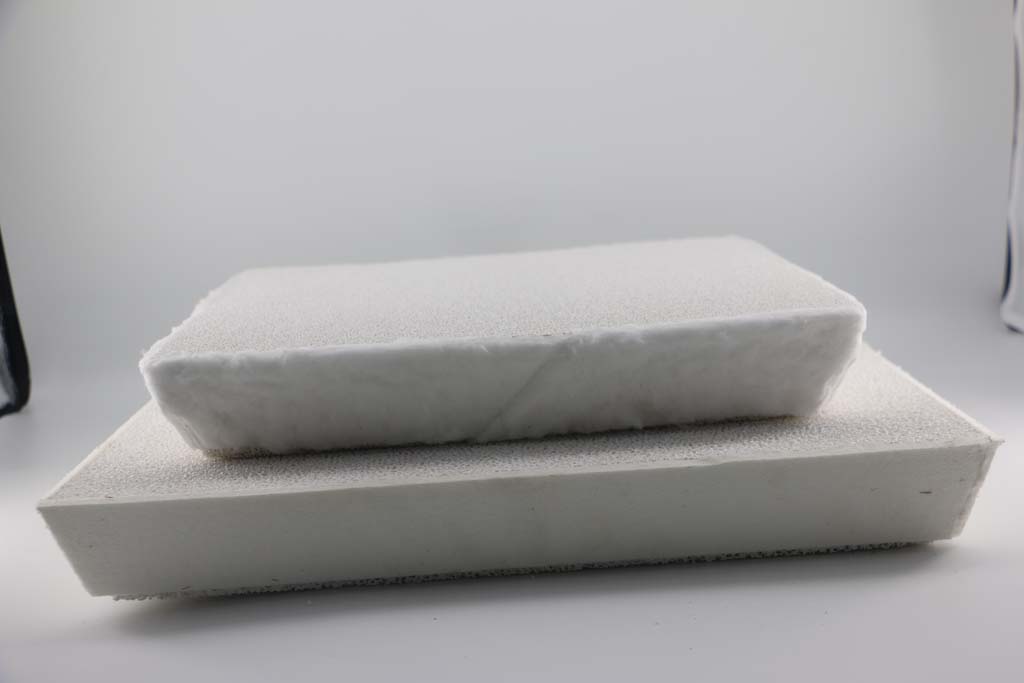
12 3月 Ceramic Foam Filter For Metal Filtration
Ceramic Foam Filter For Metal Filtration is a unique class of lightweight materials consisting of a relatively regular array of hollow cells arranged in a three-dimensional network.
Porous ceramics are divided into two subclasses consisting of either open or closed cells.
The closed-cell ceramics can be used as a network of soap bubbles. The porous ceramics can be widely used in catalyst carriers, hot gas collectors, molten metal filters, chemical sensors and separation membranes.
Al2O3 matrix ceramic foam is a kind of representative porous ceramic, which has high resistance to molten aluminum attack and is used in filtering molten aluminum.
The three main processes for the fabrication of ceramic foam are the replica technique, the sacrificial template method, and the direct-foaming technique.
The most common preparation method for Ceramic Foam Filter For Metal Filtration is the polymeric sponge method which involves the impregnation of polyurethane sponges with slurries containing ceramic particles and appropriate binders followed by pyrolysis and sintering at a special temperature.
From key components in the aircraft and automotive industries to household applications, aluminum cast parts are found in 90% of manufactured products and equipment.
However, in reality, molten aluminum used to produce metal castings often contains impurities and inclusions that are harmful to the final cast metal product.
At present, the filtration technology using ceramic foam filters has been considered a successful method to reduce the inclusions in the molten metal during the casting of metal parts.
The production method of Ceramic Foam Filter For Metal Filtration is to immerse polyurethane foam in ceramic slurry, dry, bake, and finally fire into foam in an oven.
Before the pouring process, the filter was experimentally tested to measure size, weight, cold press strength and permeability.
After pouring, the filter is cut into several parts to measure the macro and micro structure of the filter and to ensure that the impurity particles are captured by the filter.
The thermal shock characteristics are obtained by pouring liquid aluminum when the filter is placed in the gating system to ensure that the filter can withstand the temperature of the aluminum alloy.
Further experiments were carried out to investigate and determine the efficiency of the produced ceramic foam filter on the quality of castings.
A successful method for inclusions in molten metal during the process.
Ceramic Foam Filter For Metal Filtration has good strength and fracture toughness. The hump slurry content is changed by modifying the polymer sponge, and the thickness of the ceramic coating is increased by the multi-coating method to improve the mechanical properties of Ceramic Foam Filters. Centrifugal slip casting can avoid the pores and cracks produced by the pyrolysis of organic sponge, form the best accumulation of ceramic particles, and minimize the defect size of the cell pillar. Therefore, the final product has dense cell rods and good mechanical properties. In addition, the radial distribution of Al, 0 and ZrO particles can generate residual stress, which helps to further improve the mechanical properties of foam ceramics.
No Comments