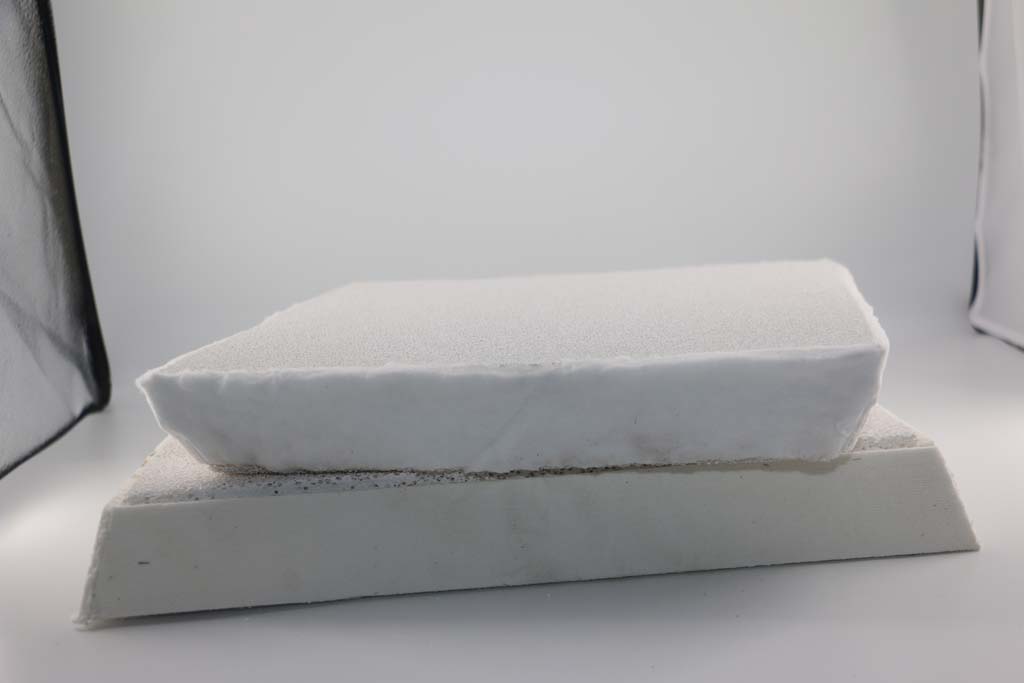
26 2月 Ceramic Foam Filterer For Foundry
Ceramic Foam Filterer For Foundry can effectively remove or reduce the inclusions in the aluminum alloy melting and casting, improve the purity of the molten metal, and make the surface of the molten metal castings smooth, uniform in structure, increased in strength, and reduced in rejects, while further reducing the machine Processing loss improves labor productivity.
By having two end faces and an outer peripheral face and separating the partition walls, a porous body formed with a plurality of main flow paths of the purified fluid that penetrates from one end face to the other end face.
Ceramic Foam Filterer For Foundry filters solid slags such as metal oxides contained in molten metal, thereby improving the quality and yield of aluminum alloys. Therefore, the use of Foam Ceramic Filter promotes technological progress in the foundry industry.
The main defects of aluminum wire ingots are
1. Crack
The reason is that the temperature of the molten aluminum is too high, the speed is too fast, and the residual stress is increased; the silicon content in the molten aluminum is greater than 0.8%, and the same melt of aluminum and silicon is formed, and then a certain amount of free silicon is generated, which increases the thermal cracking of the metal: Or insufficient cooling water. When the surface of the mold is rough or no lubricant is used, the surface and corners of the ingot will also crack.
2. Slag inclusion
The slag inclusion on the surface of the aluminum wire ingot is caused by the fluctuation of the molten aluminum, the rupture of the oxide film on the surface of the molten aluminum, and the scum on the surface entering the side of the ingot.
Sometimes lubricating oil can also bring in some slag.
The internal slag inclusion is caused by the low temperature of the molten aluminum, the high viscosity, the inability of the slag to float in time or the frequent changes of the molten aluminum level during casting.
3. Cold compartment
The formation of the cold barrier is mainly caused by excessive fluctuations in the level of molten aluminum in the mold, low casting temperature, excessively slow ingot casting speed, or the vibration and uneven drop of the casting machine.
4. Stoma
The pores mentioned here refer to small pores with a diameter of less than 1 mm.
The reason is that the casting temperature is too high and the condensation is too fast, so that the gas contained in the aluminum liquid cannot escape in time, and after solidification, small bubbles are gathered and left in the ingot to form pores.
5. Rough surface
Because the inner wall of the crystallizer is not smooth, the lubrication effect is not good, and aluminum tumors on the crystal surface are formed in severe cases. Or because the ratio of iron to silicon is too large, the segregation phenomenon caused by uneven cooling.
6. Leakage of aluminum and re-analysis.
The main reason is the operation problem, and the serious one can also cause nodules.
No Comments