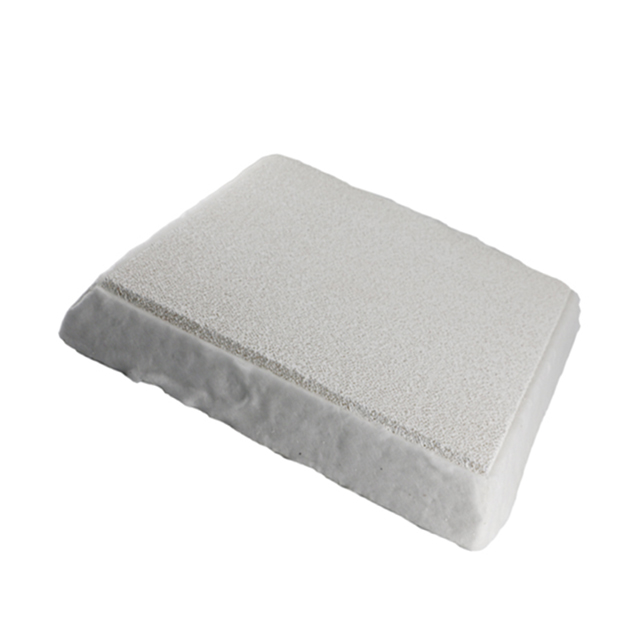
08 10月 Ceramic Foam Filter Foundry
Ceramic Foam Filter Foundry is used in the metallurgical industry and foundry.
With Ceramic Foam Filter Foundry , you can solve all the problems associated with the presence of inclusions. From the point of view of casting quality, filtering provides an increase in the mechanical and operational properties of castings.
Advantages obtained using ceramic foam filters:
Optimum conditions for filtering liquid metal are ensured throughout the entire spill process;
Optimized casting speed;
Filters trap impurities and oxide films;
Simplification of the gating system;
Improving the surface and quality of castings;
The possibility of using direct casting technology on the filter;
Improving the mechanical characteristics of castings and achieving better density of castings;
Decrease in quantity of marriage.
Closed pores, cracks, and openings on work surfaces are not acceptable. The side walls of the filters can be filled with ceramic.
1.3 Filters in a kink should not contain extraneous inclusions visible to the naked eye.
1.4 Packaging and labeling
1.4.1. Cast filters are packed in cardboard boxes that protect products from damage during transportation and storage.
1.4.2 Packaging ensures the safety of the cargo during transportation by any type of covered transport, and exclude its moisture.
1.4.3 Marking of filters is carried out with indelible paint at each packing place, indicating:
– type of filter
– the size
– porosity (10.20.30 PPI)
– date of manufacture
– name number of the employee of the Quality Department;
Additional stickers (ATTENTION FRAGILE, etc.)
2. Security requirements
2.1. Filters are refractory materials and are fire and explosion proof.
2.2 Ceramic Foam Filter Foundry in their composition do not contain harmful substances and do not have a negative effect on human health.
3. Acceptance rules and test methods
3.1 Each batch should be accompanied by a document on the quality of the material, which should contain the following:
-the name of the manufacturer and supplier;
-product name;
– net weight and number of packing places;
-results of checking the material for compliance with these technical requirements for all indicators.
3.2 Acceptance of products from the consumer is carried out according to the indicators of table 1 and paragraphs 1.2 and 1.3, from each incoming batch.
3.3 Control sample in an amount of at least 20 pcs. Ceramic Foam Filter Foundry is selected selectively from each batch to examine the appearance, fracture and geometric dimensions.
3.4 Determination of the geometric dimensions of filters and dimensional tolerances is carried out using an electronic, digital vernier caliper with marking jaws, the division price is 0.01 mm.
3.5 The number of pores per linear inch is determined using a measuring magnifier GOST 25706-83 and caliper GOST 166-89.
3.6 Physico-chemical parameters are checked on three samples, selectively taken from the control and previously passed control in appearance and geometric dimensions.
3.7 If at least one indicator does not comply with these technical requirements, a double number of samples is taken for
re-control. Repeated results are considered final, and if they are inconsistent, the entire batch is rejected.
Sorry, the comment form is closed at this time.