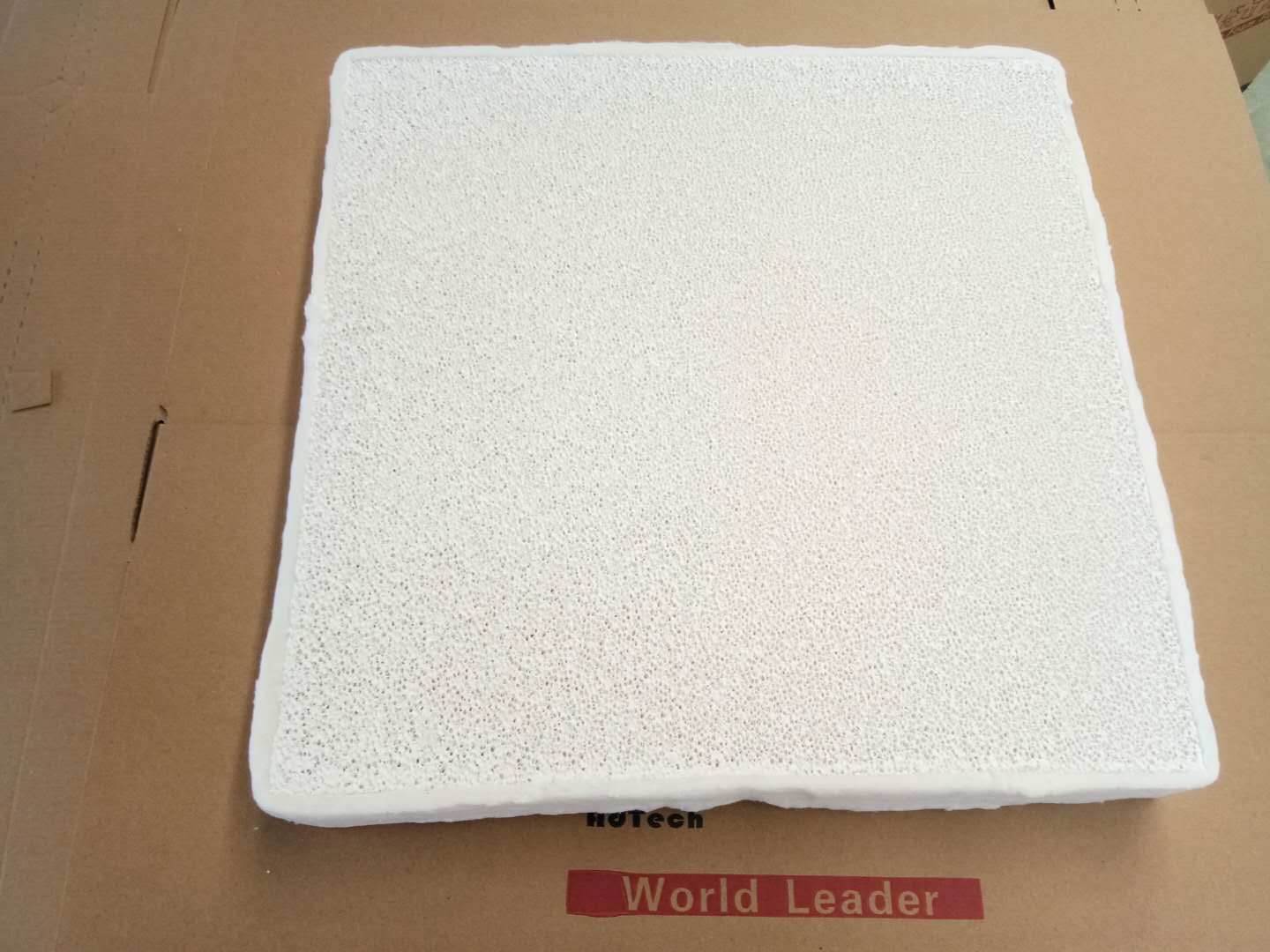
20 10月 Molten Aluminum Filter Bangladesh
Molten Aluminum Filter Bangladesh removes all kinds of inclusions in the aluminum water, and the fineness can reach the micron level. The molten aluminum becomes a smooth laminar flow, which is conducive to washing, has good mechanical strength and chemical stability, and has superior corrosion resistance.
Stable filtration effect can be achieved by strictly controlling the pore size and pore size.
The ceramic foam filter plate is surrounded by a sealing ceramic fiber lining, which helps to seal the filter and the filter box to ensure that there is no side flow of molten metal.
Molten Aluminum Filter Bangladesh is mainly used in the purification process of aluminum and aluminum alloy production. They are also used as various gas-solid and liquid-solid separation media, catalyst carriers, burners, sound absorption and environmental protection.
Molten Aluminum Filter can effectively remove various fineness of micro-inclusions in aluminum water, so that the aluminum water has a smooth laminar flow, which is very suitable for filling.
It has good mechanical strength and chemical stability, as well as excellent aluminum cleanliness.
Strictly control the pore size and through-hole ratio to achieve stable filtration.
The ceramic foam filter plate is surrounded by a sealed thermally-expandable ceramic fiber gasket, which helps to seal the filter plate to the filter box to ensure that no metal liquid bypasses.
Parameters of ceramic filter in aluminum and aluminum alloy production
178×178×50mm, 230×230×50mm, 305×305×50mm, 381×381×50mm, 432×432×50mm, 508×508×50mm, 584×584×50mm,
There are mainly seven kinds of foam ceramic filter plate products. Other specifications and models are required.
30ppi 40ppi cast filter usually uses polyurethane foam as a carrier, immersed in a ceramic slurry made of fine powder (such as refractory aggregate sintering aids, binders and water), and then extrudes the excess slurry. The ceramic material around the foam fiber is dried, fired and sintered at a high temperature, and finally the foam ceramic product remains.
Because the casting temperature of the casting alloy is different, the foam ceramic filter made of refractory material should be used when casting.
In order to solve this problem, a simple filter made of wire mesh, perforated steel plate, etc. is inserted into the gating system to remove impurities from the beginning.
Used for internal filters with two-dimensional structures such as silicate needle fibers and boron nitride fibers.
Today, ceramic foam filters use pore sizes to mechanically block larger particles of mixed oxide, and filter cakes to filter out smaller mixed oxide particles.
It also has the functions of adsorption and rectification. The production line using ceramic foam filters greatly increases the output of castings.
The Aluminum Industry Association of India (AAI) urges the government to give priority to the supply of coal to the aluminum industry to avoid large-scale losses.
“Any power outage in the electrolytic aluminum plant will have a catastrophic impact. It will take at least 12 months for a series of electrolytic cell shutdowns to resume, which will cause more than 800,000 people to lose their jobs, and banks will face debt risks of more than 1 billion rupees. And an additional country’s foreign exchange losses of 90,000 crore,” said the Aluminum Industry Association of India (AAI).
The uninterrupted power demand of the Indian aluminum industry is approximately 9.4 GW (9,400 MW), which accounts for less than 6% of the country’s total demand (145 GW) and the total energy traded on the Indian Energy Exchange (7.6 GW in 2021) ) Of 123%. Therefore, technically speaking, it is not feasible to obtain such a huge amount of power from the grid.
The report stated that the aluminum industry cannot import electricity, while the national aluminum industry needs 150,000 tons of domestic coal every day.
The Coal Industry Association of India stated that the association needs to resume the continuous supply of coal immediately.
According to data records: India is the largest aluminum producer in Asia (except China), and its rich bauxite resources provide a strong resource guarantee for the development of the country’s aluminum industry. Statistics show that as of the end of 2020, India’s total alumina production capacity was 7.13 million tons per year, accounting for 45% of Asia (except China) production capacity and 10% of total overseas production capacity. The primary aluminum production capacity is 4.07 million tons, accounting for 33% of Asia (except China) production capacity and 12.6% of total overseas production capacity.
No Comments