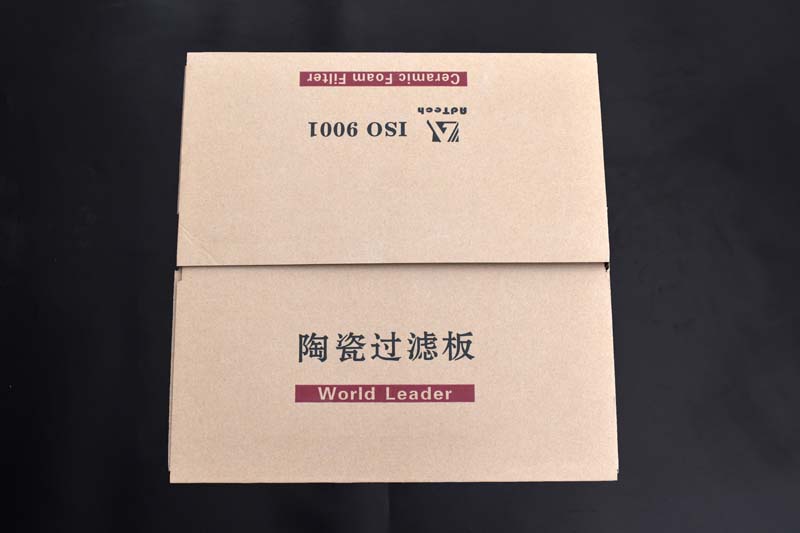
18 8月 Ceramic Foam Filter Naz Aluminium filters
Ceramic Foam Filter Naz Aluminium filters suspended matter and non-metallic particles in molten aluminum through tiny holes inside. In the aluminum casting process, these aluminum slags are trapped on the surface of the filter medium, and the fluid passes through the microporous channel to produce various physical effects, achieving the effects of mechanical filtering, purification, diffusion, and fluidization.
Ceramic Foam Filter is an alumina-based ceramic foam filter, which can be widely used for filtering in the casting process of aluminum, aluminum alloy and other non-ferrous metals. This type of filter can be placed in a standard filter box, holding furnace, etc.
Ceramic Foam Filter Naz Aluminium is used in the casting process to filter solid slags such as metal oxides contained in molten metal, thereby improving the quality and yield of castings. Therefore, the use of ceramic foam filters promotes technological progress in the casting industry.
Ceramic foam filters are basically divided into 6 pore sizes: 10PPI, 15PPI, 20PPI, 25PPI, 30PPI and 40PPI.
The aluminum melting purifier is usually installed between the furnace outlet and the filter box.
The melt flows into the box of the degassing device, and the inert gas is broken by rotating the rotor, forming a large number of dispersed bubbles into the aluminum melt.
After collision, capture, surface adsorption and partial pressure, the hydrogen and oxide slag in the melt are carried out from the surface of the molten aluminum along with the gas to form scum. The aluminum alloy melt flows out from the outlet of the degassing device, which is continuously online The purpose of the above refinement.
The online rotor degassing device is developed on the basis of absorbing the advantages of the mainstream box-type degassing device on the market. Many key technologies such as box sealing and anti-turbulence on the surface of molten aluminum have been improved to ensure the high efficiency, continuous stability and low cost of the degassing device.
Maintenance of degassing tank
1.During continuous casting, clean up the scum on the surface of the molten aluminum in the degassing tank every two days: stop the heater, lift the cover of the degassing tank and move it to the side, use a shovel to remove the scum on the surface of the molten aluminum Then, quickly close the degassing box cover. After the box cover is in the correct position, start the heater.
2. When replacing the alloy, first lift the degassing tank cover, after cleaning the scum on the surface of the molten aluminum, place the degassing tank cover, start the heater, and then put the molten aluminum in the tank.
3. If the deaeration box is not used for a long time, the deaeration box should be cleaned: lift the deaeration box cover and move it aside. First clean up the scum on the surface of the molten aluminum, and then drain the molten aluminum . Clean up after the temperature in the box decreases. After cleaning, be sure to paint in the box.
4. Matters needing attention
4.1 When cleaning the scum on the surface of the molten aluminum, you must pay attention to safety to prevent being injured by the high-temperature molten aluminum.
4.2 Before the molten aluminum in the degassing tank is discharged, the scum on the surface of the molten aluminum must be cleaned. If the slag is not cleared first, the slag will be deposited on the bottom, which is difficult to remove. After a long time, it will damage the heater and rotor.
4.3 In short, it is necessary to clean the slag first and then put the molten aluminum!
No Comments