured in all standard sizes and different thicknesses. The basic materials of foam ceramic filters are silicon carbide, zirconia and alumina.
Non-metallic inclusions in foam ceramic filter castings are an important factor leading to casting defects. They affect the surface finish, mechanical properties and processing properties of castings, and lead to an increase in scrap rate. The foam ceramic filter products are used to remove inclusions, reduce turbulence, and achieve rapid and stable metal liquid filling flow, thereby improving the quality of castings. It has a significant filtering effect on all types of steel such as carbon steel, stainless steel, cobalt-based nickel-based superalloys.
The main performance of Ceramic Foam Filter For Metal Filtration
1. Alumina foam ceramic filter, applicable temperature is 1250℃, suitable for filtration and purification of aluminum and alloy solution. It is widely used in general sand casting such as tidal casting and aluminum casting casting. Alumina foam ceramic filter products are effective solid inclusions in molten metal. The product has a coarse pore size of 10 ppi and a fine pore size of 70 ppi. Specifications and models can be made according to user requirements.
2. Made of pure zirconia material, the temperature can reach 1760℃, and it is insensitive to different pouring temperature changes. Excellent raw materials and advanced production technology ensure that the filter has stable dimensional tolerances, meet the requirements of manual molding and a more efficient mechanized production line, and ensure product quality
Sorry, the comment form is closed at this time.