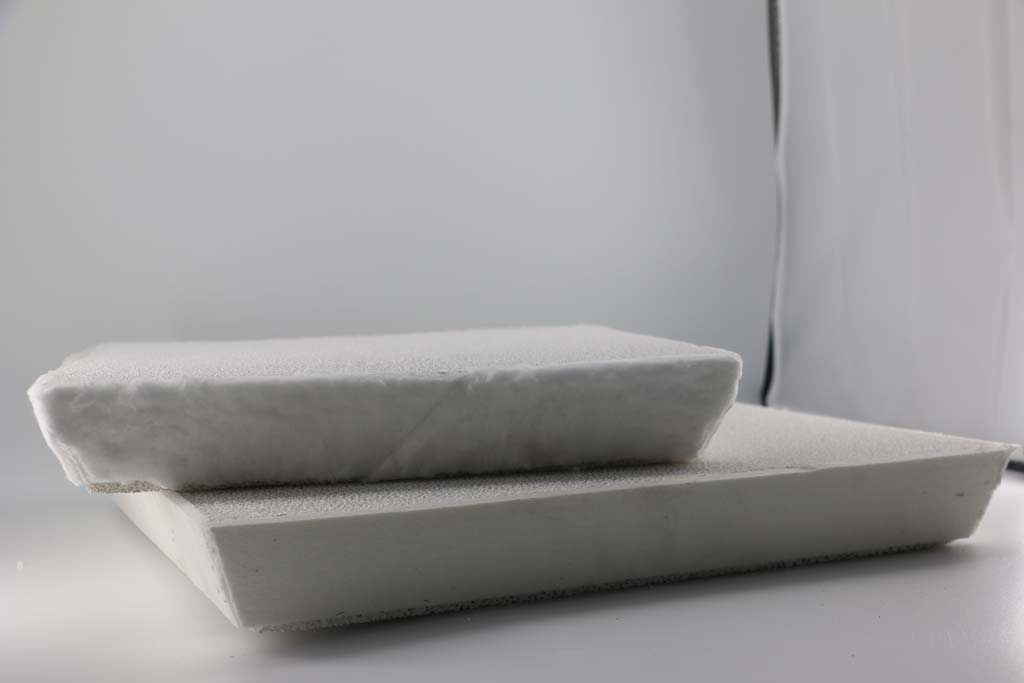
25 2月 Filter Zirconia Ceramic Plates
Filter Zirconia Ceramic Plates has great benefits to the strip foil and its products (such as can blanks, car finishing materials, PS printing plates, etc.) after purifying liquid aluminum.
Filter Zirconia Ceramic Plates employs domestic research talents and adopts the formulas and processes of many foreign companies. It is carefully developed by introducing foreign production equipment and some raw materials.
5083 belongs to the Al-Mg-Si series alloy and has a wide range of applications. Especially the construction industry cannot do without this alloy. It is the most promising alloy.
Good corrosion resistance, excellent weldability, good cold workability, and medium strength.
The main alloying element of 5083 is magnesium, which has good forming performance, corrosion resistance, weldability, and medium strength. It is used to manufacture aircraft fuel tanks, oil pipes, and sheet metal parts of transportation vehicles and ships, meters, street lamp brackets and rivets, Hardware products, electrical enclosures, etc.
AL-Mg series alloy is the most widely used anti-rust aluminum. This alloy has high strength, especially fatigue resistance: high plasticity and corrosion resistance, and cannot be strengthened by heat treatment.
The plasticity is good during semi-cold work hardening, and the plasticity is low during cold work hardening. It has good corrosion resistance, good weldability, poor machinability, and can be polished.
Uses are mainly used for low-load parts that require high plasticity and good weldability, working in liquid or gaseous media, such as mailboxes, gasoline or lubricating oil pipes, various liquid containers and other low-load parts made by deep drawing: Wire is used to make rivets.
Casting generally adopts vertical or horizontal water-cooled semi-continuous casting method.
In order to improve the structure and surface quality of the billet in vertical casting, electromagnetic crystallization tanks, short crystallization tanks and hot top casting methods (see solidification of metals) have also been developed.
The water-cooled semi-continuous casting method is to introduce liquid metal into a water-cooled crystallizer through a launder, so that the liquid metal is cooled to form a solidified shell, which is pulled by the base of the casting machine or dropped out of the crystallizer by its own weight to form an ingot.
The process parameters vary greatly due to the alloy composition and billet size. Generally, the casting speed and cooling rate should be increased as much as possible, and the height of the crystallization tank should be reduced.
The casting temperature is usually 50-110°C higher than the liquidus line of the alloy. In addition, the continuous casting and rolling process of aluminum strip has been developed.
Non-metallic inclusions in castings are the main factor leading to casting defects. They affect the surface finish, mechanical and processing properties of castings and lead to an increase in the rejection rate. Foam ceramic filter products are precisely to remove inclusions and reduce turbulence to achieve a fast and stable molten metal filling flow rate, and therefore improve the quality of castings.
No Comments