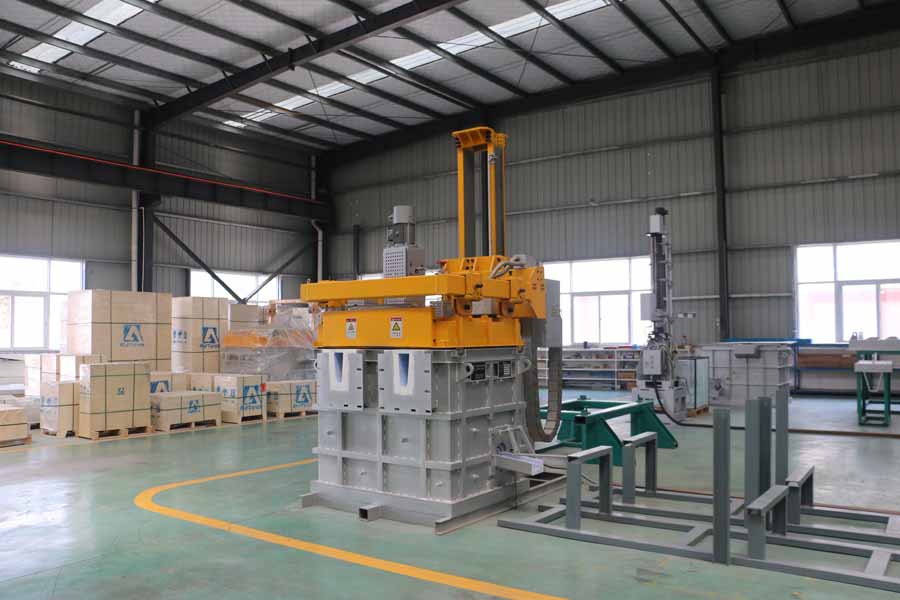
01 3月 Liquid Aluminum Refining System
Liquid Aluminum Refining System, in which the degassing unit body is integrally cast and sintered with high-strength imported castable, which has good thermal shock resistance.
The insulation layer on the outside of the box is made of high-quality imported nanoboard, lightweight fiberboard, and other materials, which have good insulation performance.
The box cover is integrally cast and sintered with lightweight castables.
The working principle of the degassing unit is to blow a certain amount of Ar-Cl2 or N2-Cl2, pure Ar, N2 gas into the bottom of the aluminum melt through the high-speed rotating rotor, and the impeller is fully chopped to form dispersed bubbles to make the aluminum liquid and pure Full contact with Ar or N2 gas.
According to the principle of air pressure difference and surface adsorption, when bubbles rise, hydrogen and oxidized slag can be adsorbed, scum is formed on the surface, and hydrogen is carried out to achieve the purpose of removing hydrogen and slag.
During the operation of the Liquid Aluminum Refining System, the motor drives the rotation of the rotor to break the nitrogen or argon blown into the aluminum melt into a large number of dispersed bubbles and disperse them in the molten metal.
Bubbles in the melt, relying on the gas partial pressure difference and the principle of surface adsorption, absorb hydrogen in the melt, adsorb oxidized slag, and are taken out of the melt surface as the bubbles rise so that the melt can be purified.
Because the bubbles are small and dispersed, they are evenly mixed with the rotating melt, and then they rotate in a spiral shape to slowly float up. The contact time with the melt is long, and it will not form a continuous linear rise to generate airflow, thereby removing the harmful hydrogen in the aluminum melt and significantly improving The purification effect.
Why is the Liquid Aluminum Refining System needed in the aluminum smelting process?
Aluminum and aluminum alloy melts contain a large amount of hydrogen, metal, and non-metallic inclusions.
If the above harmful substances cannot be removed in time before casting, casting defects such as pores, inclusions, and looseness will be formed inside and on the surface of the casting, which will seriously affect the physical, chemical, mechanical, and various deep processing properties of the casting, and produce a lot of waste products.
No corrosion to the lining of the ladle or crucible furnace. Since argon or nitrogen is used as the refining medium, there is no pollution to the environment.
No Comments