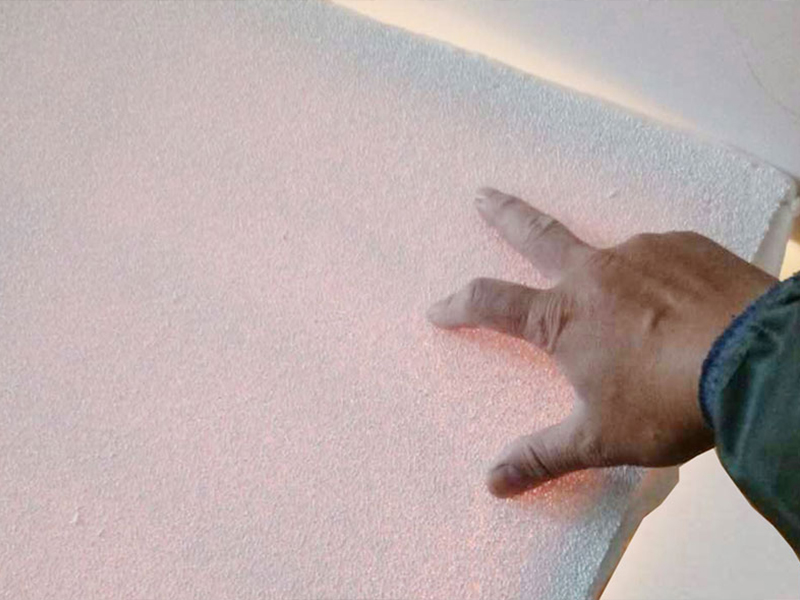
28 7月 Foundry Ceramic Filters Malaysia
Foundry Ceramic Filters Malaysia is becoming a common practice in more and more aluminum foundries. Foundry Ceramic Filters not only have a good filtration efficiency is not enough, it must also have a high and consistent flow rate, good strength, high capacity and good dimensional accuracy.
This must be achieved at the lowest possible cost. Some of these parameters conflict with each other. For example, if the ceramic foam filter has a very large capacity, the filtration efficiency may be affected. Therefore, the most effective filter is carefully designed to provide the best performance on all these parameters.
Ceramic foam filters are introduced into aluminum foundries for use in critical, complex, thin-walled aerospace aluminum castings.
Foundry Ceramic Filters Malaysia is a new type of molten metal filter developed in recent years. It is used to reduce casting defects and plays a vital role in the metal casting and foundry industry. It is used to filter impurities in molten metal to improve The quality and performance of the final product.
Even the slightest non-metallic impurities in molten metal can have a destructive effect on the performance and strength of finished metal products.
This may cause the final product to fail to meet the necessary quality standards; ceramic filters play an important role in removing these impurities and ensuring high-quality castings.
Advantage of Ceramic Foam Filters
1.High strength without loose ceramic particles or powder.
2.Three dimensional connected mesh structure and high porosity.
3.Large surface area of slag collection, large inner surface area of filtering.
4.Excellent thermal shock resistance.
5.Various sizes, shapes and pore sizes are available.
6.Particles larger than the pore size are captured at the top of the ceramic foam filter.
7.Smaller particles are captured on the filter cake created by the larger particles.
8.Finer particles are captured within the pores in the filter.
Aluminum is the second most available metal in the world. It is lighter and non-corrosive, and will develop rapidly in the future. Aluminum has been used in the packaging industry for a long time because of its light weight, good formability, good thermal conductivity, high strength, and non-corrosiveness. These outstanding characteristics have also led to applications in automation, construction and other fields.
After proper alloying and treatment, aluminum can resist corrosion from water, salt and other environmental factors, as well as various other chemical and physical factors.
Primary aluminum is cast into ingots and shipped to customers or used to produce aluminum alloys for various purposes.
The grain refiner affects the aluminum alloy during the solidification stage.
The modifier changes the AlSi eutectic structure from acicular to spherical, thereby significantly improving the ductility of the alloy.
Other master alloys are used in aluminum forging alloys and casting alloys for composition adjustment and structure control.
No Comments