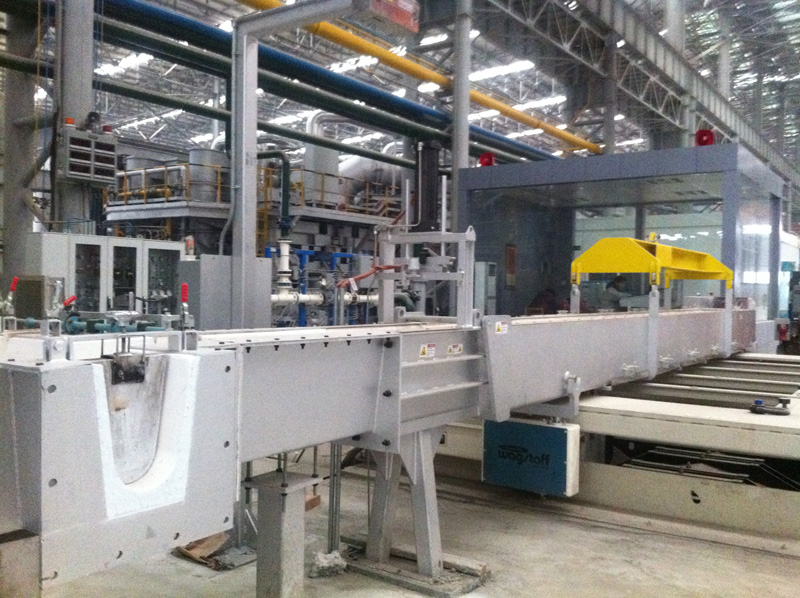
05 5月 Heat Resistant Ceramic Launder For Aluminum Foundry
Heat Resistant Ceramic Launder For Aluminum Foundry
Ceramic Launder is an important part of the aluminum and aluminum alloy casting process. It is mostly installed between the melting furnace and the casting platform and on the casting platform. The main function is to drain the aluminum melt.
The flow cell installed between the melting furnace and the casting platform is wrapped with a metal (mostly iron plate) casing and lined with thick aluminum silicate fiber paper to ensure that the flow cell is not directly in contact with the iron shell and is easily broken. Plays a good role in insulating aluminum liquid.
During the installation process, it is installed at an appropriate inclination, and the aluminum liquid flows by gravity.
The aluminum liquid flows directly from the furnace eye of the melting furnace, passes through the launder, and is transported to the casting machine platform, and then is diverted to the splitter disc through the upper trough of the casting machine, and then flows to the crystallizer, and finally cooled and crystallized into the finished aluminum rod.
In the aluminum liquid transport distance between the melting furnace and the platform, a filter box is often arranged, and a ceramic filter plate is placed on the filter box for filtering the dross in the aluminum liquid.
However, due to the large area of the ceramic filter plate and the large through-hole ratio (80%-90%), the aluminum liquid cannot completely cover the surface when passing through the filter plate, but simply passes through a certain filtering surface and causes the filter mesh to be blocked. The filter plate breaks and affects the aluminum casting production.
A flow tank with a function of lifting aluminum liquid is arranged behind the filter box. When the aluminum liquid flows through the filter plate in the filter box, it is responsible for raising the filtered aluminum liquid to a height before filtering, thereby satisfying the uniform and comprehensive passage of the aluminum liquid. The surface of the filter plate serves to filter and purify the aluminum liquid.
Ceramic Launder For Aluminum Foundry has a long life lining, adopts new high-silicon melt material forming technology, strong corrosion resistance, non-stick aluminum, non-contaminating performance to aluminum liquid, and meets the requirements of high added value and high technical performance. The production technology of aluminum products is flawed.
Product advantages
Good insulation performance, reasonable design and long service life;
It is integrally molded with noble molten material and has high dimensional accuracy;
The lining has high strength, erosion resistance, heat shock resistance and smooth surface;
The inner liner has strong corrosion resistance to aluminum, zinc and magnesium alloys, enhances the use effect of the molten metal transfer equipment, and strengthens the service life of special alloys;
The temperature drop of the metal liquid during use is 2 ° C per meter, resistant to erosion, heat shock and smooth surface.
Instructions for usage
Corresponding to the drawing structure, the flow cell is installed to ensure that the overall flow path is clean, no damage, no gap.
Uniformly preheat the installed flow path, heat up at a constant speed for 6-8 hours, check the surface of the lining red, ie 800 °C, to remove the adsorbed crystal water, close to the casting temperature, safe and efficient use.
If the tank flow tank does not have electric heating baking conditions, it must be baked with flame. The key one is to control the flame temperature, and the other is to avoid direct flame grilling and avoid the thermal stress generated by local heat, causing the liner, tube body, disc body or filter plate to burst. The flame is divided into a weak flame (red soft flame), a medium flame (yellow), and a strong flame (blue and white).
Sorry, the comment form is closed at this time.