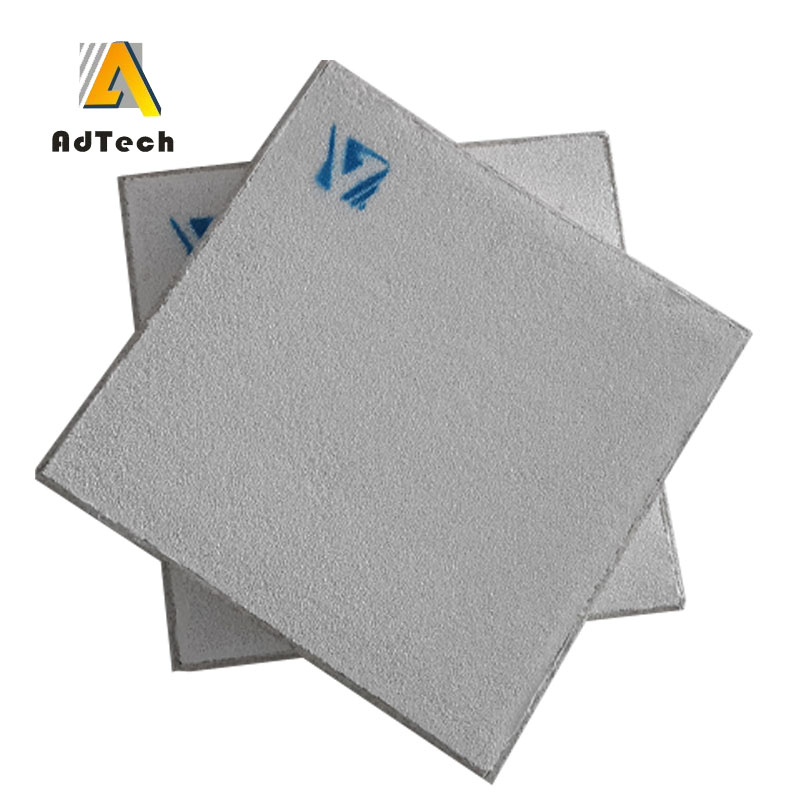
29 4月 Filters used in foundry
Filters used in the foundry for Aluminium
The quality of the aluminum melt is important, it greatly affects the subsequent processing properties and the quality of the final product.
Therefore, all countries in the world attach great importance to the purification of aluminum melt.
There are many reasons for aluminum pollution. On the one hand, during the melting process, aluminum is exposed to the furnace atmosphere in a molten or semi-molten state, which is prone to oxidation, easily reacts with water vapor to absorb hydrogen, and easily forms various forms of non-metallic slag. And coarse intermetallic particles and the like.
On the other hand, part of the waste material in the composition charge carries some non-aluminum impurities during the circulation.
Since the waste comes from the process waste and waste of the various processes of the factory and the waste outside the factory, the route is different, the composition is complex, and the quality is also poor.
These impurities tend to cause bubbles and inclusions in the slab, which seriously affect the purity of the metal melt, thereby further affecting the processing properties, mechanical properties, corrosion resistance and appearance quality of the product.
Filters used in foundry Aluminium can effectively remove all kinds of fineness in the aluminum water to micron-sized inclusions, making the aluminum water into a smooth laminar flow, which is good for filling.
It has good mechanical strength and chemical stability, and superior aluminum washability.
Strictly controlled hole size and through-hole ratio for stable filtration.
The Filters used in the foundry are surrounded by a sealed heat-expandable ceramic fiber gasket, which helps the ceramic foam filter to seal in the filter box, ensuring no metal liquid bypass.
Its installation and use, in general, need to pay attention to the following aspects
1. Correct selection of filter plates
The size of the filter plate and the number of holes must be selected in consideration of the flow rate range of the specific casting type, the maximum liquid level of the metal during filtration, the total filtration amount, and the cleanliness of the original aluminum liquid.
2. Pre-filtration treatment can not be ignored
Such as molten aluminum furnace and holding furnace, normal slag, cleaning furnace, and furnace refining. In particular, an in-line degassing device is still necessary because it not only reduces the hydrogen content of the melt, but also removes some of the non-metallic inclusions.
3. The filter plate must be adapted to the square refractory filter box
The two are adapted to seal, to prevent the metal from flowing into the casting box from the gap without being filtered, and also to avoid the failure of the foam filter plate to float in the aluminum water due to the excessive light weight.
4. Preheating before use
Preheat to remove moisture and facilitate initial transient filtration. Preheating can be carried out using electrical or gas heating. Under normal circumstances, it takes about 15 minutes.
5. During normal filtration, no slag is required to avoid knocking and vibrating the filter plate. At the same time, the launder should be filled with aluminum water to avoid too much disturbance of the aluminum water.
6. After casting, drain the metal in the flow cell and filter plate. There is a vibrator abroad that is placed on the filter plate and shaken for one minute to shake off about 75% of the remaining liquid metal from the filter plate.
7. Finally, clean the perimeter and remove the filter plate after solidification.
ADTECH is one pioneer followed by the International Enterprise, which keeps focusing on the manufacture of metallurgical materials.
1 . Ceramic Foam Filter
2 . Degassing Unit
3 . Filter Box
4 . Hot-top casting series
5 . Roll casting nozzle
6 . Flux series
7 . Other Metallurgical Material
Sorry, the comment form is closed at this time.