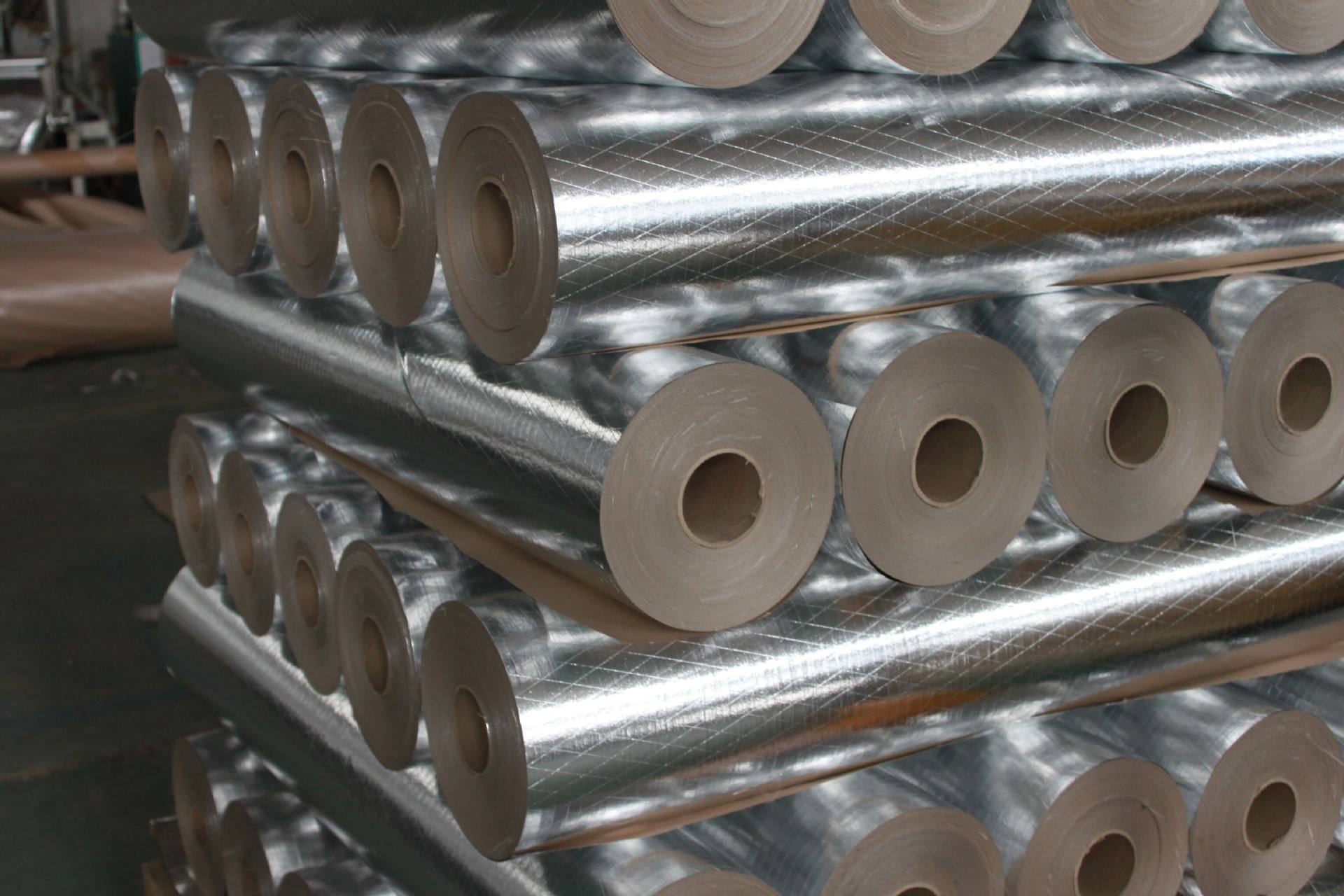
04 8月 Metal Foam Filters
Metal Foam Filters remove non-metallic inclusions in the aluminum alloy melt, and adopt furnace flux treatment. The technology of ceramic foam filter outside the furnace has been widely used in China.
The smelting of aluminum alloy is the first step in the aluminum alloy processing process, and it is also a crucial link. Reflected in the alloying, purification, and refinement processing technology of the smelting process.
Aluminum foil material has been widely used in many fields because of its light weight, corrosion resistance and good electrical conductivity.”
The ultra-thin double zero aluminum foil with a thickness of less than 0.005 mm has become the goal and direction that modern aluminum hall processing companies strive to seize the market and improve efficiency.
To obtain high-quality ultra-thin double zero aluminum foil products with a small number of pinholes and high yield, the basic quality of aluminum foil blanks must be strictly controlled.
Metal Foam Filters are a key process in the production of aluminum foil blanks, and are the prerequisite and guarantee for processing high-quality double zero aluminum foil. The impact on the quality and yield of ultra-thin double zero aluminum foil is profound.
When the new filter plate is first used, the slightly larger inclusion particles in the aluminum melt may pass through the pores of the ceramic filter plate. These “large particles” inclusions are inherited in the cast-rolled billet and affect its inherent quality.
When the filter plate is used for a period of time, some small impurity particles will be adsorbed in its pores. As the amount of filtration of aluminum liquid does not gradually increase, the adsorbed particles in the pores of the filter plate continue to gather, so that the pores of the filter plate become smaller and the filtering effect is improved. .
But when the amount of impurities adsorbed by the filter plate is so large that it blocks the pores of the filter plate, the filtering effect begins to decrease, and the quality of the cast-rolled billet is correspondingly reduced.
It can be seen from the test pinholes that the two-stage filter plate can well remove the small particle inclusions in the aluminum melt, and has a better purification effect on the aluminum melt.
Test from Kunming Metallurgical Research Institute
The 1235 aluminum liquid refined by high-purity nitrogen in the holding furnace is further purified outside the furnace by an online degassing device, and then filtered and purified outside the ceramic plate furnace to enter the casting-rolling mill to produce cast-rolling billets.
The ceramic plate filtering method used is a two-stage filter box, which is 30PPi days and 40/50PPi mesh foam ceramic two-stage filter plates. The aluminum liquid needs to pass through a first-stage filter before flowing into the front box.
The filter plate can effectively block metal and non-metal inclusions and bubbles in the aluminum melt, play a role in purifying the aluminum melt, and provide a basic guarantee for obtaining high-quality cast-rolled blanks.
Casting ingredients are 5t per roll.
Metal Foam Filters has a direct relationship between the clean quality of molten aluminum and the amount of molten aluminum filtered by the ceramic filter plate. Therefore, in order to process high-quality ultra-thin aluminum foil, it is necessary to use the cleanest molten aluminum to produce cast-rolled billets.
The aluminum foil cast-rolled billet between 26 t and 55 t produced after the new filter is used is the preferred billet for the production of ultra-thin aluminum foil.
Sorry, the comment form is closed at this time.