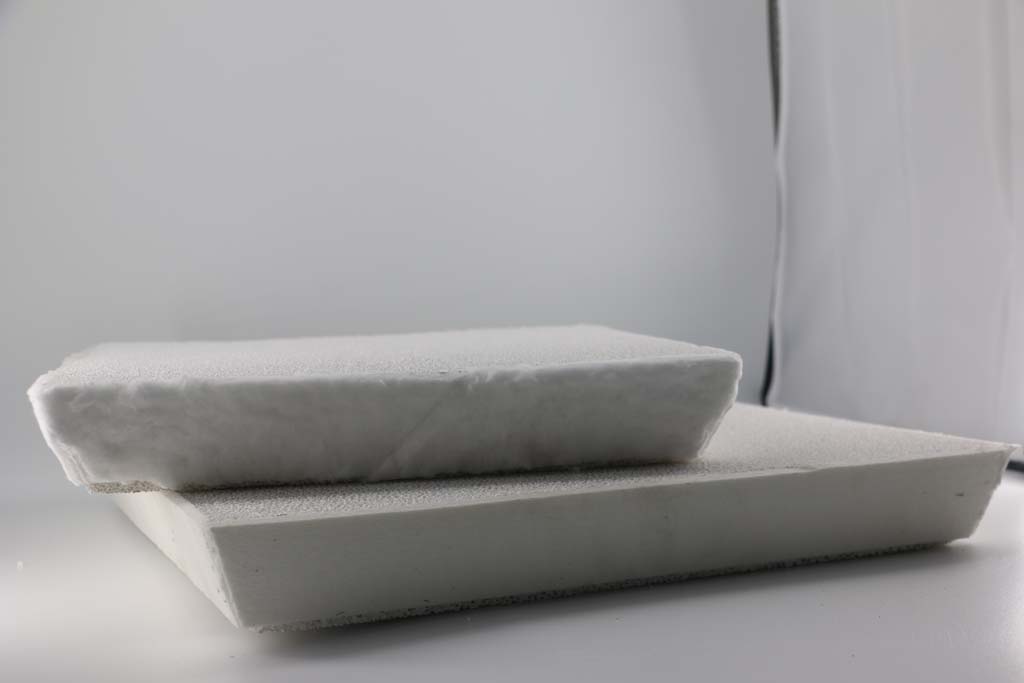
23 2月 Foundry Ceramic Foam Filter For Metal Casting
Foundry Ceramic Foam Filter For Metal Casting is to immerse polyurethane sponge in ceramic slurry, squeeze out the excess part, dry, and finally sinter at high temperature to form a three-dimensional porous ceramic material. It is a pipe with twists and turns connected to each other but uneven in thickness.
It is precisely this uneven tube wall that plays a key role in trapping small inclusions in the aluminum melt. This structure also increases the path through which the aluminum melt contacts the ceramic part of the Ceramic Foam Filters For Casting, thereby increasing the probability of inclusion particles being attached.
In the practice of casting production, filtration efficiency can be used to evaluate the purification effect of Foundry Ceramic Foam Filter For Metal Casting on liquid casting alloys.
Samples were taken from the top and bottom of each casting in the same heat or the same ladle of molten metal to determine the cleanliness of the filtered and unfiltered castings.
Use an optical microscope and a scanning electron microscope to analyze the inclusion assembly area.
The slag inclusion defects in the castings greatly affect the production efficiency and economic benefits of the iron casting plant.
Coarse inclusions on the surface reduce the surface finish of the casting, and cause the casting to be directly scrapped in severe cases.
Defects of inclusions under the skin are usually only found in the processing stage, assembly stage or actual use stage.
For example, in the processing workshop, the presence of macroscopic or microscopic inclusions will reduce the machinability of castings and the life of machining tools.
The inclusions that exist during assembly or during service will reduce the mechanical properties or service performance of the casting, such as causing leakage under pressure.
Castings scrapped during processing, assembly or use usually cause higher losses, because E has performed multiple operations before.
No Comments