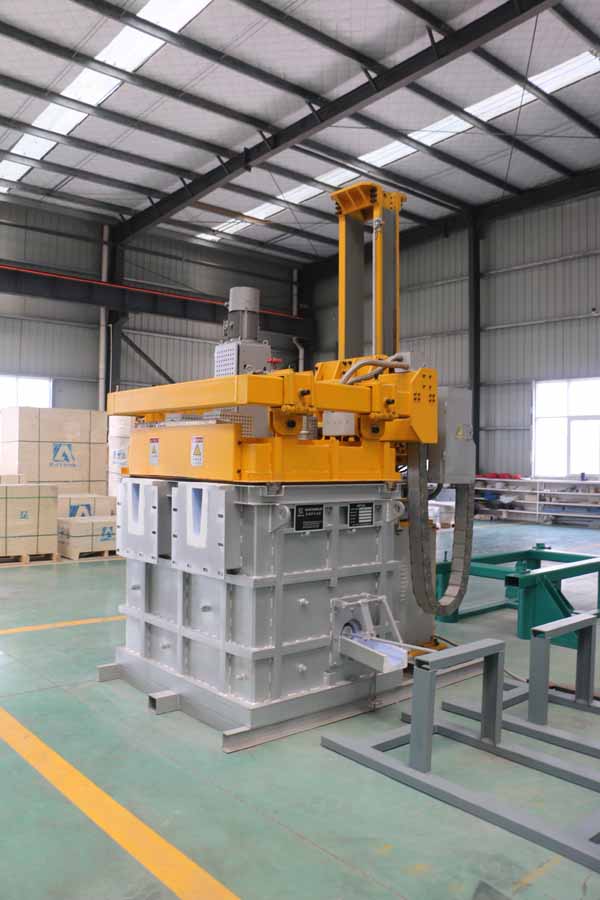
28 4月 Melt Aluminum Degassing
Melt Aluminum Degassing uses the nitrogen blown into the aluminum alloy melt to be crushed by the rotating silicon nitride rotor, forming a large number of diffusion bubbles, so that the aluminum alloy liquid and nitrogen are fully contacted in the processing tank.
According to the principle of pressure difference and surface adsorption, the bubbles absorb the hydrogen in the melt and adsorb the oxidized slag (the collision is larger, the radial interception is smaller).
Slag forms on the surface of the melt. The aluminum alloy melt flows from the outlet of the degassing device (located in the lower part of the dirt) to the casting machine.
The aluminum alloy liquid continuously enters the degassing device, and the nitrogen is continuously blown in. Through the degassing process, the purpose of purifying the aluminum alloy liquid is realized.
Aluminum alloy is the most widely used non-ferrous metal structural material in the industry.
It is widely used in aviation, aerospace, automobile, machinery manufacturing, shipbuilding, chemical industry and other industries. With the rapid development of industrial economy, the demand for aluminum alloy continues to increase.
The degassing process is essential to remove dissolved hydrogen and non-metallic content from molten metal before casting to achieve the best quality.
Hydrogen is dissolved in the molten material, diffuses into the rising bubbles of molten gas, and is transported to the surface of the molten material.
Hydraulic lifting mechanism
In order to ensure its accurate positioning, the molten aluminum degassing unit has a hydraulic lifting device, which is used to control the vertical movement of the silicon nitride rotor and the U-shaped silicon carbide rod heater heating system, which can be rotated at 90° horizontally. The hydraulic system is relatively stable. positioning accuracy.
Heating system
The heating system uses an electric heater, and the U-shaped silicon carbide rod covers the cylindrical silicon carbide or silicon nitride protective tube. There is a thermocouple for temperature measurement inside the tube, which can realize automatic temperature control, and the power can be adjusted arbitrarily in the range of 2 kW ~ 26 kW.
The temperature control system uses a more advanced power integrated unit to achieve fully automatic control to avoid the popularity of the lack of bumpers when the heater is turned on and off.
U-shaped silicon carbide rod heaters are often affected by the main current during frequent on-off processes.
The heater in the non-buffer stage is easy to age and has a short life.
Melt Aluminum Degassing process
Inert gas storage tank → online degassing device gas control cabinet → graphite rotor nozzle → processing aluminum alloy melting → purification and degassing treatment
The working principle of Aluminum Degassing is to increase the surface area of nitrogen that contacts the metal. A larger surface area will increase the transfer rate of the metal to the inert gas. The smaller the bubble size for a given gas volume, the larger the surface area. Smaller bubbles interfere with the melt surface and reduce the pickup of additional hydrogen in the humid atmosphere.
No Comments