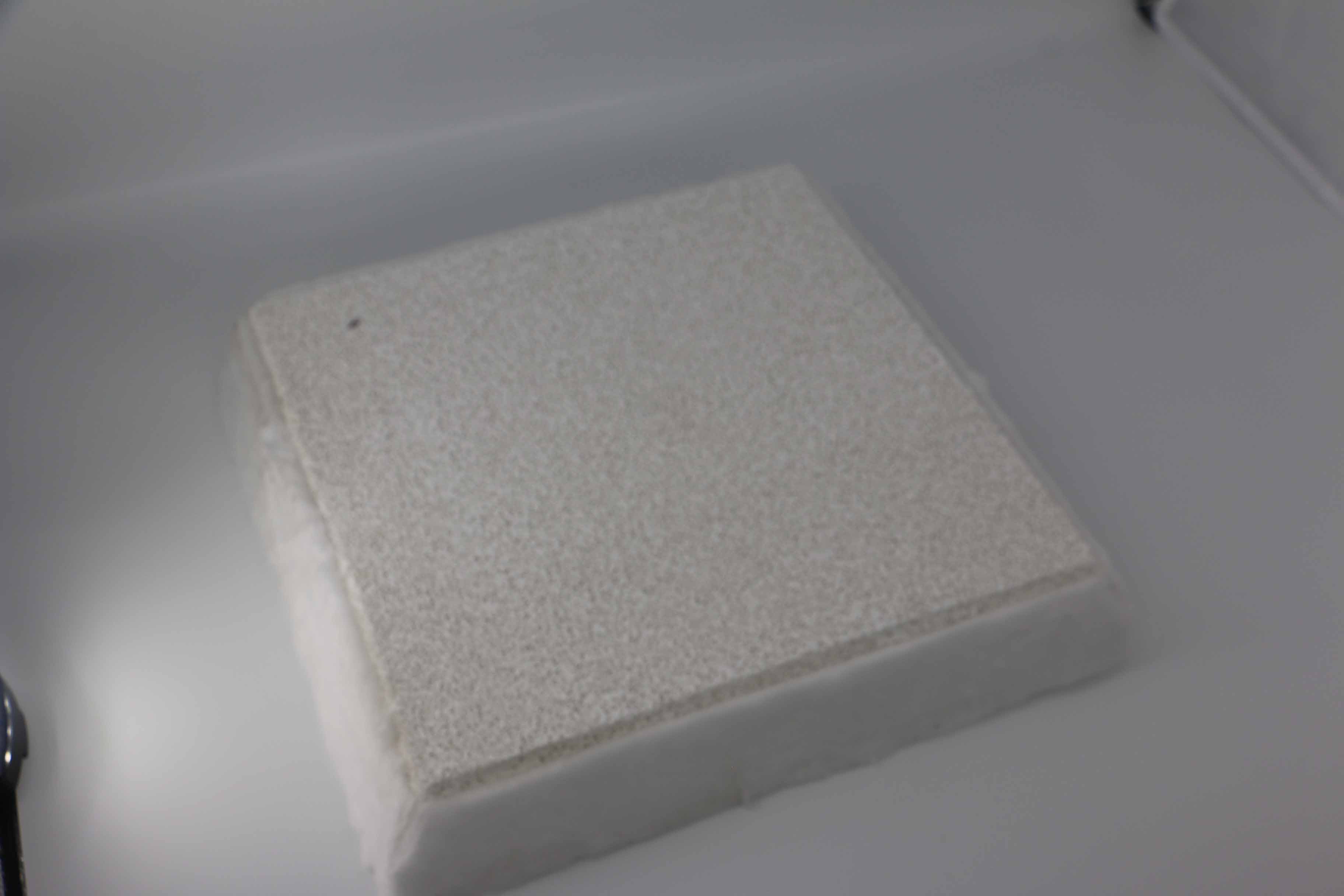
24 7月 Molten aluminium Filtration
Molten aluminium Filtration filtration mechanism
Sieving
Like a sieve, it prevents the inclusion of particles and their agglomerates whose size is larger than the pore size of the filter surface.
Cake filter
After sieving, many inclusions larger than the filter hole are captured at the inlet of the filter.
As the number of captured inclusions increases, a “filter cake” composed of large inclusions is formed on the surface of the inlet end of the filter.
The “filter cake” makes the liquid thinner, so that the inclusions smaller than the pore size of the filter are also partially captured on the “filter cake”.
Deep bed filtration
Inside the ceramic foam filter, the path the melt flows through is tortuous, and there is even cross-flow reversal in a small local area.
This has two main functions
1. It can greatly increase the probability of inclusion particles contacting the filter
2. Speed ??up the flow rate and flow direction change of the melt, so that the small inclusions in the melt can be caught in a corner after being collided.
Function of Molten aluminium Filtration
Removal of impurities
Purify the aluminum alloy liquid, the viscosity of the aluminum alloy liquid decreases after filtration, and the fluidity of the aluminum alloy liquid increases by 10%-15%. Therefore, filtration improves the filling capacity of aluminum alloy liquid.
The flow of the aluminum alloy liquid before filtration is turbulent, and after filtration, it becomes laminar (the flow channel of the foam ceramic filter is twisted and turned), which reduces air entrainment and secondary slagging.
As the filtration progresses, the filtration mechanism changes from sieving, filter cake to deep bed filtration, and the purity of the aluminum alloy after filtration is getting higher and higher (without exceeding the maximum filtration capacity of the ceramic foam filter).
For example, the aluminum alloy liquid in the combustion chamber at the bottom of the cylinder head is the purest.Molten aluminium Filtration please contact sales@adtechamm.com
Reduced scrap rate of parts
Improved part cutting performance
The mechanical properties of materials are significantly improved, especially the elongation.
Selection of Molten aluminium Filtration Foam Ceramic Filter Size
1.Calculate the minimum cross-sectional area of ??the sprue.
2. Calculate the sum of the cross-sectional area of ??the runner and the sum of the cross-sectional area of ??the inner runner.
3. Determine the placement and number of filters.
4.According to the filtering speed of the filter per unit area, the filtering capacity of the filter per unit area, the actual pouring speed and the weight of the aluminum alloy liquid passing through the filter and the purity of the aluminum alloy liquid, determine the size of the filter (such as aluminum alloy If the liquid is too impure, multi-stage filtration is required).
Namely: the filtration speed of the filter> the pouring speed of the aluminum alloy liquid the filtration capacity of the filter> the amount of inclusions in the aluminum alloy liquid
Usually: the filter area of ??the filter is 2.54 times the cross-sectional area of ??the runner.
The area where the metal passes through the filter should be large enough to not affect the pouring speed and pouring time of the mold due to the placement of the filter. Therefore, the process should be considered: slag collection factors, filter factors, and damping factors. Therefore, the ratio of the area of ??the cross section at the filter to the area of ??the normal runner is 2.5-4.0:1.
There should be a large enough space before and after the filter to collect the inclusions and also facilitate the smooth flow of molten metal. Molten aluminium Filtration please contact sales@adtechamm.com
Use ceramic foam filter, in order to prevent filtering inclusions from affecting the flow of metal, the filter size is selected according to the amount of molten metal filtered.
If the whole box of aluminum water is too much or too dirty, you can branch on the runner and use multiple filters.
Three placement filters
Horizontally
Top-down: The best way for the molten metal to pass through the filter from bottom to top. In the initial stage of filtration, the filtered liquid has a shower phenomenon. As the liquid below fills up, the shower phenomenon disappears.
Bottom-up: the filtered liquid flow without showering.
Vertical placement
At the beginning of filtration, the utilization area of ??the filter is small. There is no shower phenomenon in the filtered liquid flow.
Precautions
1.Improper use of ceramic filters, the effect is worse than using other filters.
2. The system design must ensure that all the aluminum alloy liquid passes through the filter. If part of it does not pass, the aluminum liquid is not pure, and turbulence is generated, which entrains gas and creates slag. Molten aluminium Filtration please contact sales@adtechamm.com
3. The filter area of ??the filter should be large enough to not affect the flow rate of the aluminum alloy liquid (the minimum flow rate should be located at the smallest section of the sprue)
4. There should be enough space before and after the filter to collect the inclusions.
5. The aluminum alloy liquid should be smelted in the melting furnace (to avoid oxidation and slag removal) and the refining and slagging and degassing of the holding furnace should be done. Because the filtering capacity of the filter is limited, too dirty aluminum alloy liquid will cause the last filtered aluminum alloy liquid to be more dirty than the first filtered aluminum alloy liquid.
6.The ceramic filter should be baked before use.
7. The debris on the dry ceramic filter should be blown off and should not be brought into the sprue.
8. The ceramic filter should be placed correctly to avoid crushing.
Sorry, the comment form is closed at this time.