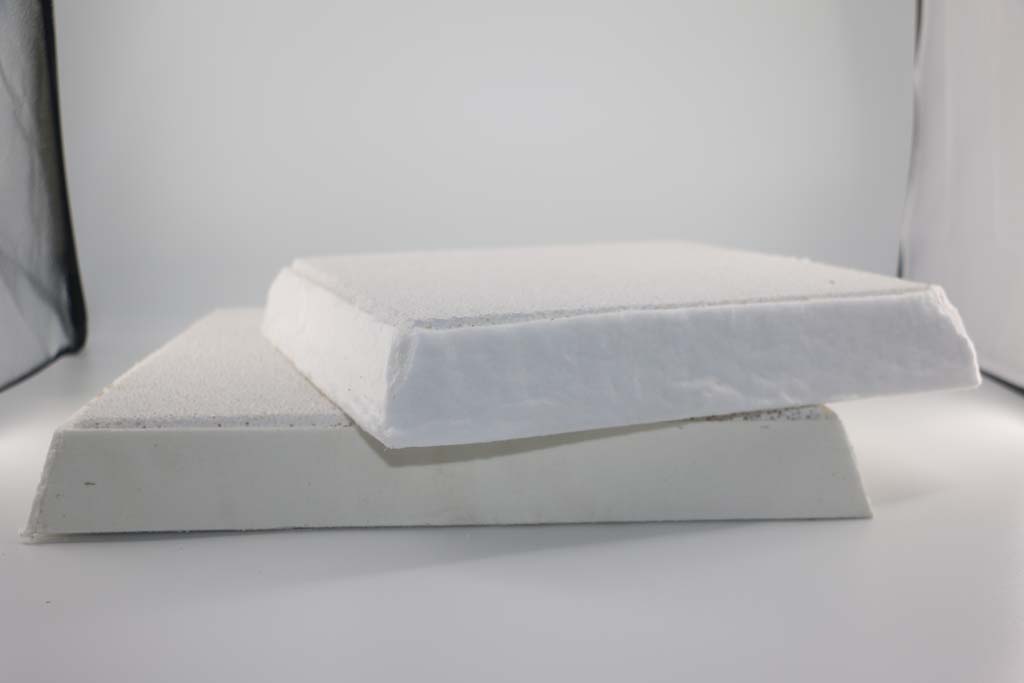
12 3月 Ceramic Porous Ceramic Filter
Ceramic Porous Ceramic Filter (CFF) have been used commercially in the foundry industry for more than four decades for the production of premium quality aluminium castings for use in such applications as in the aerospace industry.
In recent years, Ceramic Porous Ceramic Filter has become more important in the physical purification of metals, for the ferrous and nonferrous industries.
The nonferrous industry uses the largest amount of this filtering media, especially the aluminium casting industry.
In 1992, Aubrey and Dore reported that eight million metric tons of aluminium was filtered using CFF, and this means that about 50 percent of all the aluminium produced in the world in that year, was purified through this filtering media.
Porous ceramics are now widely applied as materials for filtration of fluid in high-temperature applications.
It is widely accepted that based on their structural properties, CFFs can remove exogenous and indigenous inclusions in the melts, and moreover, have low flow resistance and high filtration efficiency for particles over 10-20 microns.
The structure of Ceramic Porous Ceramic Filter creates a unique, tortuous path for the fluid to flow, which captures inclusions and allows clean, smooth-flowing metal to exit into the mould cavity. CFFs are generally accepted as the best filters for casting. Their main advantages are: high filtration efficiency, turbulence reduction, refractoriness, and erosion resistance, for the most demanding casting applications.
Permeability is an important parameter for the characterization of CFFs, since it is required to predict the flow rate obtainable under a given pressure drop or to be able to predict the pressure drop necessary to achieve a specific flow rate. The relationship between these quantities can be expressed as a function of the fluid flow, and medium properties and is obtained by fitting the experimental data with permeability equations.
Ceramic Porous Ceramic Filter possess flu attractive set of properties such as high porosity, high temperature stability ete,therefore they have been widely used as casting steel and casting iron field.
Ceramic Porous Ceramic Filter uses refractory raw materials as aggregates, and is combined with a ceramic filter material made by high-temperature sintering such as binders. The structure has a large number of conventional and controllable pores.
In addition to the characteristics of high temperature resistance and corrosion resistance, it also has the characteristics of uniform pore size and high air permeability, so it can be widely used as a filter in the aluminum casting industry.
In the aluminum casting production process, the mechanism of filtering molten aluminum is mainly inertial collision, diffusion and interception.
Inertial collision: The impurity particles in the fluid flowing through the micropores of the porous ceramic filter element are caught by contact with the walls of the micropores due to inertia. The inertial impact is proportional to the square of the diameter of the impurity particles, and inversely proportional to the flow velocity and fluid viscosity.
Diffusion: The impurity particles leave the streamline due to Brownian motion and contact the wall of the microporous channel, thereby being captured. Diffusion capture is inversely proportional to flow rate and fluid viscosity.
Retention: The impurity particles are captured because the pores are larger than the micropores, which belongs to surface filtration. The retention is only related to the size of the impurity particles, and has nothing to do with the flow rate and fluid viscosity.
No Comments