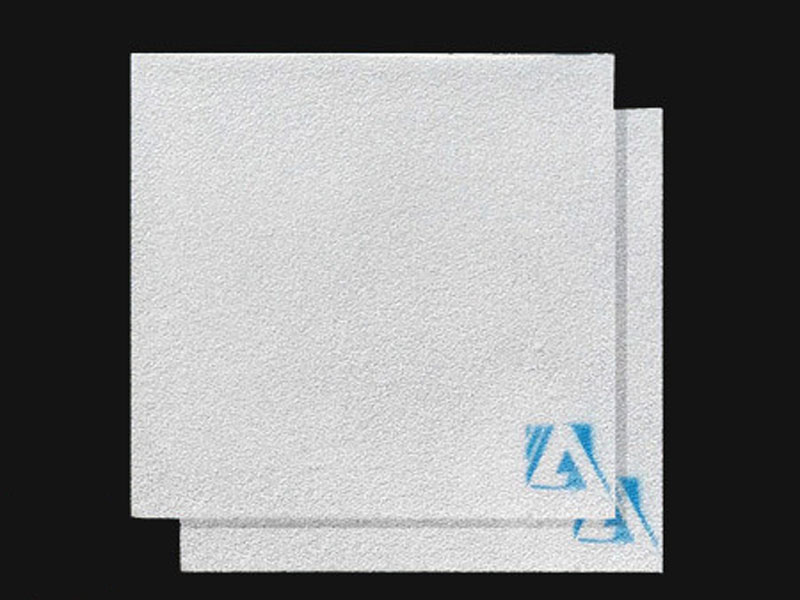
03 9月 molten aluminium Ceramic Filter Foam
molten aluminium Ceramic Filter Foam
molten aluminium Ceramic Filter Foam used in the manufacture of castings 已安装的插件brings undeniable benefits, which are determined by quality and economic indicators.
Improving the quality of manufactured products, which is determined by the ideal external surface and the purity of the internal structure of the metal, makes it possible to produce castings of more complex and thin-walled structures.
The economic benefits from the introduction of filtering technologies are to reduce the production costs of machining castings, reduce the consumption of melt, and most importantly, significantly reduce the percentage of rejects.
Due to the above mentioned advantages, filtering technology has been continuously used in almost all foundries in Europe.
Here the question of the need for filtering is not posed, but the problems of increasing the efficiency of filtering technologies are solved.
Such efficiency depends on the correct selection of the filter size for a particular technology, its placement in the gate system, the correct design of the gate system itself, and also the observance of the necessary conditions throughout the entire technological process.
Why is it necessary to Ceramic Foam Filter?
Filtration helps to eliminate many of the shortcomings of castings, achieve their high quality, and also solve many production problems.
This is manifested in the following:
Increasing the uniformity of the internal structure of the metal.
Improvement of mechanical properties.
Elimination of a number of metallurgical deficiencies (gas sinks, porosity, leaks).
Improving surface quality.
Significant improvement in the machinability of products.
The most important task of filtering is to eliminate non-metallic inclusions that most affect the quality of the finished casting. The main sources of inclusions are:
Slags (primary and secondary).
Metal oxidation products.
Molding materials and erosion products of molds and cores.
Remains of refiners, molten coatings, insoluble parts of modifiers, etc.
In the casting process, inclusions are solid, liquid and semi-liquid (viscous). Filter capture of these impurities is promoted not only by its foamy structure, but also by the physical properties of the ceramic material from which the product is made.
At high temperatures, both solid and liquid particles adhere to the surface of the filter material. Examples of trapping inclusions are shown in the figure. In order to meet modern requirements for foundry products, the purity of the melt is a prerequisite.
Even minor inclusions can lead to cracks or surface defects, which makes the final product unusable. Effective cleaning of aluminum melts in the foundry is ensured by ceramic foam filters.
Ceramic foam filters are designed to ensure high purity of casting aluminum and its alloys at metallurgical enterprises, as well as for filtering aluminum castings in foundries.
Filters are made in the form of a truncated pyramid; main dimensions are in inches. The beveled side walls serve as a supporting surface for landing in a ceramic filter box.
Ceramic foam filters for aluminum are supplied with a seal around the edges to ensure that they fit into the filter box housing to prevent metal from passing by the filter. Two different sealing materials are possible: a thermally expanding seal and a lint-free seal.
Sorry, the comment form is closed at this time.